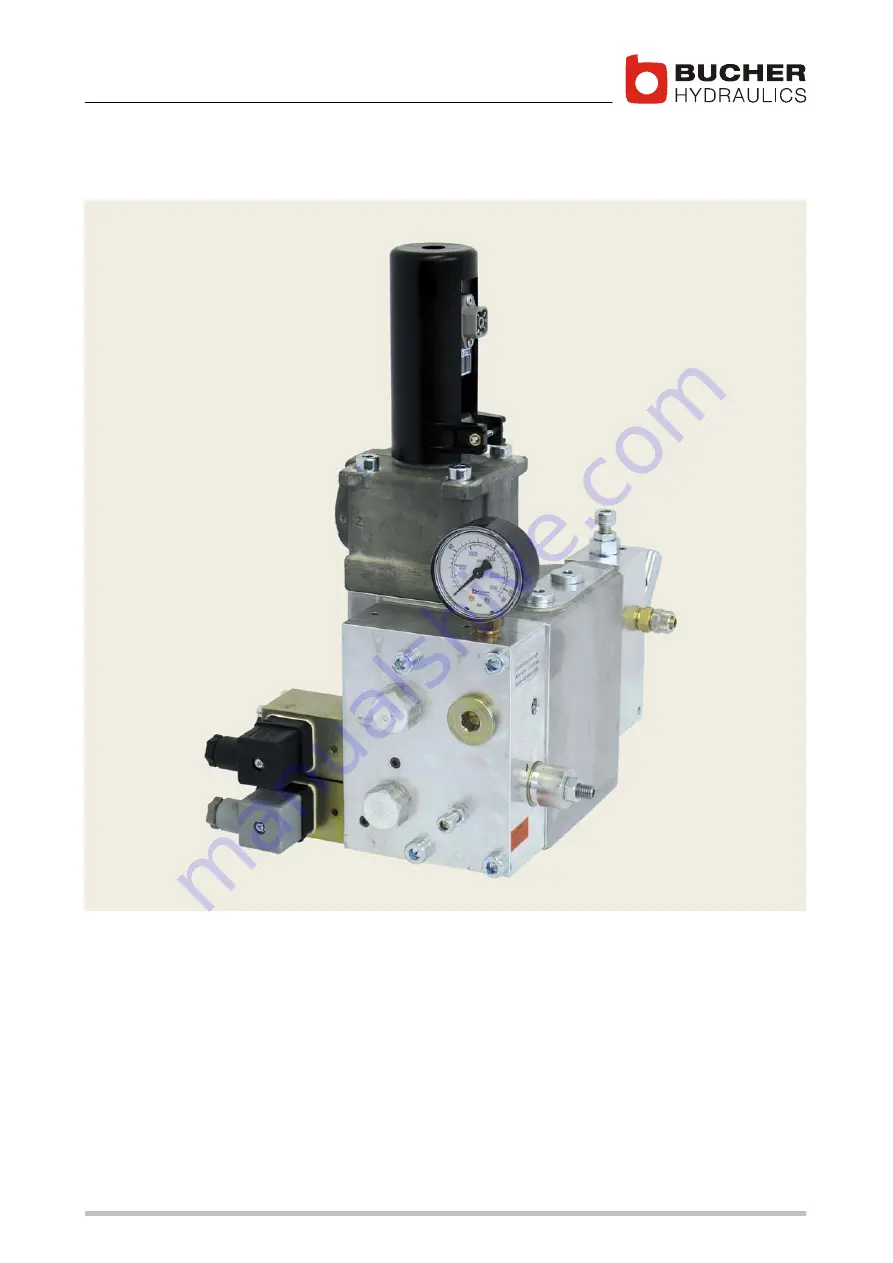
C−LRV Lift Control Valve, Size 175 / 350 / 700
NTA−2 power supply unit and C−DELCON
Issue: 08.08
Installation and startup guide
1/92
Classification: 450.500.500
Reference: 300−I−9010212−E−10/08.08
C−LRV Lift Control Valve, Size 175 / 350 / 700
NTA−2 power supply unit and C−DELCON
Issue: 08.08
Installation and startup guide
1/92
Classification: 450.500.500
Reference: 300−I−9010212−E−10/08.08