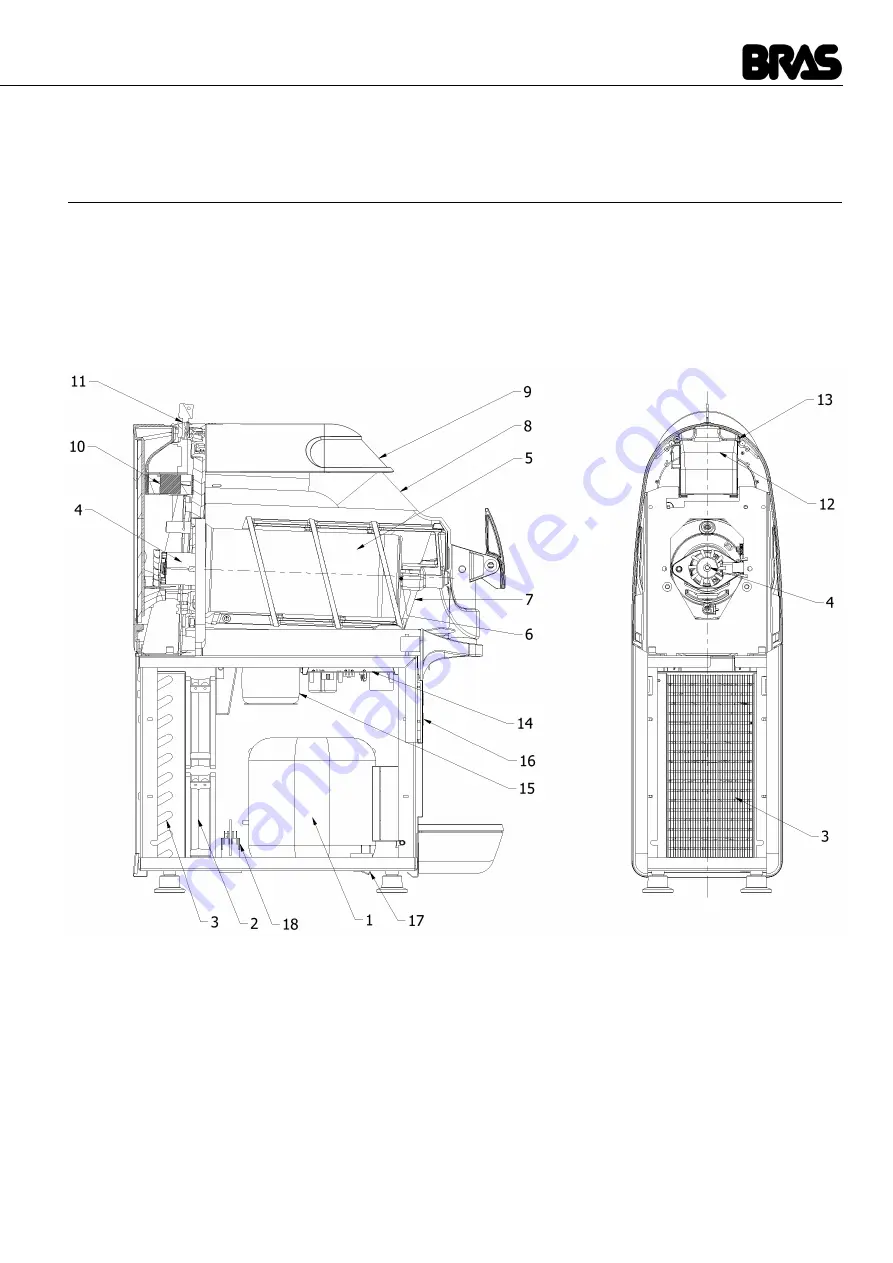
29
This Service Manual is intended solely for internal use by the manufacturer and his technical support team or other simi-
larly qualified persons, in order to prevent any risks.
This manual describes the procedures for adjustment, maintenance and repair of the dispenser. For information regarding
ordinary usage by the operator, please refer to the Instruction Manual provided with each dispenser.
1 APPLIANCE’S DESCRIPTION
This dispenser is designed for the production of iced or frozen drinks such as crushed ice drinks, ice creams and sorbets. The lower
half of the dispenser contains the cooling system, which consists of a compressor (1), a condenser (3), the related fans (2) and a
solenoid valve to open and close the cooling circuit. The lower half of the dispenser also contains the circuit boards designed to
control operation (14) and (16) and the power supply transformer (15) for both the circuit boards and the geared motor to drive the
mixers.
The upper half of the dispenser contains the transparent tank (8) designed for the food product, which in turn contains the mixer (7)
and the evaporator cylinder (5) which is the unit that chills the product. In addition, the rear of the dispenser houses the electric motor
(4) and the geared motor which drives the mixer, the tank defrosting fan (10) and any LED lamps.
figure 1
The dispenser also features a main ON/OFF switch situated on the left-hand side of the frame underside. In addition, each tank is
fitted with a control panel, situated under the dispenser tap, the functions of which are described below.
BCREAM HD 1/2/3
The model BCream HD, in production starting from year 2014, has the following differences from the previous model:
More powerful mixing system
Cup sensor for ease of dispensing
Graphic display showing a larger number of messages
Improved software for better product handling
Timer for operation programming