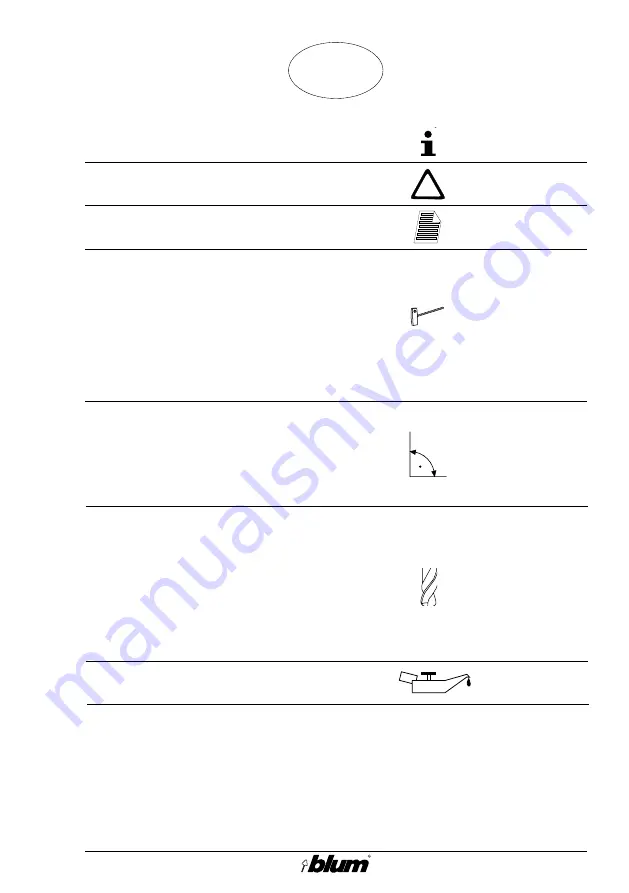
1
CONTENTS:
A
Reading instructions
B
Safety instructions!
C
Description of parts
D
Preparing PRO-CENTER 2000
• Mounting large worktable
• Altering control unit attachment
• Mounting centre squares to
PRO-CENTER 2000
•
Increasing drilling accuracy
E
Adjusting MZK.2880 to ruler
•
Setting drilling head at a right angle
to ruler
•
Setting drilling head parallel to ruler
F
Working with MTZ.2880
•
System 32
•
Carcase profiles
•
Dowels
- Tops and bases
- Shelves
G
Maintenance
2
3
5
6
7
7
8
10
14
18
19
20
20
23
24
PAGE:
EN
!
Summary of Contents for PRO-CENTER 2000
Page 25: ...25 ...
Page 26: ...26 Notes ...
Page 27: ...27 Notes ...
Page 28: ...28 Id Nr 173 399 0 Printed in Austria BA 17 02 EN 01 2002 BAU0003173112 IDX05 ...