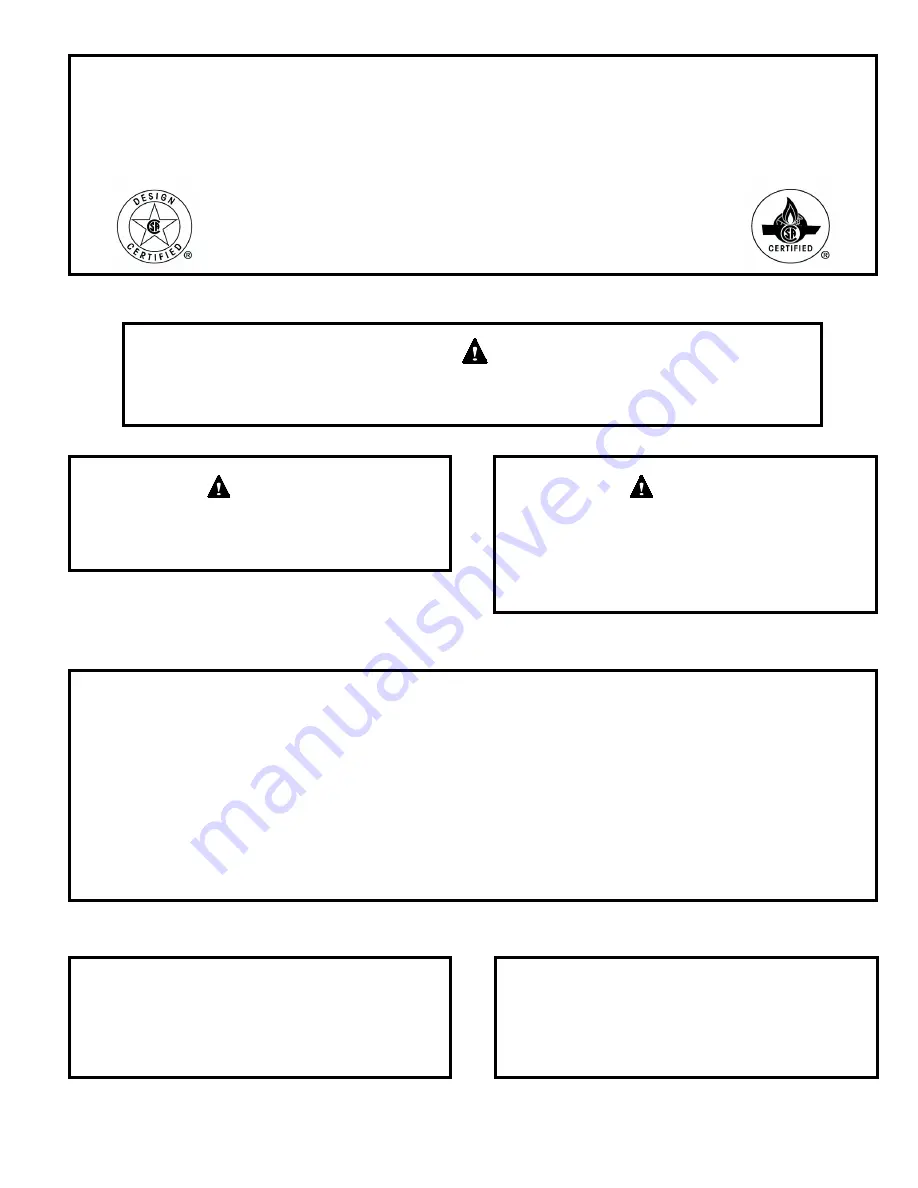
507581-04
Issue 1933
Page 1 of 59
This manual must be left with the homeowner for future reference.
INSTALLATION INSTRUCTIONS
A96UH2E
Warm Air Gas Furnace
Upflow/Horizontal Left Air Discharge
Direct Vent & Non-Direct Vent
This is a safety alert symbol and should never be ignored. When you see this symbol on labels or in
manuals, be alert to the potential for personal injury or death.
Improper installation, adjustment, alteration, service
or maintenance can cause property damage, personal
injury or loss of life. Installation and service must be
performed by a licensed professional installer (or
equivalent), service agency or the gas supplier.
WARNING
As with any mechanical equipment, personal injury can
result from contact with sharp sheet metal edges. Be
careful when you handle this equipment.
CAUTION
Save these instructions for future reference
(P) 507581-04
*P507581-04*
Manufactured By
Allied Air Enterprises LLC
A Lennox International, Inc. Company
215 Metropolitan Drive
West Columbia, SC 29170
Table of Contents
Unit Dimensions ............................................................
Parts Arrangement.........................................................
A96UH2E Gas Furnace .................................................4
Shipping and Packing List .............................................4
Safety Information .........................................................4
General ..........................................................................
Combustion, Dilution & Ventilation Air ...........................7
Installation ...................................................................10
Filters ...........................................................................14
Duct System ................................................................14
Venting.........................................................................
Condensate Piping ......................................................
...................................................................37
Electrical ......................................................................40
Blower Performance ....................................................49
Unit Start-Up ................................................................
Other Unit Adjustments................................................
Service.........................................................................
Planned Service ..........................................................57
Repair Parts List ..........................................................58