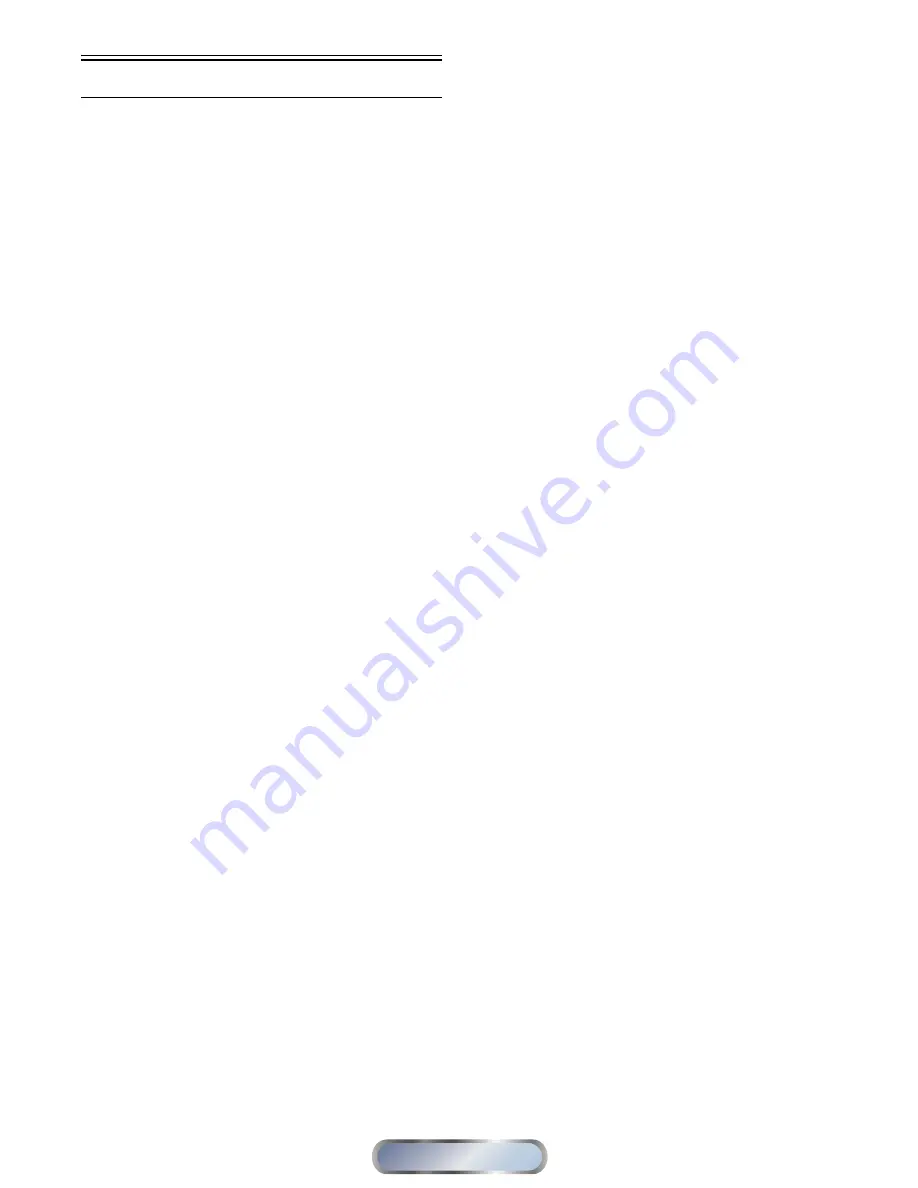
FOREWORD
This Arctic Cat Service Manual contains service, maintenance, and troubleshooting information for the 2011 Arc-
tic Cat 350/425 ATV models. The complete manual is designed to aid service personnel in service-oriented appli-
cations.
This manual is divided into sections. Each section covers a specific ATV component or system and, in addition to
the standard service procedures, includes disassembling, inspecting, and assembling instructions. When using this
manual as a guide, the technician should use discretion as to how much disassembly is needed to correct any given
condition.
The service technician should become familiar with the operation and construction of each component or system
by carefully studying the complete manual. This manual will assist the service technician in becoming more aware
of and efficient with servicing procedures. Such efficiency not only helps build consumer confidence but also saves
time and labor.
All Arctic Cat ATV publications and decals display the words Warning, Caution, Note, and At This Point to
emphasize important information. The symbol
! WARNING
identifies personal safety-related information.
Be sure to follow the directive because it deals with the possibility of severe personal injury or even death. A
CAUTION
identifies unsafe practices which may result in ATV-related damage. Follow the directive because it
deals with the possibility of damaging part or parts of the ATV. The symbol
NOTE:
identifies supplementary
information worthy of particular attention. The symbol
AT THIS POINT
directs the technician to certain
and specific procedures to promote efficiency and to improve clarity.
At the time of publication, all information, photographs, and illustrations were technically correct. Some photo-
graphs used in this manual are used for clarity purposes only and are not designed to depict actual conditions.
Because Arctic Cat Inc. constantly refines and improves its products, no retroactive obligation is incurred.
All materials and specifications are subject to change without notice.
Keep this manual accessible in the shop area for reference.
Product Service and
Warranty Department
Arctic Cat Inc.
© 2010 Arctic Cat Inc.
December 2010
®™ Trademarks of Arctic Cat Inc., Thief River Falls, MN 56701
Manual
Table of Contents
For Discount Arctic Cat Parts Call 606-678-9623 or 606-561-4983
www.mymowerparts.com