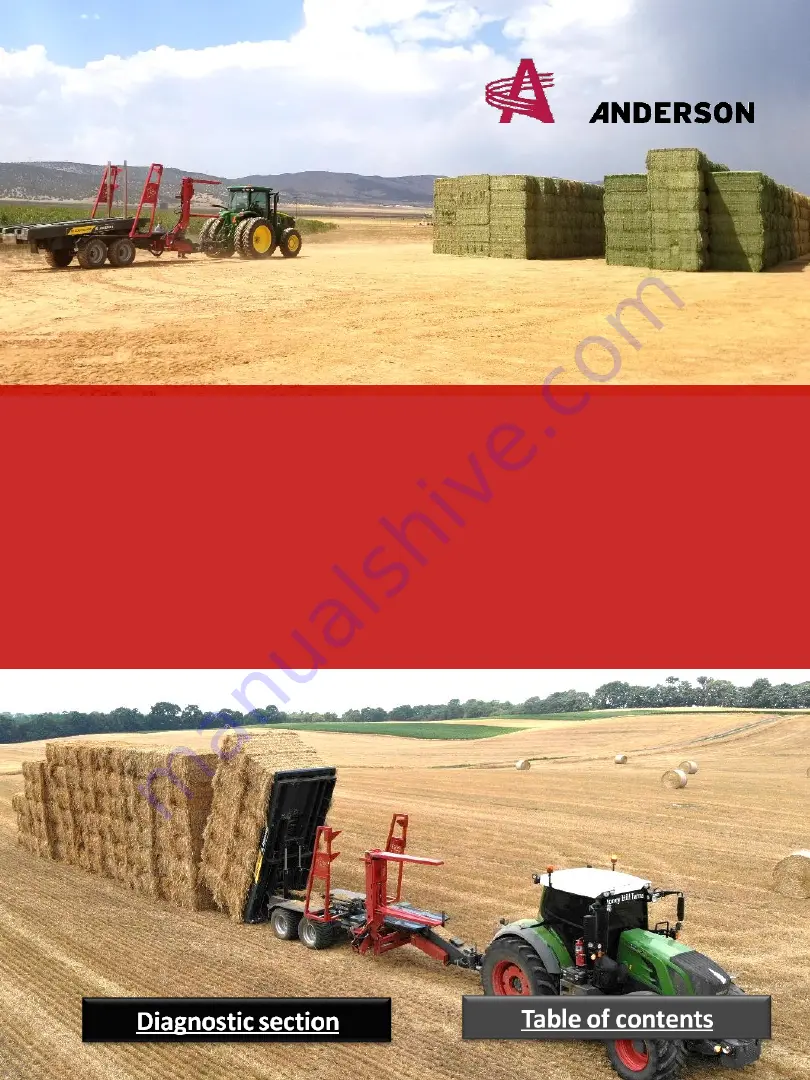
DIAGNOSTIC GUIDE FOR STACKPRO
When navigating the pages you will see buttons that send you to the
corresponding procedures / sections of the troubleshooting table. You can also
use the shortcut from the table of contents (procedures) to obtain a specific
procedure. At any time you may click on the Anderson logo at the top of any
page to return to this page.
Summary of Contents for STACKPRO 5400
Page 27: ...List of all sensor and their location 27 ...
Page 28: ...List of all sensor and their location 28 LS_BR_R LS_BR_E ...
Page 29: ...List of all sensor and their location 29 ...
Page 30: ...List of all sensor and their location 30 LS_CH ...
Page 53: ...List of all sensor and their location 53 ...
Page 54: ...List of all sensor and their location 54 LS_BR_R LS_BR_E ...
Page 55: ...List of all sensor and their location 55 ...
Page 56: ...List of all sensor and their location 56 LS_CH ...
Page 58: ...58 Electric diagram 7200 2 0 ...