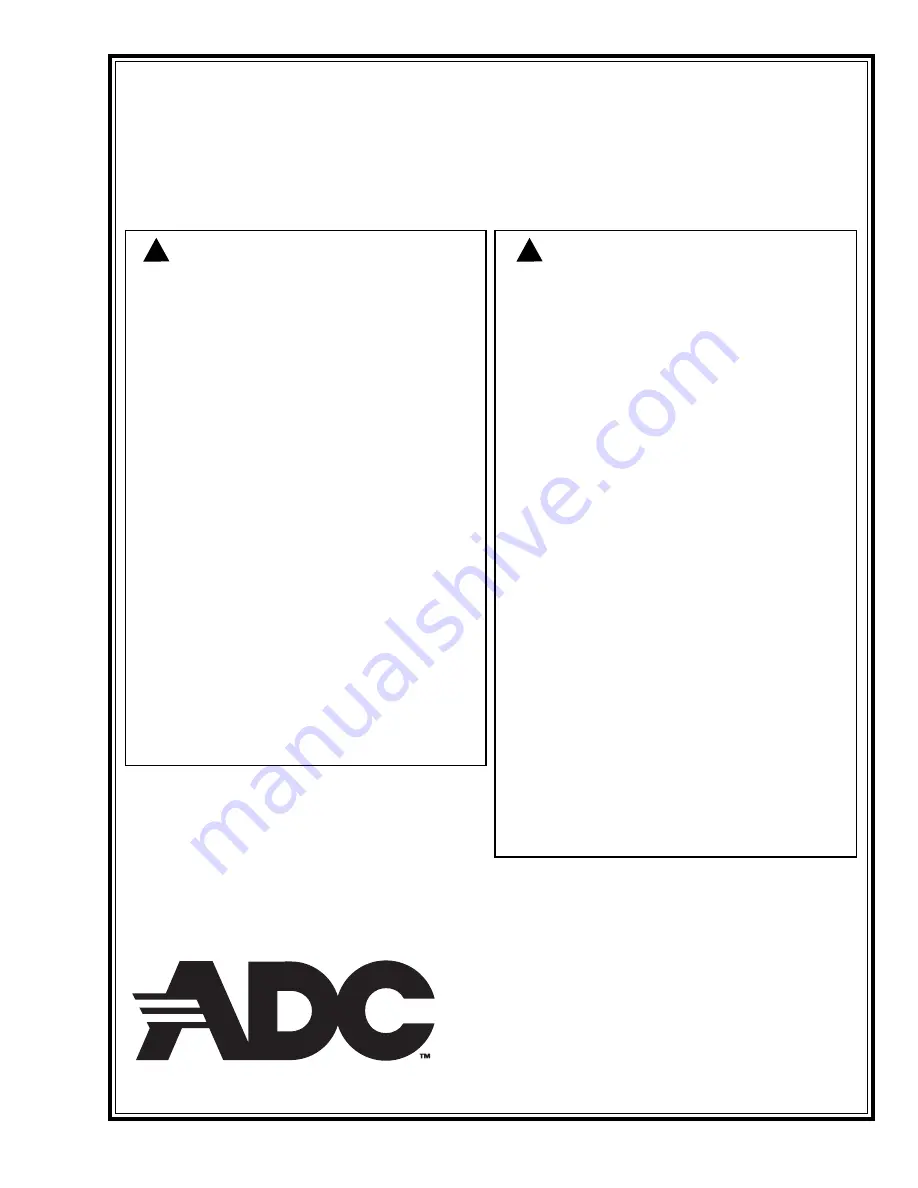
ADC Part No. 113363 - 37
ML-122 / MLG-122DR
Installation Manual
Phase 7 / Non-Coin / Dual Timer / F.S.S.
American Dryer Corporation
88 Currant Road, Fall River MA 02720-4781 USA
Telephone: +1 (269) 923-3000 / Fax: +1 (508) 678-9447
e-mail: [email protected] / www.adclaundry.com
AVERTISSEMENT:
RISQUE D’INCENDIE OU D’EXPLOSION
Le non-respect des avertissements de
sécurité pourrait entraîner des blessures
graves, la mort ou des dommages
matériels.
– N’entreposer pas et n’utilisez pas
d’essence ni d’autres vapeurs ou
liquides inflammables dans le voisinage
de cet appareil ou de tout autre appareil.
– QUE FAIRE SI VOUS SENTEZ UNE
ODEUR DE GAZ
●
●
●
●
●
Ne tentez pas d’allumer d’appareil.
●
●
●
●
●
Ne touchez à aucun interrupteur. Ne
vous servez pas des téléphones se
trouvant dans le bâtiment où vous
vous trouvez.
●
●
●
●
●
Évacuez la pièce, le bâtiment ou la zone.
●
●
●
●
●
Appelez immédiatement votre
fournisseur de gaz depuis un voisin.
Suivez les instructions du fournisseur.
●
●
●
●
●
Si vous ne pouvez rejoindre le
fournisseur de gaz, appelez le service
des incendies.
– L’installation et l’entretien doivent être
assurés par un installateur ou un service
d’entretien qualifié ou par le fournisseur
de gaz.
WARNING:
FIRE OR EXPLOSION HAZARD
Failure to follow safety warnings exactly
could result in serious injury, death or
property damage.
– Do not store or use gasoline or other
flammable vapors and liquids in the
vicinity of this or any other appliance.
– WHAT TO DO IF YOU SMELL GAS
●
●
●
●
●
Do not try to light any appliances.
●
●
●
●
●
Do not touch any electrical switch;
do not use any phone in your
building.
●
●
●
●
●
Clear the room, building or area of
all occupants.
●
●
●
●
●
Immediately call your gas supplier
from a neighbor’s phone. Follow
the gas supplier’s instructions.
●
●
●
●
●
If you cannot reach your gas
supplier, call the fire department.
– Installation and service must be
performed by a qualified installer, service
agency or the gas supplier.
!!!!!
!!!!!