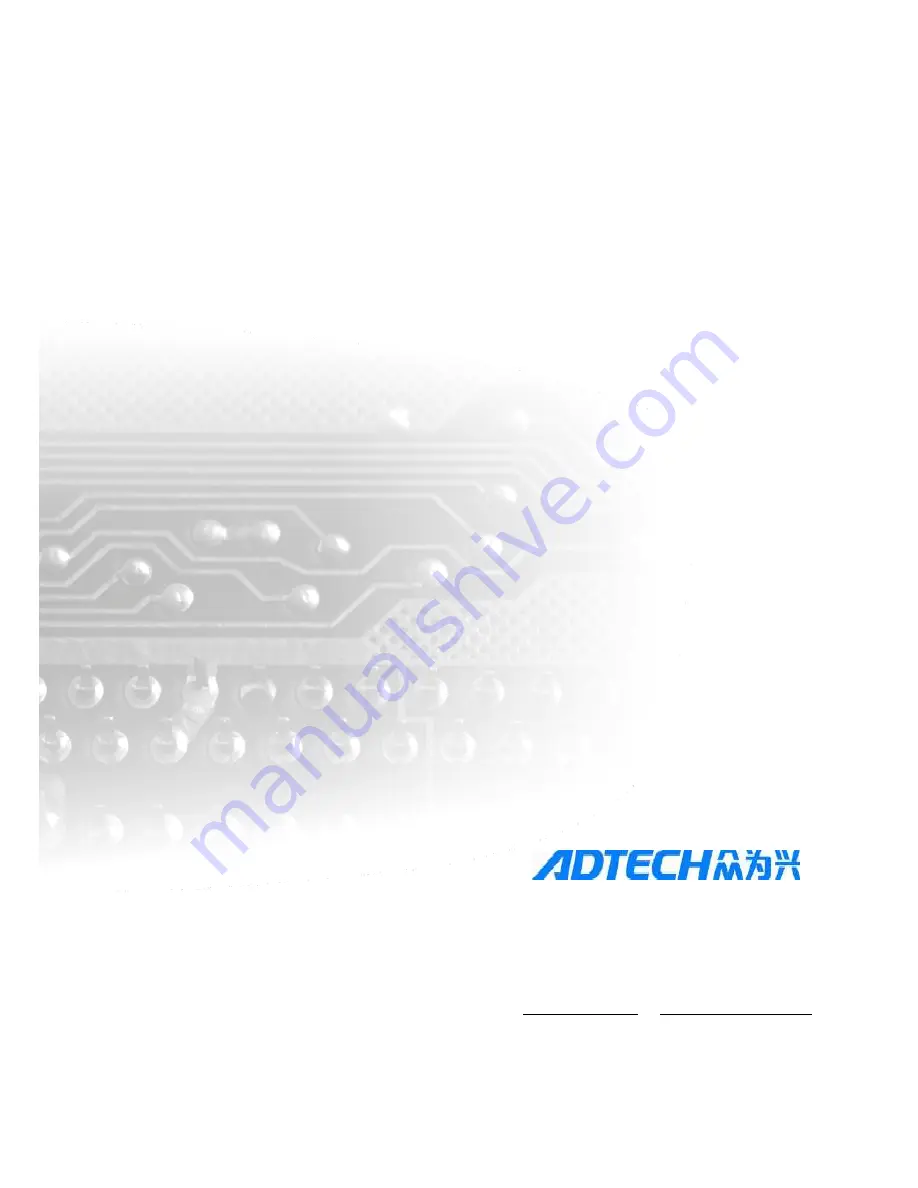
A
A
D
D
T
T
-
-
H
H
C
C
4
4
5
5
0
0
0
0
Flame / Plasma Cutting Machine CNC System
User’s Manual
Adtech (Shenzhen) CNC Technology Co., Ltd.
Add: F/5, Bldg/27-29, Tianxia IC Industrial Park, Yiyuan Rd, Nanshan District, Shenzhen
Postal code: 518052
Tel: 0755-26722719 (20 lines) Fax: 0755-26722718
E-mail: [email protected] http://www.adtechcn.com