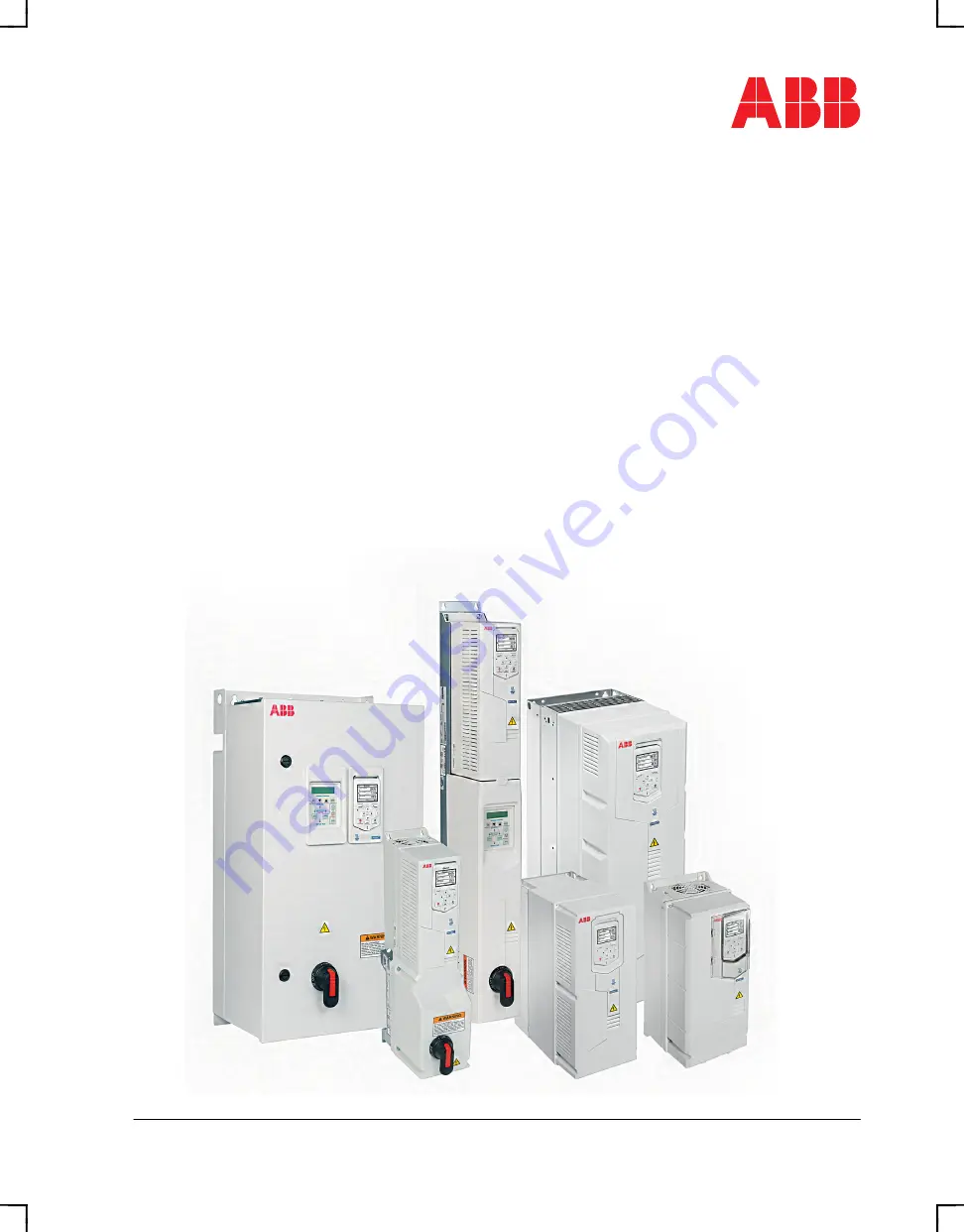
—
ABB DRIVES FOR HVAC
ACH580-01 drives
Installation, Operation and Maintenance
Manual (I, O & M)
ACH580-01 HVAC Drives (1...350 HP, 0.75...250 kW)
ACH580-BCR/BDR (1...350 HP, 0.75...250 kW)
ACH580-PCR/PDR (1...350 HP, 0.75...250 kW)
ACH580-VCR/VDR (1...60 HP, 0.75...45 kW)
ACH580_Inst_Op_Maint_Rev G.book Page 1