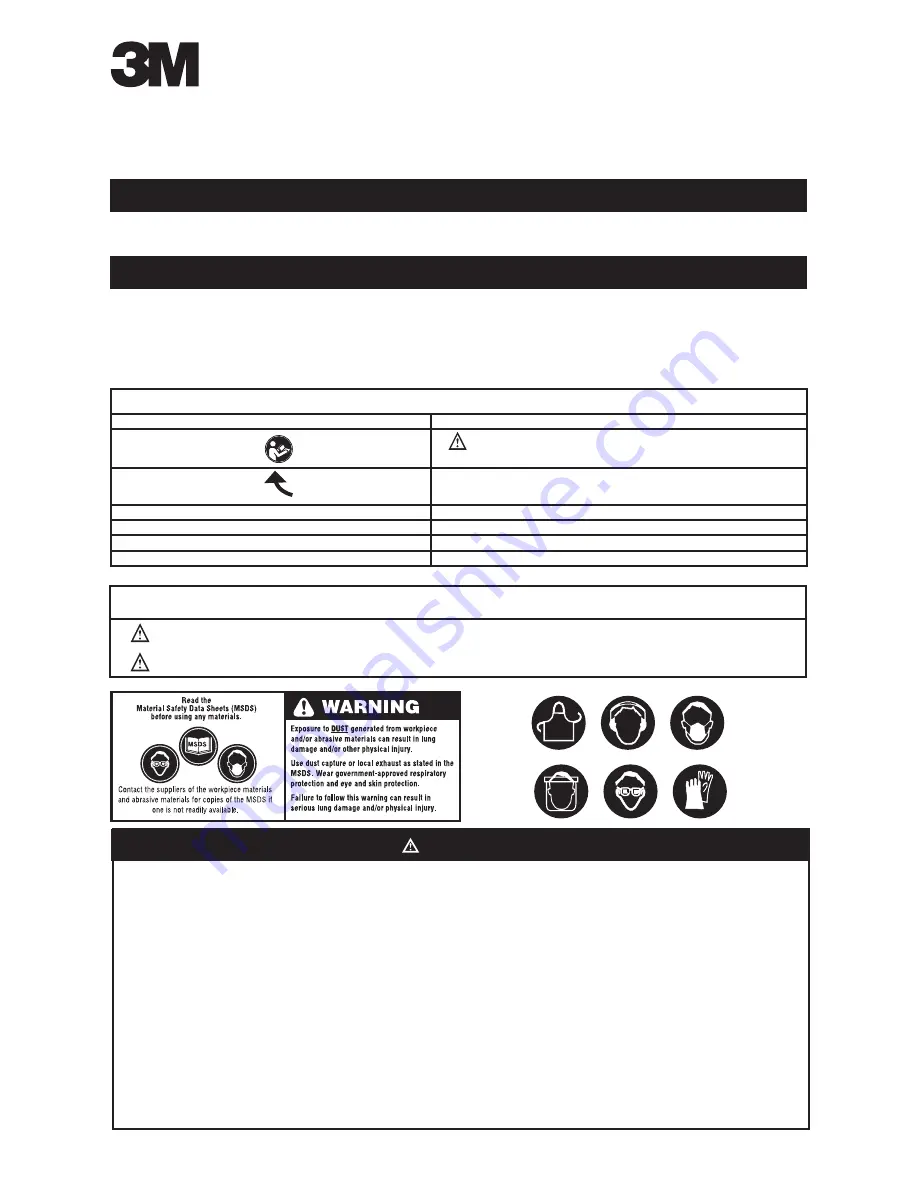
1
Important Safety Information
Intended Use
GRINDERS, TYPE-27 INSTRUCTION MANUAL
101 mm (4 in.) - 113 mm (4 1/2 in.)
12,000 RPM
Please read, understand and follow all safety information contained in these instructions prior to the use of this tool.
Retain these instructions for future reference.
These pneumatic tools are intended for use in industrial locations, and used only by skilled, trained professionals in accordance with the instructions in this
manual. These pneumatic tools are designed to be used with the appropriate size Type 27 Wheel for grinding metals. They should only be used for such grinding
applications and within their marked capacity and ratings. Only accessories specifically recommended by 3M should be used with these tools. Use in any other
manner or with other accessories could lead to unsafe operating conditions.
Do not operate tool in water or in an excessively wet application.
Do not use grinding wheels that have a Max RPM less than the marked RPM rating on the tool.
To reduce the risks associated with impact from abrasive product or tool breakup, sharp edges, hazardous pressure, rupture, vibration and noise:
• Read, understand and follow the safety information contained in these instructions prior to the use of this tool. Retain these instructions for future reference.
• Only personnel who are properly trained should be allowed to service this tool.
• Practice safety requirements. Work alert, have proper attire, and do not operate tools under the influence of alcohol or drugs.
• Operators and other personnel must always wear protection for eyes, ears, and respiratory protection when in the work area or while operating this
product. Follow your employer’s safety policy for PPE’s and/or ANSI Z87.1 or local/national standards for eyewear and other personal protective equipment
requirements.
• Wear leather apron or other protective apparel, taking into consideration the type of work being done.
• Never exceed marked maximum input pressure (90psi / .62Mpa / 6.2Bars).
• Proper eye protection must be worn at all times.
• Tool is not to be operated in the presence of bystanders.
• If you notice any abnormal noise or vibration when operating the product, immediately discontinue its use and inspect for worn or damaged abrasive
product or accessories. Correct or replace the suspect component. If abnormal noise or vibration still exists, return the tool to 3M for repair or replacement.
Refer to warranty instructions.
• Never operate this tool without all guards or safety features in place and in proper working order.
• Prior to use, ensure guard is oriented to protect the operator from flying fragments and is properly secured.
• Make sure the tool is disconnected from its air source before servicing, inspecting, maintaining, cleaning, and before changing abrasive product.
• Only use wheel retainers (flanges) and wheel arbors supplied by 3M.
• Never use this tool with Type 1 wheels or cut-off wheels.
WARNING
Original Instructions
Rev. 2/19/2015
Summary of device labels containing safety information
Marking
Description
WARNING:
Refer to Instruction Manual
Direction of Rotation
90psi / .62Mpa / 6.2Bars Max
Maximum Pneumatic Inlet Pressure
12,000 RPM
Maximum Rotational Speed
Use accessories rated at tool RPM or higher
Accessories Safety Note
Prolonged vibration may cause injury
Vibration Safety Note
Explanation of Signal Word Consequences
Indicates a potentially hazardous situation which, if not avoided, may result in death or serious injury and/or property damage.
Indicates a potentially hazardous situation which, if not avoided, may result in minor or moderate injury and/or property damage.
WARNING:
CAUTION: