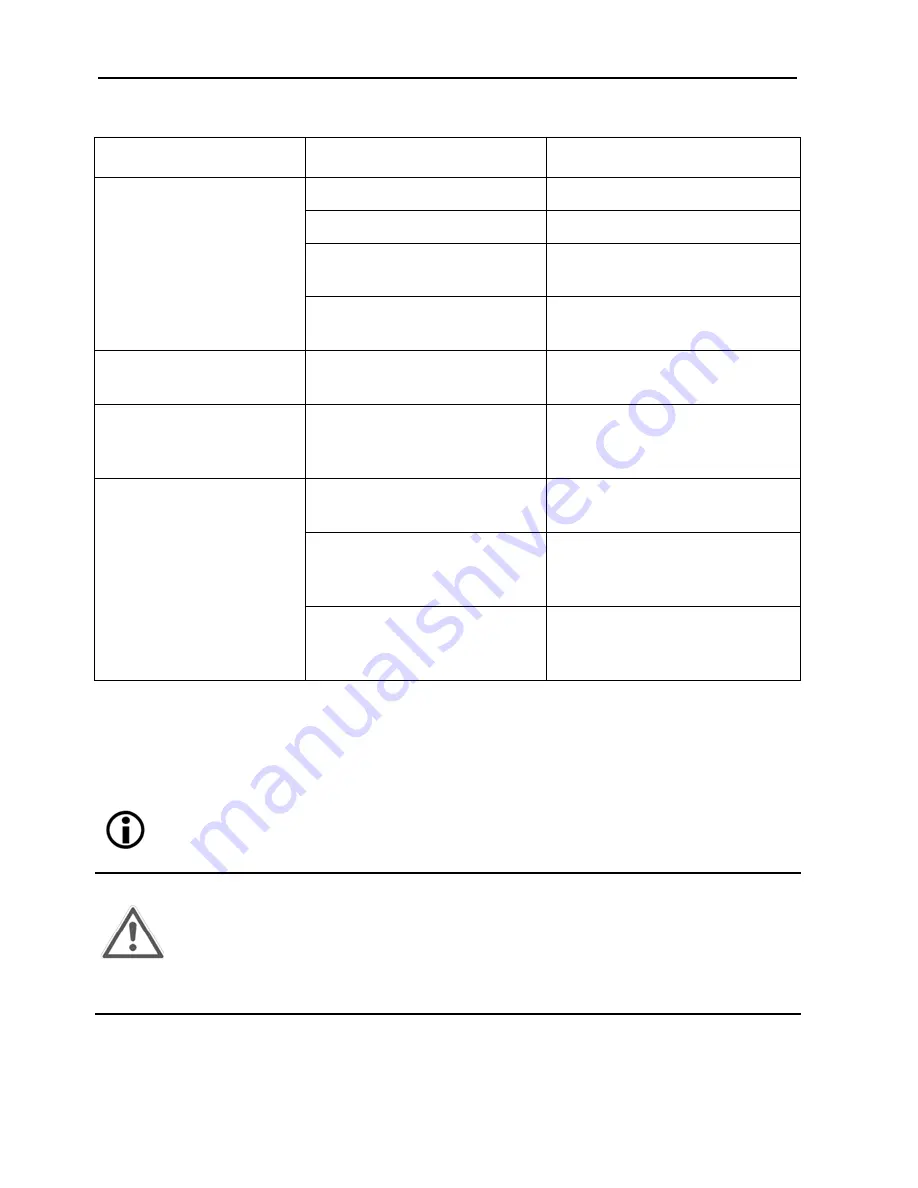
ZUWA Impeller Pumps
18
10. Troubleshooting
Fault Possible
cause
Remedy
Intake line is not leaktight
Seal connection or line
Impeller worn or damaged
Replace impeller
Suction line or foot valve is
blocked
Clean suction line or foot
valve
Pump does not take in
liquid
Pressure line closed or
blocked
Open fittings on the pressure
side or clean pressure line
Pump does not build up
pressure
Impeller or lateral discs are
worn
Replace impeller or lateral
discs
Liquid escapes from the
pump
Shaft gasket or O-ring is
missing or defective
Check whether part is in place
and insert or replace defective
component
Impeller blocked
Fill pump with the medium to
be pumped
Impeller clogged up or
macerated
Use an impeller appropriate to
the medium
Pump does not start
Motor defective
Have motor checked by
specialist personnel and have
repaired if necessary
11. Environmentally friendly disposal
>
Dispose of pumps according to locally applicable regulations.
Plastic parts can be contaminated by toxic pumped media, to the extent that
cleaning is no longer an adequate solution.
Warning
Danger of poisoning and environmental damage due to hazardous
pumped media
>
Collect escaping pumped media and dispose of according to the
locally applicable regulations.
>
Neutralise residues from the pumped media.