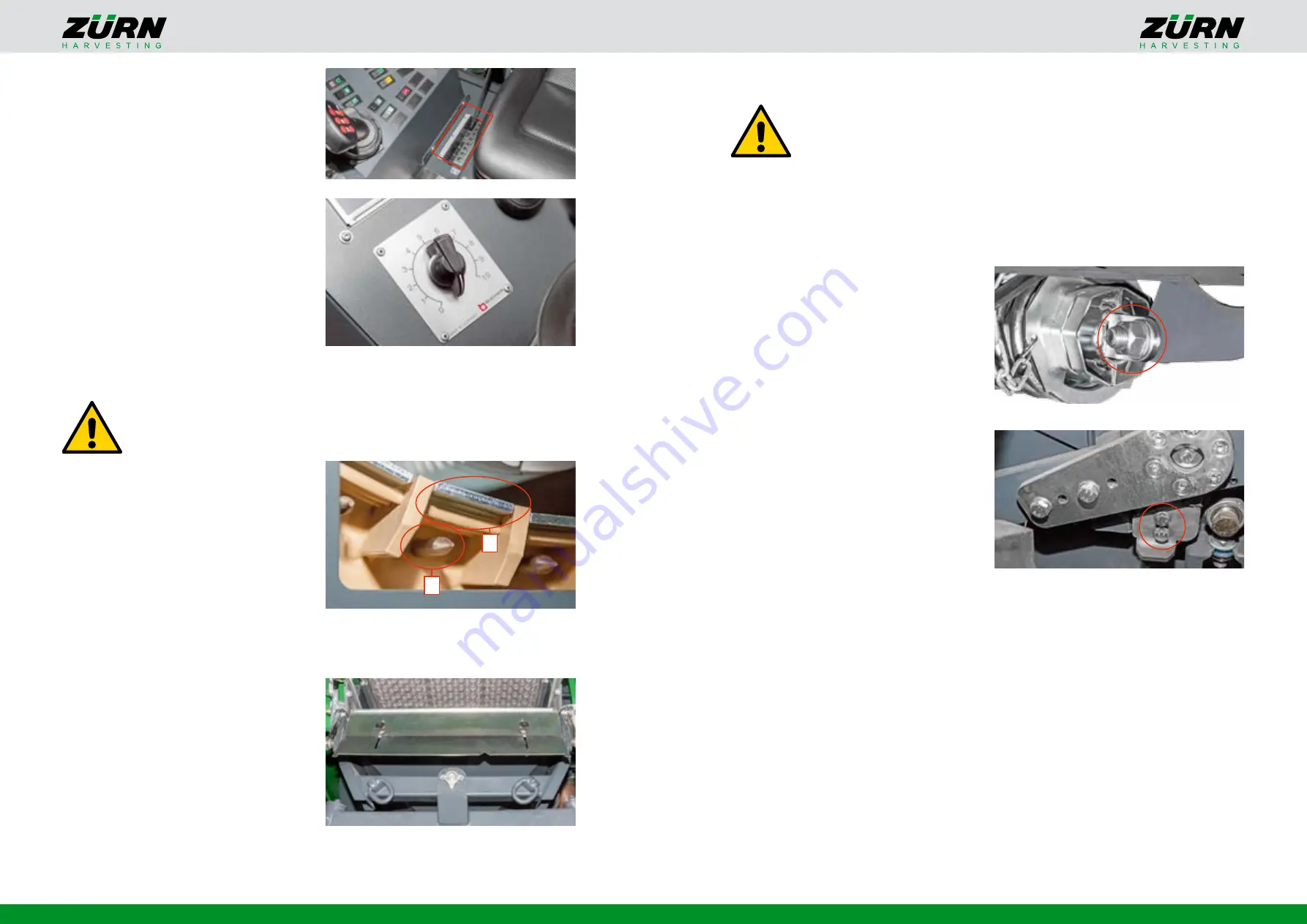
24/52 | Operation manual Z130-SE | 05/2016
25/52 | Operation manual Z130-SE | 05/2016
7.4. Setting concave spacing
The concave spacing is set using the lever
(Fig. 7.2) on the right or the left beside the
driver’s seat.
7.5. Setting wind strength
The wind strength is set with the aid of the
rotary switch on the dashboard (Fig. 7.3).
7.6. Adjustment treshing drum
speed (Variator)
The treshing drum speed is either adjustet
via the button (see 3.1 element 13, electrical)
or with the crank (manually) on the left side
of the combine.
7.7. Fitting de-awner bars
Fit de-awner bars evenly to prevent an imbalance on the threshing concave.
Up to four de-awner bars can be fitted.
1. Adjust concave spacing to the highest
setting.
2. Open right side cover on the threshing
concave
3. Fit required number of de-awner bars
4. Push locking pins from the right through
the holes in the threshing concave (Fig. 7.4
the holes (Fig. 7.4 element 2).
5. Check whether bars are firmly seated.
6. Close cover.
7.8. Adjusting dust plate
• Position the dust plate (Fig. 7.5) such that, at
the rear edge of the under sieve, the grains
do not wander forward on the under sieve.
• The opening between the dust plate and
upper sieve must be large enough that the
chaff on the under sieve can wander to the
rear.
Fig. 7.2
Fig. 7.3
Fig. 7.4
1
2
7.9. Adjusting header
7.9.1. Removing header
The combine has a quick-change system for removing and fitting the header.
1. Fully raise header.
2. Move reel all the way in and lower.
3. Switch off the engine remove the ignition
key.
4. Secure the table on blocks to prevent it
dropping.
5. Remove the header load relief springs
6. Remove blocks.
7. Fully lower header.
8. Uncouple hydraulic lines from header and
reel.
9. Disconnect Bowden cable for the reel
speed adjustment.
10. Slightly raise header using a crane or
similar at the reel mounting.
11. Disconnect lifting cylinder.
12. Unlock and remove pins for the header
bearings on the left and right by removing
the two hex-head bolts (Fig. 7.7).
13. Pull out header to the front.
The header is fitted in the reverse order of removal.
Fig. 7.6
Fig. 7.7
The header must be secured against dropping during all work on the header.
Fig. 7.5