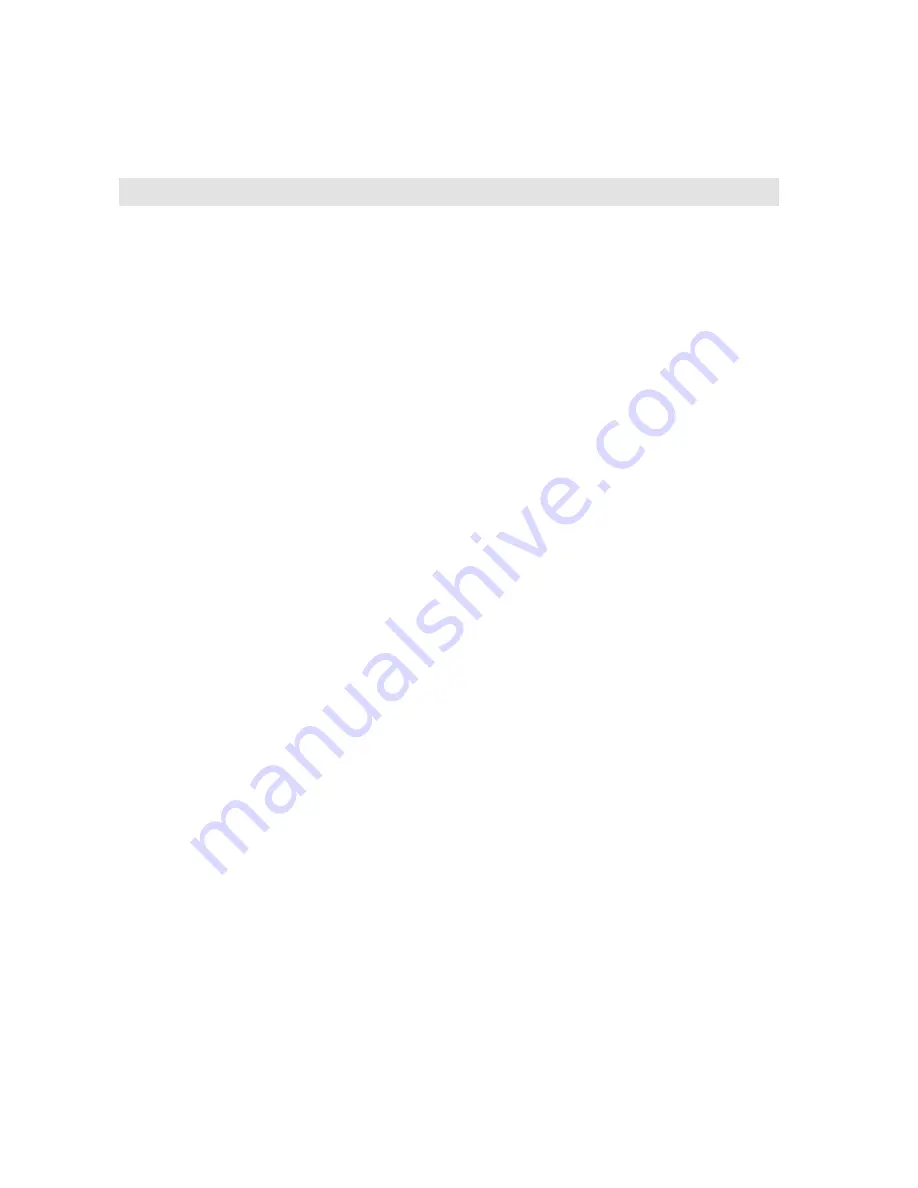
19
At the end of the adjusting procedure, subject the actuator to a functional check by means of the control circuit,
making sure particularly that the actuator starts correctly and is not “alive” after tripping of the respective microswitch.
If this is not the case, the actuator should be immediately disconnected from the mains to avoid a damage to the
electric motor and to find out the failure.
12. ATTENDANCE AND MAINTENANCE
Both electrical remote control and manual local control of the actuators at the site of instalation are provided. For
manual control, the handwheel of the actuator can be used, no change-over switch being required. This control
mode can be safely used by the operator even during operation of the electric motor.
Maintenance attention to the actuators involves only replacing some faulty parts and adjusting the electromagnetic
brake of the electric motor using this brake.
The brake should be readjusted after 0.5 x 10
5
switching operations, the air gap between the armature
and the electromagnet core being set to a value of 0.6 to 0.8 mm. Adjustment can be carried out by means of nuts
on the brake pull rod. The nut nearer to the electric motor is used for adjusting the required air gap, whilst the other
nut serves for locking. After adjustment, check the correct function of the brake and secure the nut in position by
a drop of varnish. Grease filling is stable for the whole service life of electric actuator which is at least 6 years.
If the actuator is capable of operating even after 6 years of operation old grease should be removed from
the power unit to pack it with fresh grease.
The connection screws between the valve and the actuator should be retightened crosswise after 6 months from
the date of commissioning of the actuator at the latest and then at least yearly.
Summary of Contents for MODACT MOK 1000
Page 2: ...ZPA Pe ky a s is certified company in accordance with ISO 90001 as amended...
Page 37: ...NOTE...
Page 38: ...NOTE...