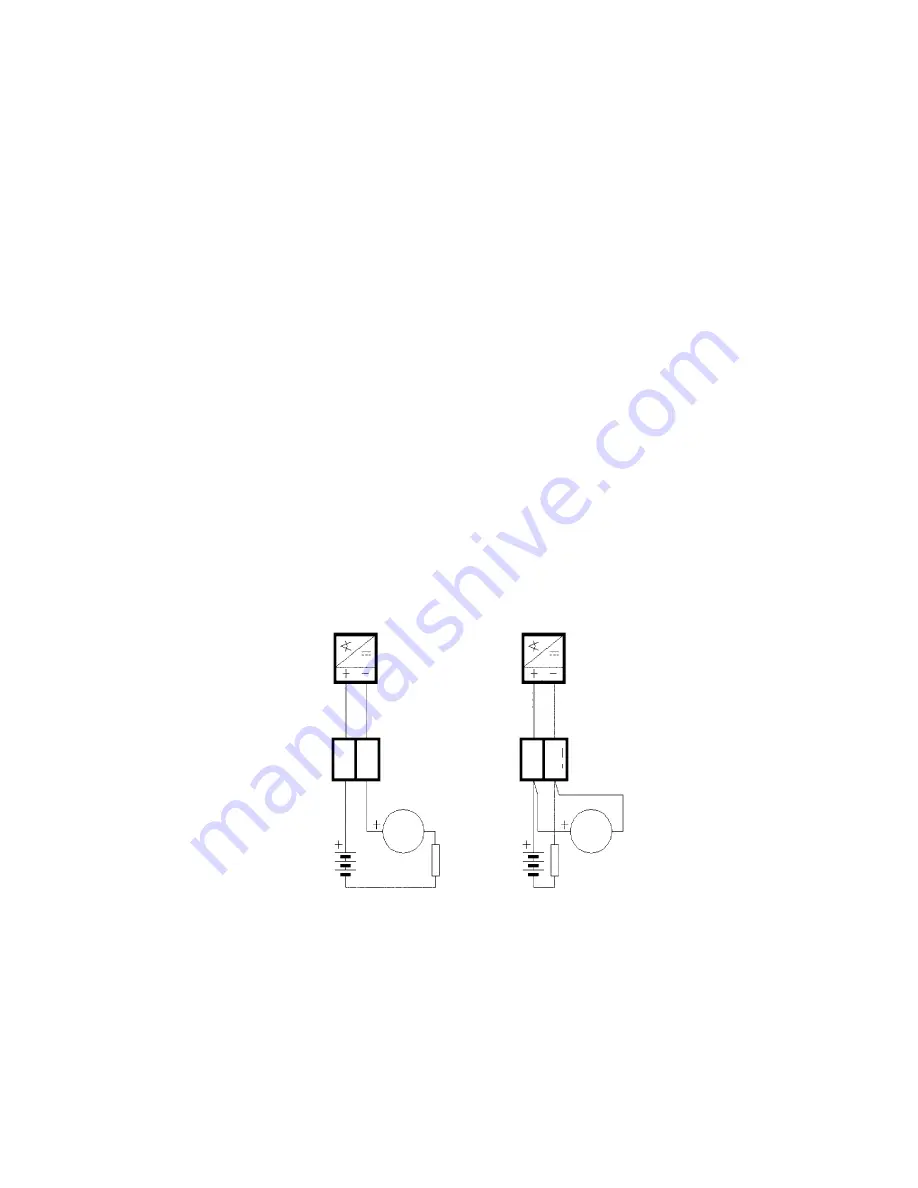
10
b) Position-limit switches
Position-limit switches PO, PZ switch off an electric actuator when the output shaft reaches the position for
which they are set. Signalling-limit switches SO, SZ signalise the position of electric actuator output shaft.
The setting of position-limit switches is carried out by positioning the output shaft into the position in
whichthe set switch should switch off. Then, loosen the micro-switch cam using the releasing screw.
Loosing will be done by turning the releasing screw counter-clockwise. Turn the releasing screw only until
the cam is released. By further turning of the releasing screw, you would tighten the cam again. Numbers of
relevant releasing screws are on a holder of position unit
(Fig. 1)
and they correspond to markings on a cam shaft.
When loosened, turn the cam in the opposite direction to the motion of an electric actuator output shaft while
setting the position “open” or “closed” until the micro-switch switches over. In this position lock the cam by tightening
the releasing screw
(clock-wise direction).
A signalling switch must be set so that it switches over sooner than a relevant position-limit switches or torque-limit
switches. When adjusting position-limit and signalling switches of electric actuators Type Nos. 52 326 and 52 327,
ensure that a gear segment of position and signalling unit drive in the extreme position “open” or “closed” doesn’t hit
the actuator case. A position unit of electric actuator Type No. 52 325 is not equipped with the locking of cams using
screws
(Fig. 2).
The cam’s position on the shaft is ensured only by friction which has to be overcome when adjusting
the cams. A design Type No. 52 325 has cams locked by friction and central milled nut with contra-nut which must be
loosened before adjusting and tightened properly again after adjusting.
c) Position transmitter
To adjust the potentiometer it is sufficient to set the actuator output shaft to any of the OPEN or CLOSED end
positions. In this way, the potentiometer is automatically preset. The automatic adjustment of the potentiometer is
usually provided already when the stop screws or the position-limit switches are adjusted.
Current position transmitter CPT 1Az – setting
Before starting setting the current transmitter it is necessary to set the end-limit positions
(torque or position
switches)
of the actuator and connect them into the tripping circuit of the electric motor. In case of an external source of
feeding voltage, verification must be carried out that it does not exceed the maximum value 30 V DC
(limit value when
CPT 1Az is still not damaged)
. Recommended value is 18 – 28 V DC.
Positive pole of the source is connected to the positive pole of the transmitter CPT 1Az; a milli-ammeter of precision
at least 0.5 % connected into the circuit. The current loop must be earthed in one point. The figure does not show
the earthing that can be made at any point of the circuit.
1. Shift the output shaft into the position Closed. During closing, the current signal value should decrease. If it increases
release the transmitter body and, by turning of about 180°, shift to the descending part of the outputcharacteristics. Set
4 mA by fine turning. Tighten the shim plates to secure the transmitter against spontaneousturning.
2. Shift the output shaft to the position Open and set 20 mA using a potentiometer on the transmitter body. The
potentiometer has a range of 12 revolutions and it has no stops so that it cannot be damaged by furtherturning.
3. Once again verify the current value in the position Closed. If it has changed too much repeat the points 1. and 2.
If the required corrections are large this procedure should be repeated several times. After the setting, securethe
transmitter against turning and drip the screws with varnish.
4. Use a voltmeter to check the voltage on the CPT 1Az terminals. In order to keep linearity of the output signal
the voltage must not drop below 9 V, not even with off-take 20 mA. If this condition is not met it is necessary to increase
the feeding voltage
(within the range of recommend values)
or to decrease total resistance of the current loop R.
CPT 1Az
U
U
R
mA
V
R
red
51
51
52
52
red
white
white
CPT 1Az
Summary of Contents for MODACT MOK 1000
Page 2: ...ZPA Pe ky a s is certified company in accordance with ISO 90001 as amended...
Page 37: ...NOTE...
Page 38: ...NOTE...