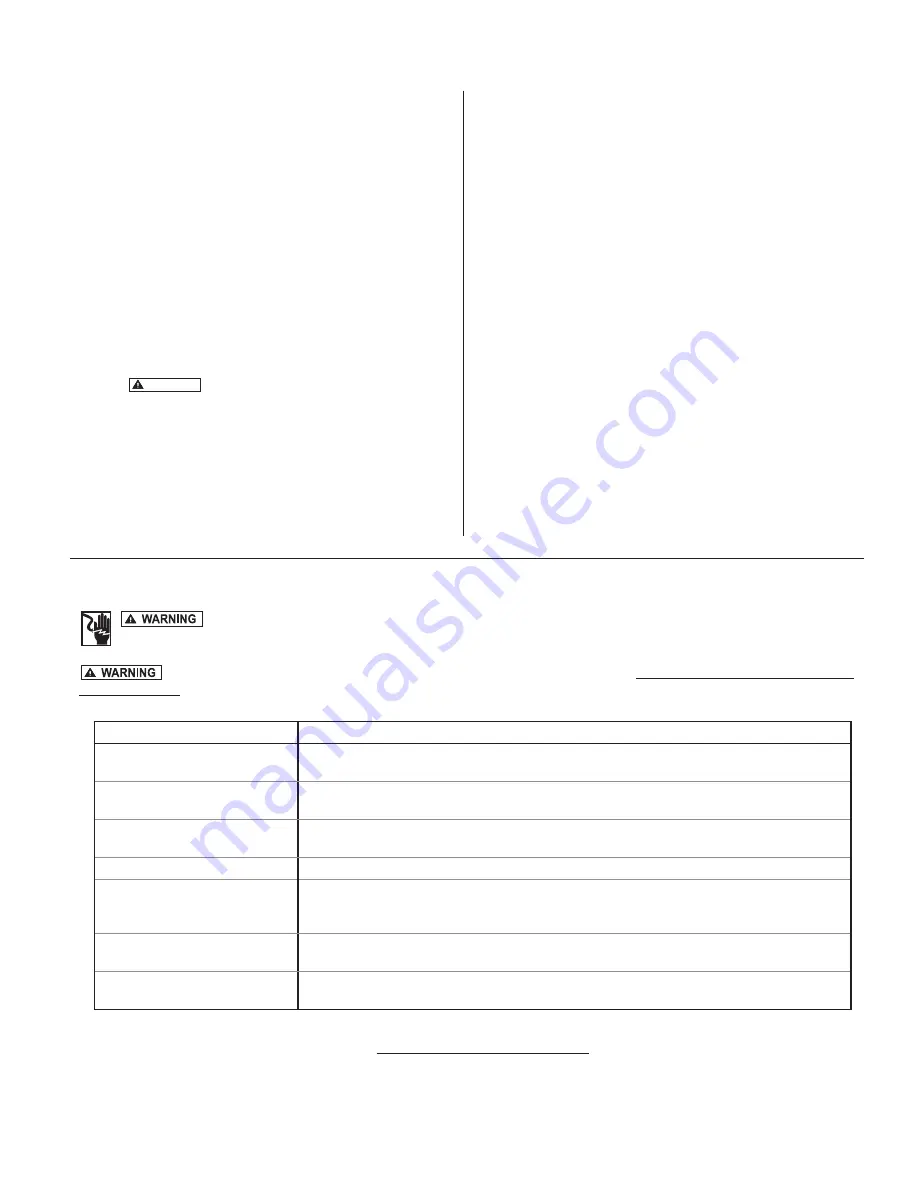
7
© Copyright 2014 Zoeller Co. All rights reserved.
ELECTRICAL PRECAUTIONS-
Before servicing a pump, always shut off the main power breaker and then unplug the pump - making
sure you are wearing insulated protective sole shoes and not standing in water. Under flooded conditions, contact your local electric company or a
qualified licensed electrician for disconnecting electrical service prior to pump removal.
Submersible pumps contain oils which becomes pressurized and hot under operating conditions -
allow 2½ hours after disconnecting before
attempting service.
If the above checklist does not uncover the problem, consult the factory - Do not attempt to service or otherwise disassemble pump. Service must be
performed by Zoeller Authorized Service Stations. Go to www.zoellerpumps.com/service stations to find the Authorized Service Station in your area.
SERVICE CHECKLIST
TROUBLESHOOTING INFORMATION
1. Charging and charged LED’s alternate frequently.
(a) This is normal.
2. DC Pump won’t run.
(a) Check 15 amp fuse in line from pump to switch (see fig. 4). If fuse
is blown, replace with 15 amp Littelfuse type 3AG, series 311.
(b) Check for proper connections.
(c) Check all wire terminal points. Clean if required.
(d) Check for low battery. Service battery if required.
3. Pump runs but pumps very little or no water.
(a) Check for low battery. Battery will recharge if Red power “on”
light indicates power has been restored and the float switch is
in the off position.
(b) If immediate usage is required, remove and replace dead
battery with a full recharged battery.
(c) Due to varying conditions the pump may continue to run on a
low battery without sufficient power to remove water. Pump will
not stop running until battery is completely discharged.
(d)
CAUTION
Weak batteries can be recharged but may
not store sufficient energy for full service. A weak recharged
battery can only be detected by reduced pumping time or by
checking each cell with a hydrometer. If your emergency pump
system is used frequently the battery should be checked by a
qualified battery dealer.
4. Pump cycles too frequently.
(a) Check positions of rubber stops on float rod.
(b) Adjust upper rubber float stop as required. Recommended for
standard installation.
5. Float switch in “on” position. Pump won’t run.
(a) Remove pump. Check for obstruction in pump preventing
impeller from rotating.
6. Pump runs, but pumps water intermittently.
(a) Pump is air locking. Check flow of water incoming to sump. If
water is entering the sump at a high velocity creating a turbulent
condition, a mixture of air and water may cause a complete
or partial air lock and reduce or stop the flow of water in the
discharge pipe.
(b) Baffle the incoming stream of water to reduce turbulence.
Diverting water stream against wall of basin usually corrects an
air lock problem.
7. Water level stays high. DC Pump continues to run.
(a) Battery is low.
(b) If power has been restored and water in sump remains high
check primary pump. Service if required.
(c) After several hours the battery will be restored to full charge.
8. Alarm sounds during battery recharge cycle.
(a) Push alarm reset (max. 3 times). If condition persists, replace
battery.
(b) To silence alarm if alarm will not reset, unplug the charger from
115V wall outlet, then disconnect the black lead from charger on
negative (-) battery post. Check battery. Replace if necessary.
Reconnect and refer to Installation (step 7).
CONDITION
COMMON CAUSES
A. Pump will not start or run.
Check fuse, low voltage, overload open, open or incorrect wiring, open switch, impeller or seal bound mechanically, motor
or wiring shorted. Float assembly held down. Switch, damaged or out of adjustment.
B. Motor overheats and trips
overload or blows fuse.
Incorrect voltage, negative head (discharge open lower than normal) impeller or seal bound mechanically, motor shorted.
C. Pump starts and stops too often. Float switch tether length too short, check valve stuck open, or none installed in long distance line, overload open, bidding,
sump pit too small.
D. Pump will not shut off.
Debris under float assembly, float bound by basin sides or other, switch, damaged or out of adjustment.
E. Pump operates but delivers little
or no water.
Check inlet, strainer housing, discharge pipe, and vent holes for obstructions. Discharge head exceeds pump capacity.
Low or incorrect voltage. Incoming water containing air or causing air to enter pumping chamber. Incorrect motor rotation.
(3 phase pumps only)
F. Drop in head and/or capacity
after a period of use.
Increased pipe friction, clogged line or check valve. Abrasive material and adverse chemicals could possibly deteriorate
impeller and pump housing. Check line. Remove base and inspect.
G.
If tank or fittings leak.
Carefully tighten pipe joints (use pipe dope) and screws. Check gasket location, tighten lid evenly. Do not over tighten
fittings or screws.