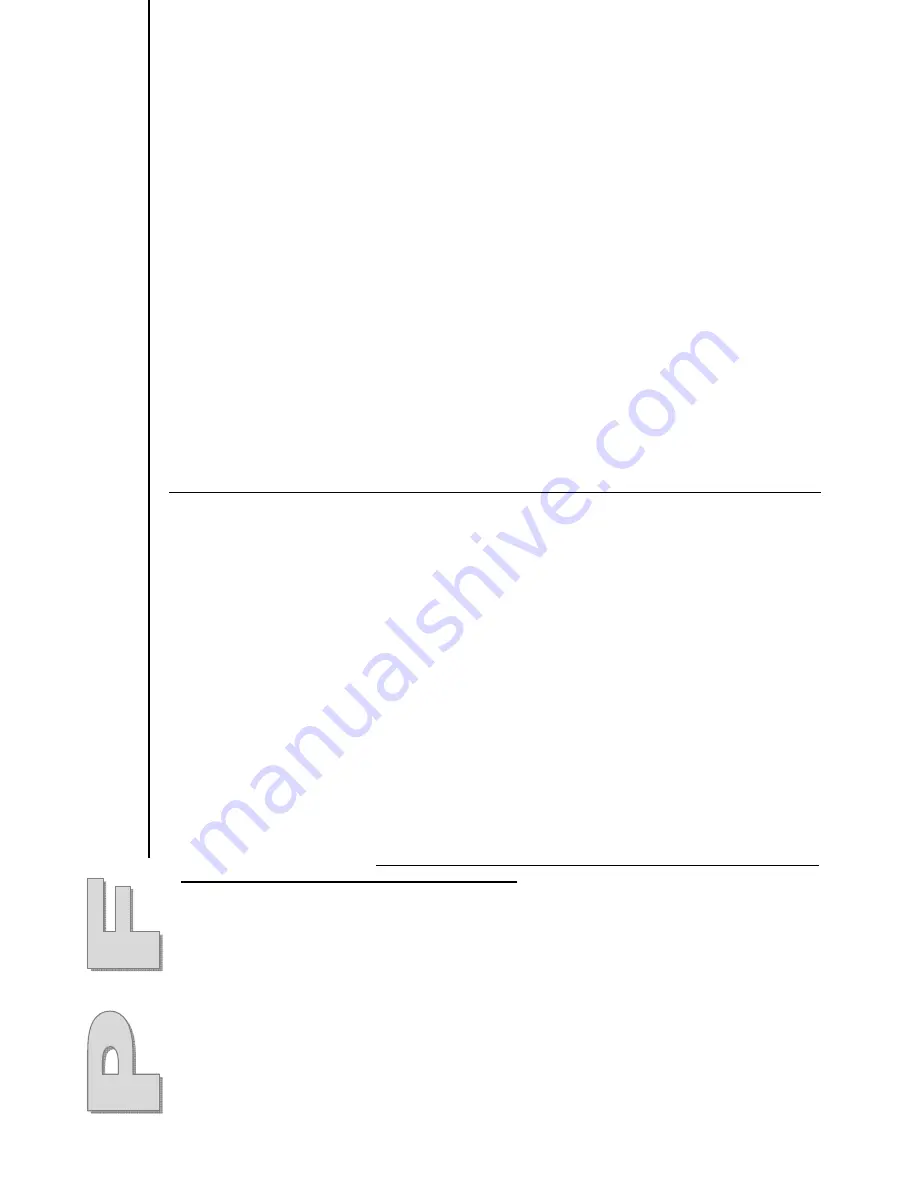
15
the person responsible for final acceptance of the unit must carry out a visual inspection to detect
any damage the unit may have suffered during transport: refrigeration circuit, electrical enclosure,
frame and casing.
the unit may not be installed close to:
- a heat source,
- combustible materials,
- the air duct inlet of an adjacent building.
for certain appliances, it is essential to fit protection grids if the unit is installed in an area which is
unprotected and easily accessible.
the appliance may only be installed, commissioned, serviced and repaired by properly qualified
persons in accordance with directives, laws, valid regulations and acceptable professional practice.
during installation, repair and maintenance work, it is strictly prohibited to step on pipes and hoses
as these could break and the escaping refrigerant could cause serious scalding.
when servicing the appliance, the composition and state of heat carrying fluid must be checked, as
well as the absence of any refrigerant.
during the annual unit sealing test in accordance with valid legislation, the high and low pressure
switches must be checked to ensure they are securely fastened to the refrigeration circuit and that
they shut-off the electrical circuit when tripped.
during maintenance work, ensure there are no traces of corrosion or oil around refrigeration
components.
before beginning work on the refrigeration circuit, isolate the appliance and wait several minutes
before removing the temperature or pressure sensors. Certain elements such as the compressor and
associated piping may attain temperatures in excess of 100°C and high pressures with the
consequent risk of severe scalding.
7.2 Repair
all work on the refrigeration circuit must be carried out with total respect of valid safety regulations
and acceptable professional practice: recuperation of refrigerant, nitrogen brazing, etc…
all brazing work must be carried out by a qualified brazer/welder,
in the case of units filled with R410A, refer to the specific indications in the installation instructions.
this unit contains pressurized components, some of which may be manufactured by ZPCE, this is
the case of piping elements. Only use the original spare parts indicated in the spare parts list to
replace a defective refrigeration component
replacement pipes must always be made of copper in compliance with standard NF EN 12735-1.
leak detection, pressure test:
- never use oxygen or dry air, risk of fire or explosion,
- use dry nitrogen or the mixture of nitrogen and refrigerant indicated on the name plate,
- the test pressure for both the high and low pressure circuits must not exceed 42 bar.
the high pressure circuit pipes are made of copper and have a diameter equal to or greater than
1’’5/8. A certificate as indicated in §2.1 in compliance with standard NF EN 10204 will be requested
from the supplier and filed in the installation technical documentation.
the use of non-original spare parts, modifications to the refrigeration circuit, replacement of the
refrigerant with a refrigerant type other than that indicated on the name plate, use of the appliance
under conditions outside the application limits indicated in the associated documentation will result in
a cancellation of the EC label and PED conformity and the person who carried out these modifications
will be sole responsible for the consequences.
the technical data relative to the safety requirements of the various applicable directives must be
indicated on the name plate.
This data must be recorded in the unit installation instructions
which are included in the installation technical file
:
-
model – code – serial number,
-
maximum and minimum OT,
-
OP,
-
year of manufacture,
-
EC label,
-
manufacturer’s address,
-
refrigerant and weight,
-
electrical parameters,
-
thermo-dynamic and acoustic performance
As part of our continuous improvement policy our products may be subject to change without
notice.
Version 12/2010