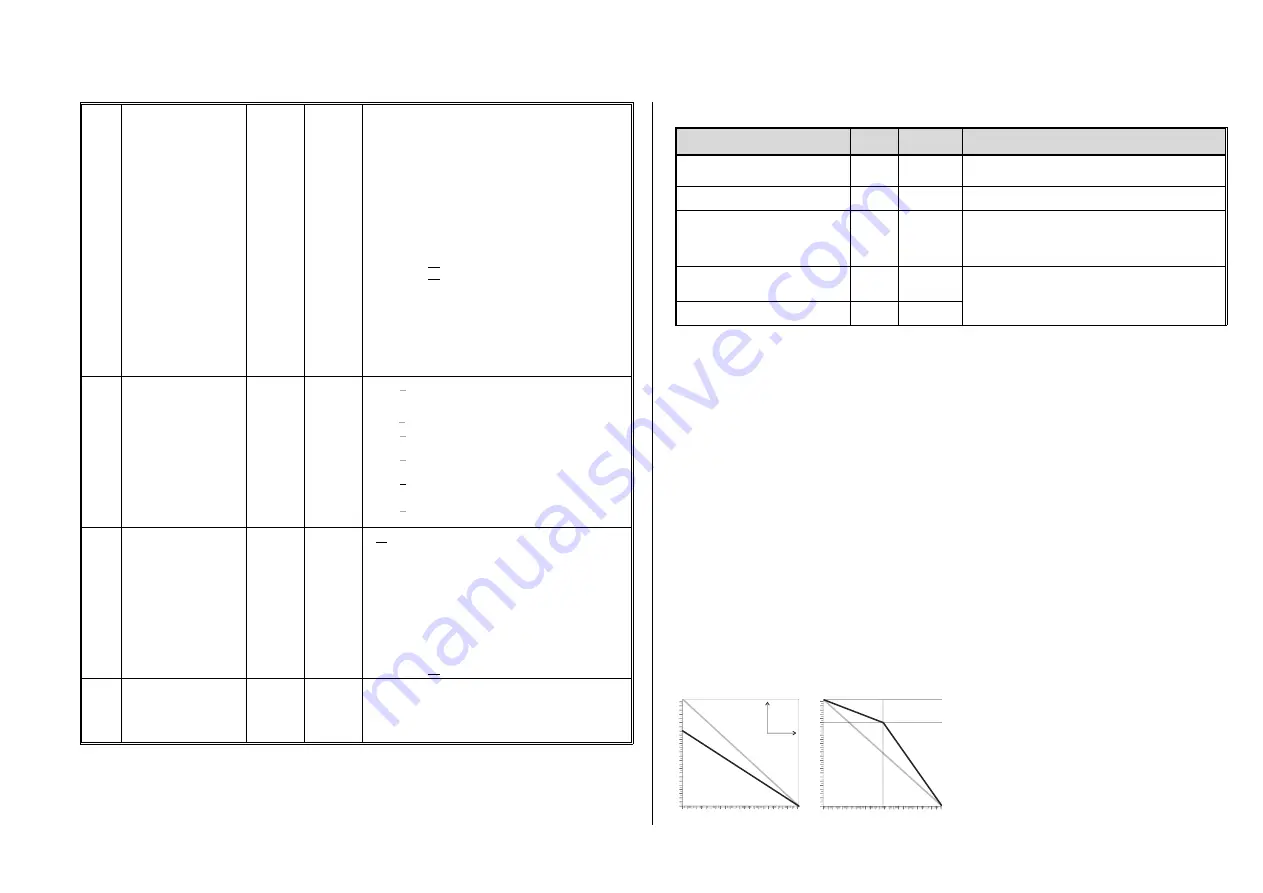
Non-Sound Decoder MX600 - MX638 and Sound Decoder MX640 - MX659 Page 19
0
10
20
30
40
50
60
70
80
90
100
110
120
130
140
150
160
170
180
190
200
210
220
230
240
250
0 20 40 60 80 100 150 200 252
D
efa
ult
co
m
pe
ns
atio
n c
urv
e
CV
#
58
=
2
55
, C
V
#
10
u
nd
#
11
3 =
0
Fu
ll c
om
pe
ns
atio
n a
t lo
w
sp
ee
d,
dro
pp
i ng
o
ff to
0
a
t fu
ll s
pe
ed
.
C
o
m
p
.
in
fl
ue
n
ce
Int. s peed s tep
Alte
red
co
mp
en
sati
o n c
u rv
e
C V
#5
8 =
18
0 , C
V #
10 u
nd #
113
=
0
Re
duc
e d
co
mp
ens
a tio
n o
ver
the
w
hole
sp
ee
d ra
nge
.
0
10
20
30
40
50
60
70
80
90
100
110
120
130
140
150
160
170
180
190
200
210
220
230
240
250
0 20 40 60 80 100 150 200
252
Def
a ult
c o
mp
en
satio
n cu
rve
Alter
ed co
mpen
satio
n cu
rve
CV #
10 =
126
, CV
#113
= 2
00,
Incre
ase
d co
mpen
satio
n
in
the
medi
um
s
peed
ran
ge.
#9
rate
.
01 - 99
High
frequency
with
modified
sampling
rate.
255-176
Low
frequency
rate
.
tens digit for sampling rate and
ones digit for sampling time.
Tens digit 1 - 4: Lower sampling rate than default
(less noise!)
Tens digit 6 - 9: Higher sampling rate than default
(to combat juddering!)
Ones digit 1
– 4: Shorter EMF sampling time
(good for coreless motors, less noise, more power)
Ones digit 6 - 9: Longer EMF sampling time
(may be needed for round motors or similar).
Typical test values against jerky driving:
CV #9 = 55 (default)
83, 85, 87, ...
CV #9 = 55 (default)
44, 33, 22,
…
= 255 - 176: Low frequency (for old motors only!)
–
PWM according to formula (131+ mantissa*4) *2exp. Bit 0-4 is
“mantissa”; Bit 5-7 is “exp”. Motor frequency is the reciprocal of
the PWM.
Examples:
#9 = 255: frequency at 30 Hz,
#9 = 208: frequency at 80 Hz,
#9 = 192: frequency at 120 Hz.
#112
Special ZIMO
configuration bits
0 - 255
4 =
0000 0100
Bit 1 = 0: Normal acknowledgement.
= 1: High frequency acknowledgement
Bit 2 = 0: Loco number recognition OFF
= 1: ZIMO loco number recognition ON
Bit 3 = 0:
12-Function Mode
= 1:
8-Function Mode
Bit 4 = 0: Pulse chain recognition OFF
= 1: Pulse chain recognition (for old LGB)
Bit 5 = 0: 20 kHz motor control frequency
= 1: 40 kHz motor control frequency
Bit 6 = 0: normal (also see CV #29)
= 1: „Märklin brake mode
#56
P and I value
For
BEMF motor regulation
55
medium
PID
setting
01 - 199
modified
settings
55
= 55: Default setting using medium PID parameters.
= 0 - 99:
Modified settings for “normal” DC motors.
= 100 - 199: Modified settings for coreless motors
(Faulhaber, Maxxon etc.)
Tens digit 1 - 4: Lower proportional value than default
Tens digit 6 - 9: Higher proportional value than default
Ones digit 1 - 4: Lower integral than default
Ones digit 6 - 9: Higher integral than default
Typical test values against jerky driving:
CV #56 = 55 (default)
33, 77, 73, 71, ..
#147
EMF
– Extended
sampling time
0 - 255
0
Useful initial test value: 20.
For Fleischmann motors
Values too small cause engine to stutter, values too big
worsens the regulation at low speeds.
Fine-tuning suggestions
(if default settings are not satisfactory):
Vehicle, Type of Motor
CV #9
CV #56
Remarks
“Normal” modern Roco engine
= 95
= 33
Means high sampling rate at low load; reduced rate at
higher load to prevent loss of power.
Typical N-scale engine
= 95
= 55
Fleischmann “round motor”
= 89
= 91
Also recommended: CV #2 = 12,
CV #147 = 60
From SW version 31:
CV #145 = 2
(Attention: often helpful
– remove suppressor compo-
nents.
Small coreless (Faulhaber, Maxxon
or similar)
= 51
= 133
The stronger the motor, the weaker the regulation is
set to avoid overshoots, the integral component never-
theless provides for full load regulation.
Large coreless (O gauge or larger)
= 11
= 111
Tips on how to find the optimal CV #56 settings:
Start with an initial setting of CV #56 =
11
; set the engine at low speed while holding it back with one
hand. The motor regulation should compensate for the higher load within half a second. If it takes
longer than that, increase the ones digit gradually: CV #56 = 1
2
, 1
3
, 1
4
...
With the locomotive still running at a low speed, increase the tens digit in CV #56. For example: (if the
test above resulted in CV #56 = 1
3
) start increasing the tens digit CV #56 =
2
3,
3
3 ,
4
3…as soon as
juddering is detected, revert back to the previous digit
this would be the final setting.
Load Compensation, Compensation Curv
e and Experimental CV’s
The goal of load compensation, at least in theory, is to keep the speed constant in all circumstances
(only limited by available power). In reality though, a certain reduction in compensation is quite often
preferred.
100% load compensation is useful within the low speed range to successfully prevent engine stalls or
run-away under light load. Load compensation should be reduced as speed increases, so that at full
speed the motor actually receives full power. Also, a slight grade-dependent speed change is often
considered more prototypical.
Locomotives operated in consists should never run at 100% load compensation, in any part of the
speed range, because it causes the locomotives to fight each other and could even lead to derail-
ments.
The overall intensity of load compensation can be
defined
with
CV # 58
from no compensation
(value 0) to full compensation (value 255). Useful
values range from 100 to 200.
For a more precise or more complete load com-
pensation over the full speed range use CV #10
and CV #113 together with CV #58 to define a 3-
point curve.