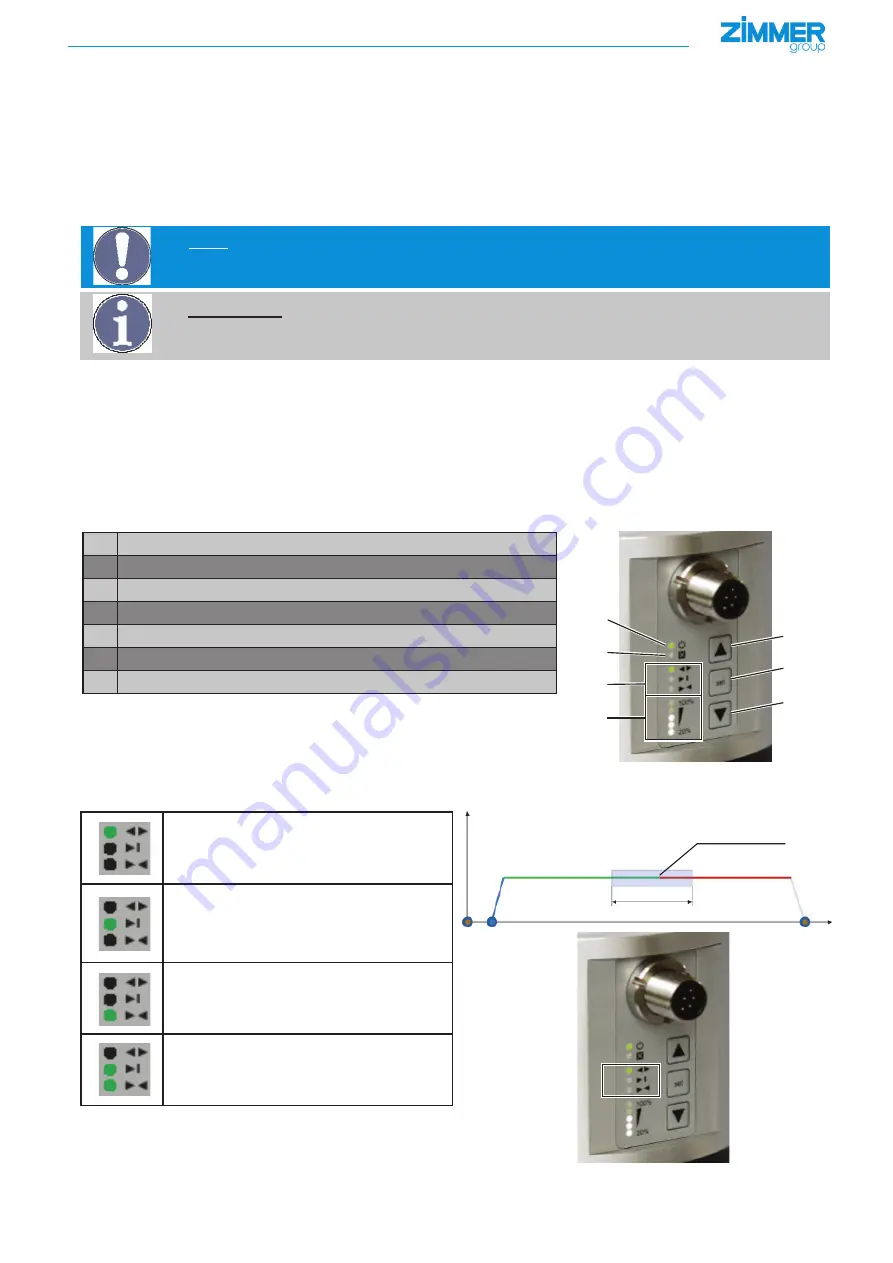
Zimmer GmbH
●
Im Salmenkopf 5
●
77866 Rheinau, Germany
●
Phone: +49 7844 9138-0
●
Fax: +49 7844 9138-80
●
www.zimmer-group.de
DDOC00198/t
EN/2015-10-07
7
INSTALLATION AND OPERATING INSTRUCTIONS:
ELECTRIC GRIPPER GEP/GED5000 SERIES
7.4
End positions
INFORMATION:
Important for handling the product.
The setting of the intermediate position (Section 6.3) is lost when teaching-in the end positions!
After teaching-in the end positions, the intermediate position must be taught-in once again!
End position confirmation occurs via pin 2 (work position)* and pin 5 (base position)*.
The statuses are visualized on the gripper via the LED display.
The gripper's end position sensing is preset by the plant.
If necessary, end positions can be re-set via an automatic traversing routine*.
► To do so, a signal (+24 V DC) must be applied to the pin 7 output (teach/adjust)* for at least 15 seconds.
A requirement is that the DIR signal is simultaneously set to "0".
► After approximately 3 seconds, the traversing routine* begins and is completed after 5 gripping cycles.
*) See "Glossary" section for definitions
NOTE:
Non-compliance may result in damage to the system
If the signal (+24 V DC) is interrupted before the end of the traversing routine, the procedure must be repeated
because the end positions are not correctly determined.
7.5
Minimum travel path
The gripper requires a minimum travel path of
> 1,25 mm
per jaw before it is permitted to reach a workpiece.
Failure to do so means the gripper cannot establish the desired gripping force and displays an error.
The minimum travel path applies to both movement directions and is independent of the gripper's starting position.
8. Operation
8.1
Control panel
The control panel of the gripper continuously displays the current status of the device and provides the option to modify various set
-
tings of the gripper using multiple menus
1
2
3
4
5
6
7
1
Power LED, power supply
2
Error LED, error display
3
Position display, menu display
4
Parameter display, binary error code display
5
Plus key, increase parameter value
6
Set button
7
Minus key, decrease parameter value
8.2
Position display
The positions of the gripper are displayed on the operator panel via three LEDs.
Gripper in base position
NC = gripper jaws open
NO = gripper jaws closed
Gripper is on a teached-in workpiece item
(teach-in position/teach position)
Gripper is at the work position
(working position)
If the gripper has been taught-in at an end posi-
tion, two LEDs are switched on simultaneously.
(Ex.: End position, work position and teach
position
Base position
Work position
Teach position