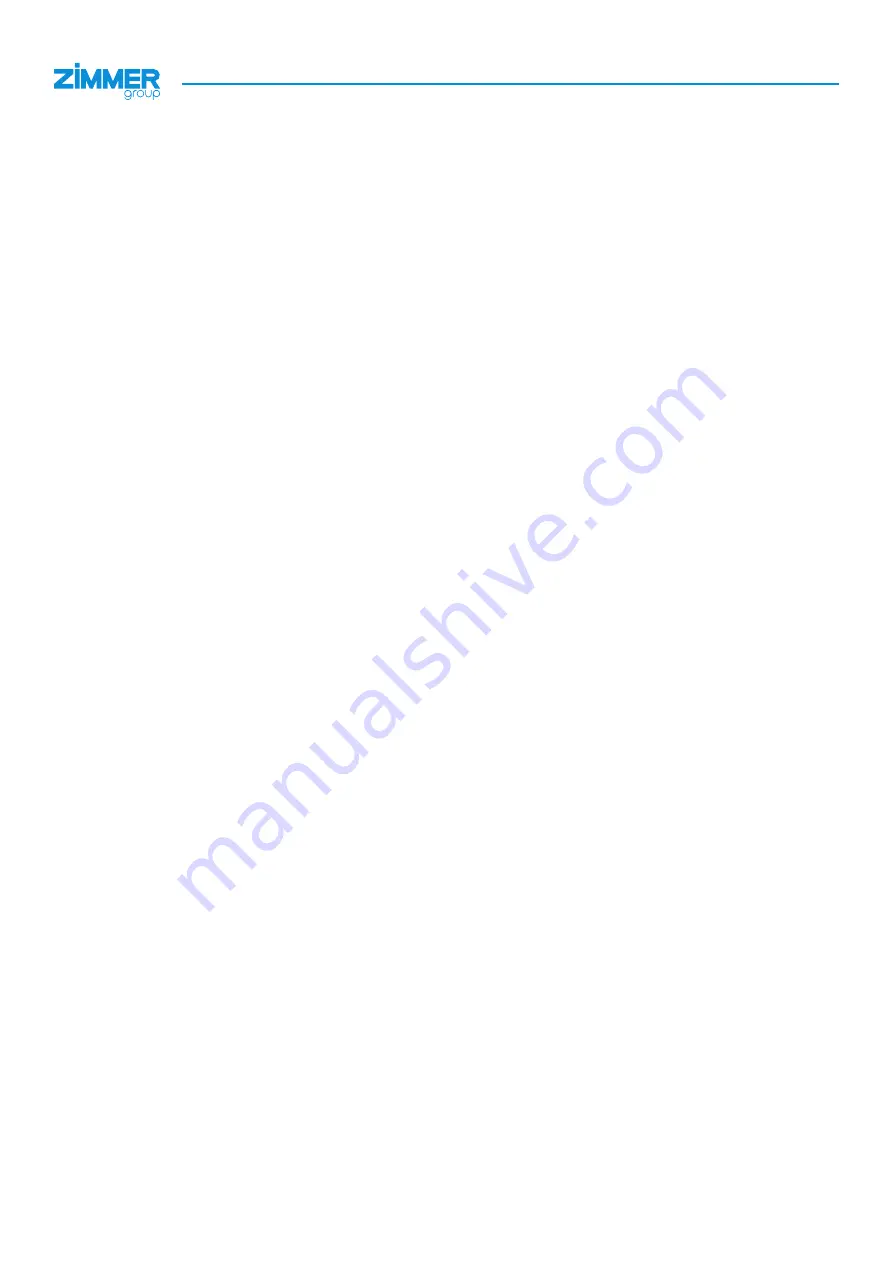
48
11.5 Functions of the function block
Depending on the switching of the function block, the following functions are carried out.
11.5.1
b_Power
If the variable is set to
true
, the drive control unit receives drive enable (AF) and the drive is permitted to move.
If the variable is set to
false
, the drive is shut down.
11.5.2 b_Automatic
Limits the automatic approach to the predefined positions.
If the variable is not set and
b_Power
is
true
, the product can be jogged continuously in the respective direction using
b_JogPlus
and
b_JogMinus
.
The operation mode in the drive control unit is not toggled for this. This bit only affects the logic of the instance
fb_
GEH8660
.
11.5.3 b_MoveToWorkPos
A positive edge at this input causes the product to move to the work position
st_Parameter.f_WorkPos
.
The prerequisite for this is that
b_Power
,
b_Automatic
and
b_Enabled
(AF) are set to
true
and the function block is not
currently processing any other commands.
11.5.4 b_MoveToWorkPos_2
A positive edge at this input causes the product to move to the alternative work position
st_Parameter.f_WorkPos_2
.
The prerequisite for this is that
b_Power
,
b_Automatic
and
b_Enabled
(AF) are set to
true
and the function block is not
currently processing any other commands.
11.5.5 b_MoveToBasePos
A positive edge at this input causes the product to move to the home position
st_Parameter.f_BasePos
.
The prerequisite for this is that
b_Power
,
b_Automatic
and
b_Enabled
(AF) are set to
true
and the function block is not
currently processing any other commands.
11.5.6 b_SetReferencePos
A positive edge at this input causes the product to move to the reference position
st_Parameter.f_HomePos
.
The prerequisite for this is that
b_Power
,
b_Automatic
and
b_Enabled
(AF) are set to
true
and the function block is not
currently processing any other commands.
11.5.7 b_Halt
If this signal is set to
true
while the drive control unit is in drive enable (AF), the drive is stopped immediately (AH).
If the variable is set to
false
, the drive control unit again has drive enable (AF).
11.5.8 b_Fehler_Reset
Acknowledge all pending errors. If the error persists, it cannot be acknowledged.
Zimmer GmbH • Im Salmenkopf 5 •
77866 Rheinau, Germany •
+49 7844 9138 0 • www.zimmer-group.com
INSTALLATION AND OPERATING INSTRUCTIONS:
GEH8000
DDOC00262 / e
EN / 2023-03-06