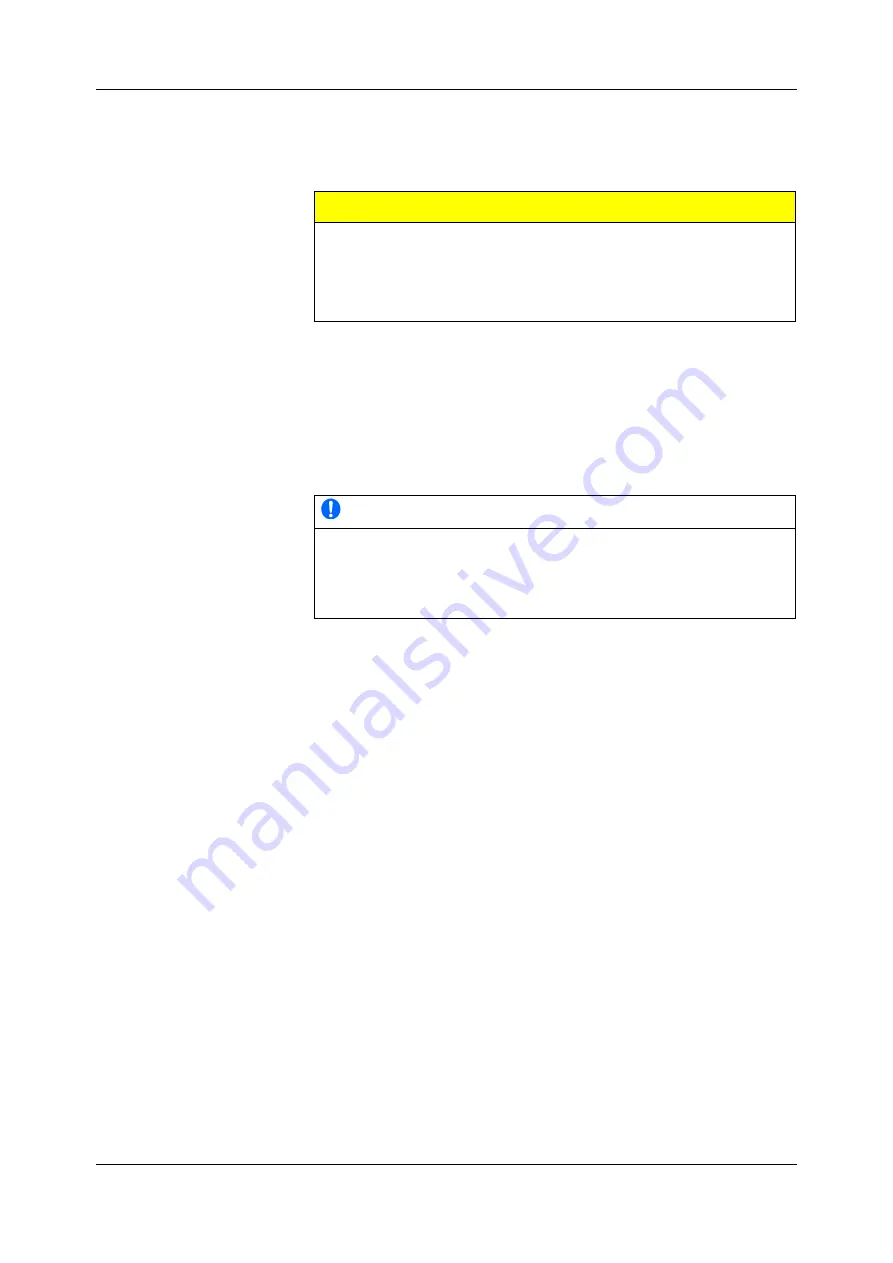
ZIMM Screw Jack
8 Decommissioning
and recommissioning
2015-01
Version 1.2
33
8
Decommissioning and recommissioning
CAUTION
Corrosion!
Damage to the screw jack after a long period out of use.
Oil bright metal surfaces and grease the spindle.
After the ZIMM Screw Jack has been out of use for a long period:
1. Clean the spindle and
2. Regrease the spindle, see section "7.2 Lubrication", page 25.
9
Repair and replacement
NOTE
The warranty becomes void if the ZIMM Screw Jack is dismantled.
Allow the ZIMM Screw Jack to be dismantled only by ZIMM or by
personnel authorised by ZIMM.
Contact ZIMM Maschinenelemente GmbH + Co KG.
10
Disposal
The ZIMM Screw Jack satisfies the current standards and regulations
for disposal of end of life equipment. It contains no poisonous
substances which demand the taking of special precautions.
During disposal, ensure:
– Compliance with regional laws and regulations for waste
disposal
– Correct disposal and recycling should be entrusted to a
professional disposal company
The following materials will require disposal:
•
Lubricants (grease or oil in the gearbox, lubricating grease on the
spindle)
•
Steel parts (coated with environmentally-friendly paints or coatings)
•
Anodised aluminium (parts)
•
Bronze/copper (bevel gear, nuts or windings on the motor)
•
Plastic parts (seals etc.)
Decommissioning
Recommissioning