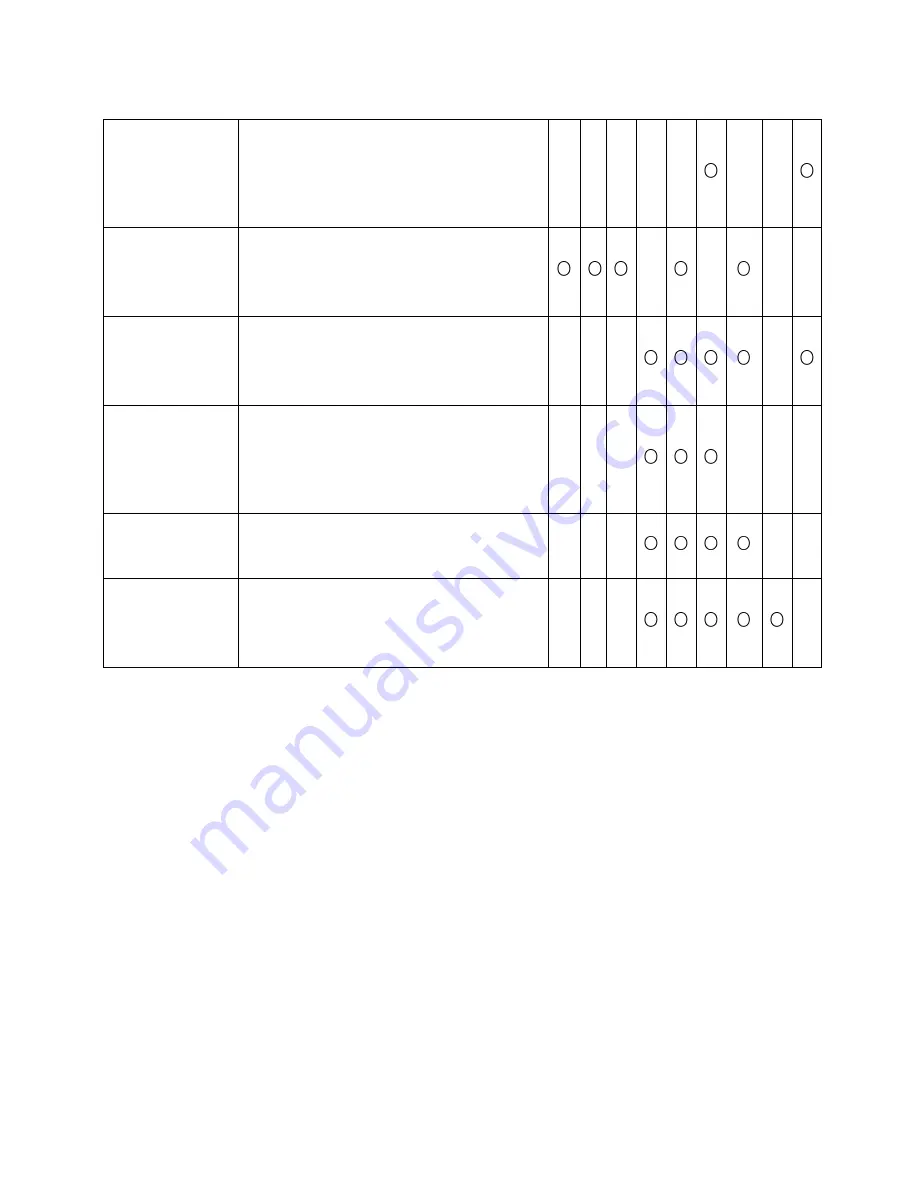
31
Body of weld gun
1. Loose connection of conductive tip, nozzle
and nozzle contactor
2. Contactor of weld gun body is not plunged
in or tightened well
Power supply
cable of weld gun
as well as cable of
switch control
1. Break off (bending fatigue)
2. Damaged by weighted drop
Surface Condition
of Parent material
and length that
wire stretches out
1. Oil, dirty, rust and paint residues
2. Too long length of wire stretched out
Output Cable
1. Cross-section of cable that connects to
parent material is not enough
2. Loose connection of
(
+
)(
, -
)
output cable
3. Bad electric conductivity of parent material
Lengthened
Cable
1. Cross-section of cable is not enough
2. It is rolled up or folded
Work Condition
for Welding
Welding current, voltage, angle of weld
gun, welding rate and wire length
stretched out should be confirmed once
again