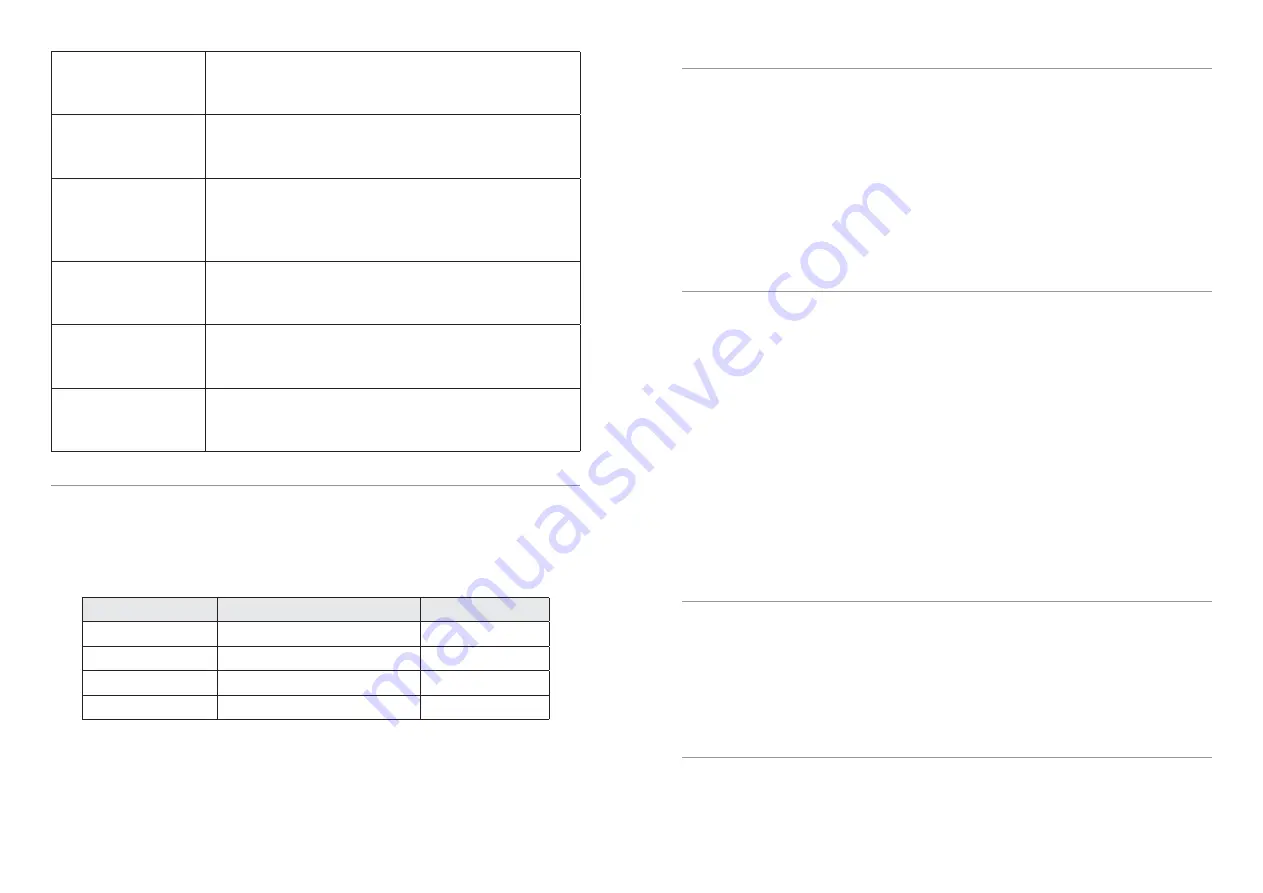
Insulation fault
A chassis leakage above the programmed threshold has been
detected. (May indicate an insulation fault, or even water inside
a DC motor.)
Low 12V battery
The voltage of the 12V auxiliary battery (power supply for the
EVMS) has dropped below the programmed threshold. May
indicate a weak battery or faulty DC/DC converter.
Precharge failed
Displayed if an error is detected during the precharge sequence,
either failing to start (usually a wiring fault) or taking too long to
finish (usually an unexpected load “downstream” from the main
contactor). The startup sequence is cancelled automatically.
Contactor seized
If using contactors with auxiliary switches and a discrepancy
is detected (contactor closed when it should be open, or vice
versa), this error will be displayed.
BMS - comms error
If the EVMS Core hasn’t received data from a BMS module for
a while (about 1 second), this error will appear and the traction
circuit will be shut down for safety.
Comms error to Core
If the EVMS Monitor hasn’t received data from the Core for
more than 1 second, this error will appear. Most commonly this
is due to a wiring fault on the CAN bus.
Peukert’s Effect
All batteries exhibit a reduction in available capacity depending on how fast they
are discharged, known as Peukert’s Effect. For most lithium batteries in EVs the effect is
negligible, but for lead acid batteries it can be quite significant. The EVMS can automatically
compensate for Peukert’s Effect for different battery types. The Peukert’s Exponent is modified
in the EVMS Core settings to suit your battery type as follows:
Peukert’s Exponent
Chemistry and type
Capacity at 1C
1.0
Lithium: LiCo, LiMn, LiFePO4
100% of C20
1.1
Lead acid: AGM
75% of C20
1.2
Lead acid: Gel cell
55% of C20
1.3
Lead acid: Flooded
40% of C20
Lead acid batteries have a capacity rated at C20 – that is, how many amp-hours the battery
can supply if discharged over a 20 hour period. When configuring the pack capacity in the
EVMS, use the C20 rate. Lithium batteries are typically rated at 1C, but they exhibit minimal
Peukert’s Effect so it is close enough to their C20 rate.
State of Charge drift and synchronisation
The EVMS uses a hall effect sensor for current measurement and, by integrating current over
time, calculating battery state of charge. While offering easy installation, safe isolation and
good linearity, hall effect current sensors can exhibit a small amount of zero-point drift and
inaccuracy at low currents, which can accumulate over time causing the reported SoC to
differ from the actual SoC. To mitigate this, the EVMS includes a system to automatically
resynchronise the SoC at the end of any full charge cycle, via programmable “Full voltage”
setting. Ideally, set this to a volt or two below the peak charge voltage of your charger. This
way at the end of each full charge, the SoC will be synchronised back to 100%.
The SoC can also be manually reset to 100% via the Options menu of the EVMS Monitor.
Stationary Applications
The EVMS configuration includes a setting for Stationary Mode, intended for use in battery
backup and off-grid power applications. In this mode, the Key input enables both Main
Contactor and Charge Enable outputs concurrently. An undervoltage cell will disable the
Main Contactor output (to remove any loads on the battery) and an overvoltage cell will
disable the Charge Enable output (to disable any charging sources). In both cases the outputs
are re-enabled once the voltage has recovered by 0.4V (i.e there is ±0.2V hysteresis around
the configured thresholds).
In Stationary Mode, the Charge Sense input is no longer used, typically the Aux Ctr output
will not be used, and precharging is not supported.
For LiFePO4, we recommend an undervoltage threshold of 2.8V (which results in 2.6V cutout
and 3.0V re-enabling for any loads on the battery), and an overvoltage threshold of 3.6V (for
3.8V charger cutout and 3.4V re-enabling). These thresholds give about 1% hysteresis on the
battery state of charge to avoid rapid cycling of the charger or outputs.
Use with system voltages above 320VDC nominal
The EVMS Core’s internal voltage measurement and isolation monitoring circuit has an
absolute maximum voltage rating of 400VDC, making it suitable for nominal battery pack
voltages up to about 320VDC. The Core may be used with higher voltages, but the
HV+
,
HV-
and
Main Ctr-
connections must be omitted. Precharging and isolation monitoring no longer
supported, and system voltage is instead calculated from the sum of all cells connected to
BMS modules.
Leakage / insulation fault detection
The EVMS Core has an internal high resistance connection (200Kohm) between the traction
circuit and the vehicle chassis. By monitoring microamps of current flowing across this
resistor, the EVMS Core can detect if the isolation between traction circuit and the vehicle
chassis is compromised, such as from damaged wiring insulation, excessive carbon buildup