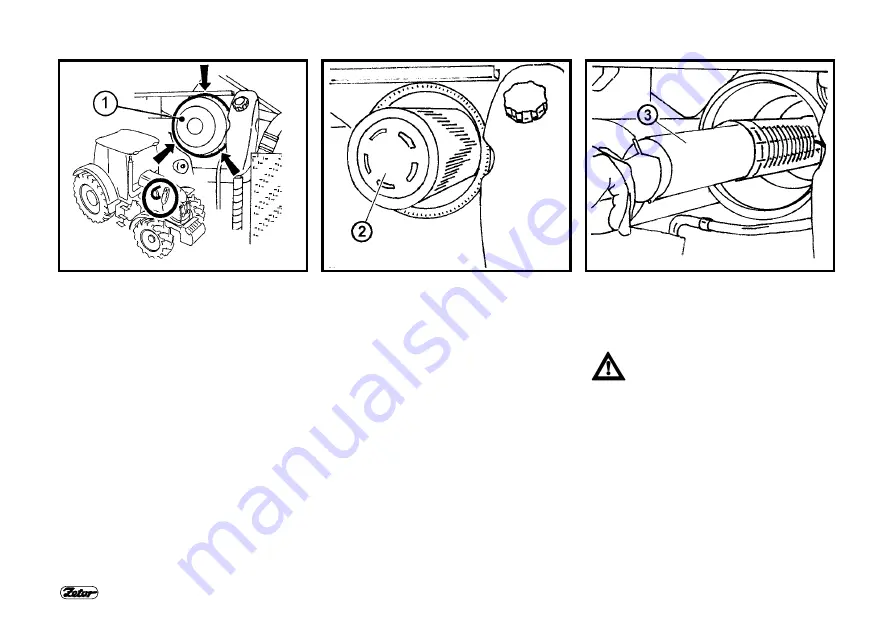
146
MAINTENANCE INSTRUCTIONS
X712 G713
QQQ_G714
INSTRUCTIONS FOR MAINTENANCE
OF DRY AIR CLEANER
Carry out maintenance of the air cleaner
as follows:
1. Lift the front bonnet.
2. Release clips of the air cleaner lid
(marked by arrows).
3. Remove the cleaner lid (1).
REGENERATION OF THE MAIN AIR
CLEANER CARTRIDGE
−
Pull out the main cartridge of the dry
cleaner (2).
Unless the main cartridge is damaged
(no dust may be on the inner surface of
the cartridge), carry out regeneration by
purging using compressed air from the
inner side of the cartridge.
This cleaning procedure may be re-
peated maximum three times. The car-
tridge shall be replaced every year.
REPLACEMENT OF AIR CLEANER
LOCKING CARTRIDGE
−
Pull out the locking cartridge of the dry
cleaner (3).
The locking cartridge cannot be
regenerated. It shall always be
replaced in these cases:
-
when the main cartridge is
damaged
-
after 5 maintenances of the air
cleaner
-
at least every two years
Summary of Contents for Proxima Plus 105
Page 1: ......
Page 2: ......
Page 7: ...7 LOCATION OF SERIAL NUMBERS G2...
Page 18: ...18 NOTES...
Page 34: ...34 GETTING TO KNOW THE TRACTOR E131...
Page 36: ...36 GETTING TO KNOW THE TRACTOR E132...
Page 48: ...48 NOTES...
Page 68: ...68 NOTES...
Page 82: ...82 NOTES...
Page 102: ...102 NOTES...
Page 114: ...114 NOTES...
Page 140: ...140 NOTES...
Page 160: ...160 NOTES...
Page 195: ...195 NOTES...
Page 197: ......