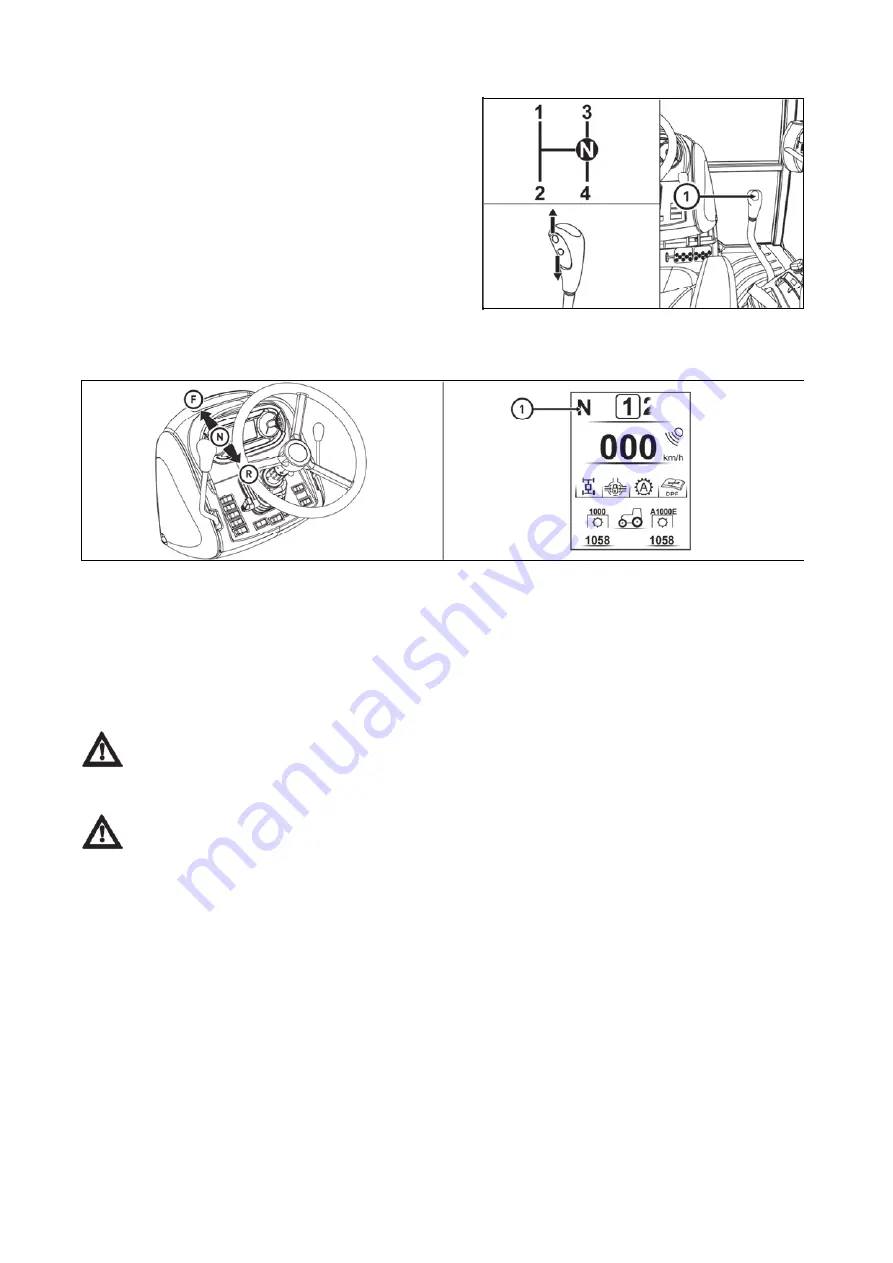
Gear shifting
Reversing lever
PGPPN184
Reversing lever selects direction of movements of the tractor (forward, backward).
F -
travel forward (16 speeds)
R -
travel backward (16 speeds)
The reversing gearbox includes 16 reverse speeds that are approximately the same as the forward speeds.
Therefore consider carefully when shifting a reverse gear for the given character of your work.
Perform reverse shifting with clutch pedal depressed and tractor in standstill.
The lever neutral position is indicated by the symbol
N
(1) on the instrument panel display.
When shifting individual gear speed (1-4) or reversing (F-R) observe the instructions for
putting the tractor in motion and gear shifting in this manual. When the tractor has been started and
is still standing, depress the clutch pedal and wait for approx. 2 seconds. Only then shift the required
gear speed or select the reverse direction.
To increase safety and to avoid unexpected situations use the foot brake during the shifting as well.
The tractors are equipped with a four-speed synchronized
transmission, a two-speed torque multiplier, a reverser
and a two-speed reduction.
The four-speed transmission is operated by the main
gearshift lever (1) with buttons for the torque multiplier
control.
The gearshift scheme is located on the gearshift knob
label and on the sticker on the right bottom windshield.
Reverse gear can only be shifted using the reverse shift
lever.
PGPPN018
OPERATION
82
Summary of Contents for Proxima GP Series
Page 1: ...OPERATOR S MANUAL PROXIMA GP 01 2019 Tractor is Zetor Since 1946 80 90 100 110...
Page 3: ...2...
Page 11: ...10...
Page 29: ...NOTES 28...
Page 55: ...NOTES 54...
Page 75: ...NOTES 74...
Page 95: ...NOTES 94...
Page 97: ...NOTES 96...
Page 105: ...NOTES 104...
Page 119: ...NOTES 118...
Page 151: ...NOTES 150...
Page 167: ...Fuse panel B PGPPN007 ELECTRIC INSTALLATION 166...
Page 183: ...NOTES 182...
Page 205: ...NOTES 204...
Page 219: ...NOTES 218...
Page 224: ...223...