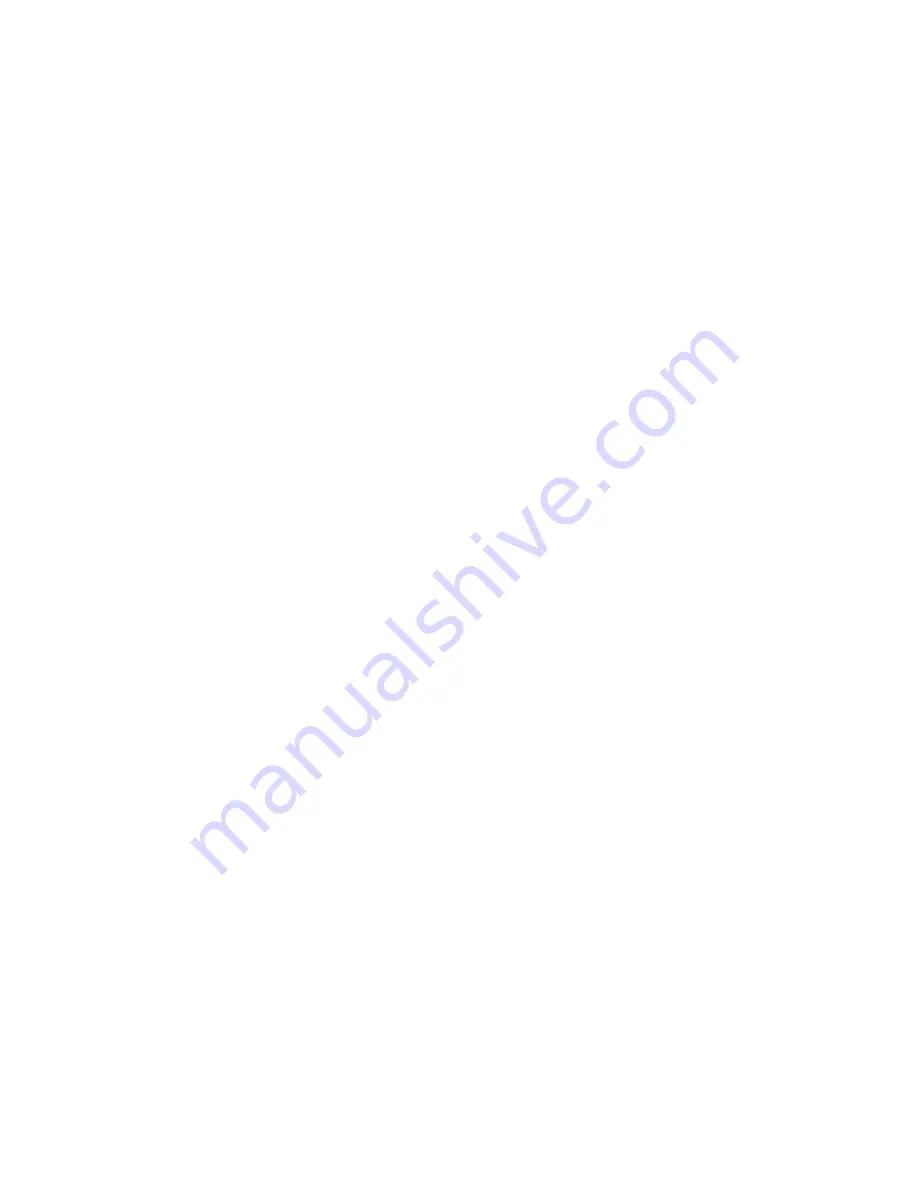
YZ Systems, Inc. • 3101 Pollok Drive • Conroe, Texas • USA • 77303 • P: 936.788.5593 • F: 936.788.5720
Page 28
DP-2010FU ver.04202004
SSSSS
ECTION
ECTION
ECTION
ECTION
ECTION
8:
8:
8:
8:
8: M
M
M
M
M
ECHANICAL
ECHANICAL
ECHANICAL
ECHANICAL
ECHANICAL
S
S
S
S
S
Y
YY
Y
YSTEM
STEM
STEM
STEM
STEM
DP-2000 Sample Pump
is a positive displacement plunger
pump. It’s dependable design provides for
dependable sampling service, while also provid-
ing a very simple to maintain pump, with very
few internal components. The pump has an
adjustable displacement of .1 to .4 cc per stroke.
The set displacement may be viewed at the
volume adjustment knob,
DP-2000 pump. Adjustment is simple. Turn the
volume adjustment knob clockwise to increase
the pump volume displacement per stroke, or
turn the volume adjustment knob counter clock-
wise to decrease the pump volume displacement
per stroke. Final control of the volume of sample
to be gathered during the sample cycle period, is
achieved by the Z-65 controller.
This pump has internal pressure balancing
capabilities that allows the pump to function
properly when the pipeline pressure is greater
that the sample vessel pressure, or when the
sample vessel pressure is greater than the
pipeline pressure.
Each time the pump strokes product previously
captured in the pump chamber is forced toward
the sample cylinder. As the pump plunger return
to a resting state a new fresh sample is captured
in the pump. Once the pump completes its
stroke, the cycle is ready to begin again.