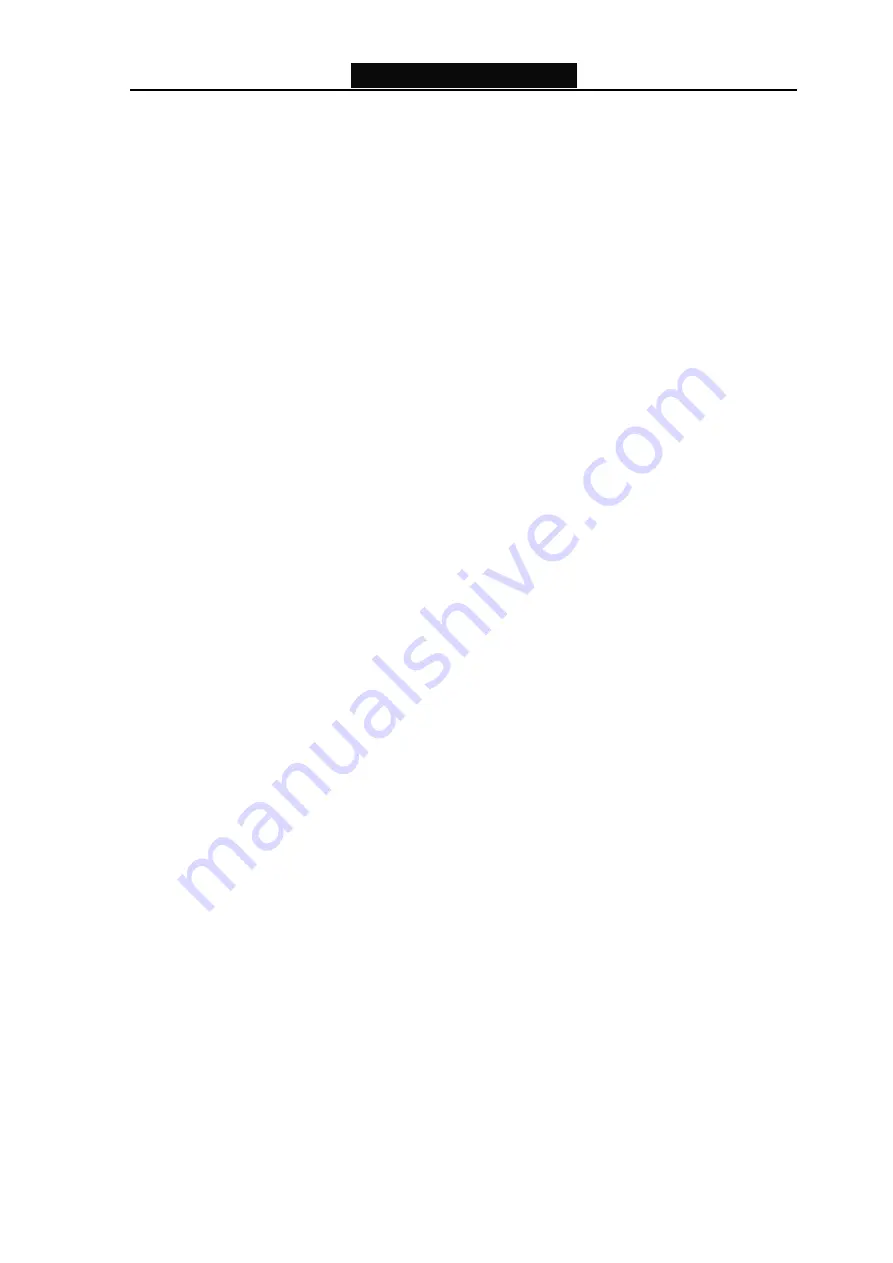
YUSHI INSTRUMENTS
39
7.6 Repairing
In order to get the optimal performance of YUT-2620, and minimize its failure rate, the latest
technology and quality components have been adopted. The process quality control and process testing
have passed ISO9001 International Quality System Authentication.
Sudden failure
In case failure occurs, please turn off the power and take out the batteries when necessary. Then
send the instrument to the appointed after-sales service center to have it repaired.
Under the following circumstances, the instrument won’t work safely:
a. The instrument suffered from evident mechanical damage. (For example it was badly collided or
squeezed during the process of transportation.)
b. The keyboard or the display screen can’t work normally.
c. It is kept in a place of high temperature, high humidity or corrosivity.
Chapter 8 Communication between the Instrument and the
Computer
8.1 The Communication between YUT-2620 and the computer and the use
of data processing software
The communication function means transporting the pre-saved waveforms and related parameters
in the instrument into the computer and generating flaw detecting reports, which can enable the
computer to control and manage the ultrasonic defectometer. It can realize single width transfer and
continuous transfer.
Connect one end of the communication cable with the communication interface. The red pot of the
interface should be aligned with the red pot on the instrument. The other end of the communication cable
should be connected with the COM1 (or COM2) interface on the PC. The instrument will transmit the