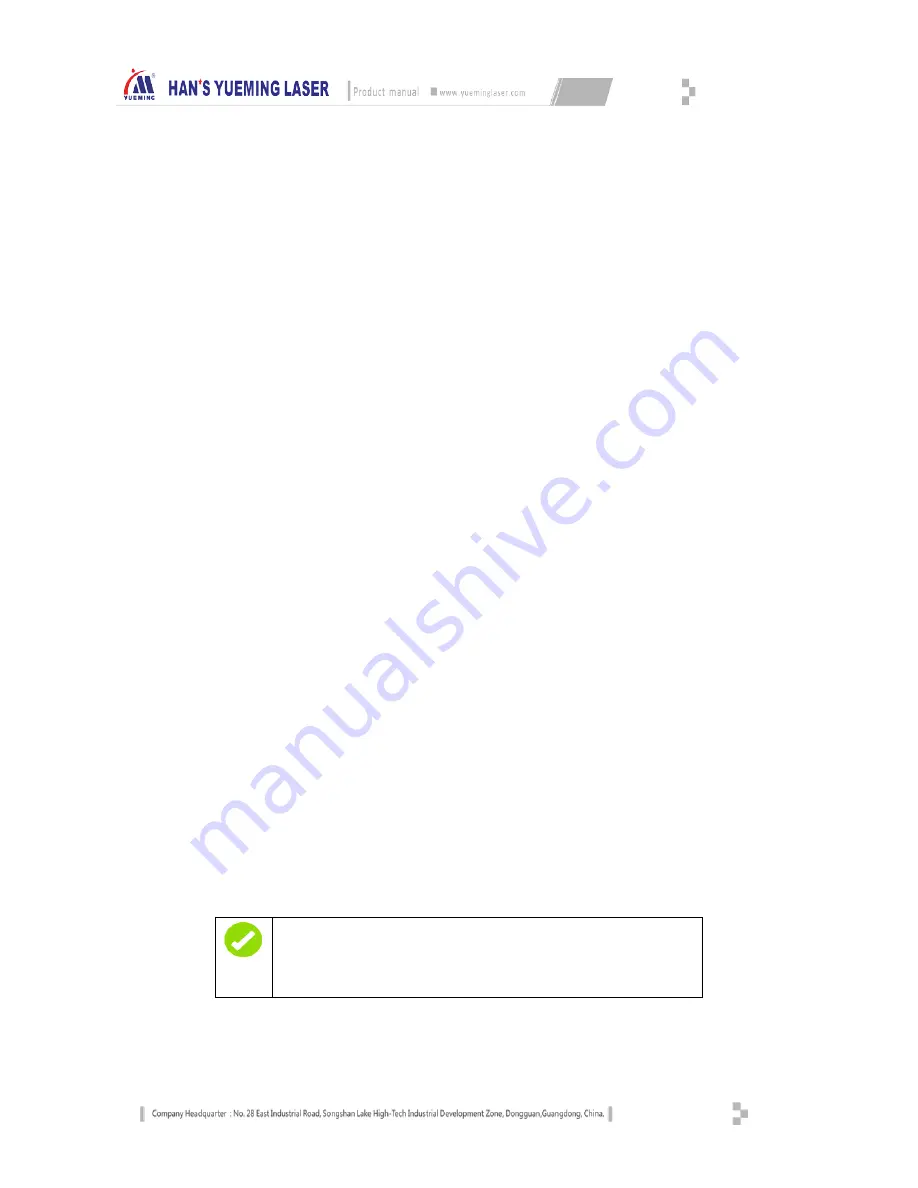
32
4.3 Maintenance of Optical Path and Optical Devices
The beam path system include beam combiner and the lens. after long time working or the mechanical
shake, the beam path will be changed, so suggest that check the laser beam path first before start the work.
Correctly, and regular maintenance of the optical system, which can effectively extend the service life of laser
device and decrease the cost of the use of the lens.
In the process of replacement, the placement of optical lenses, testing, installation, should pay attention to the
lens from damage and contamination. A new lens installation after in use, should be regularly cleaned. The
correct cleaning methods, will prolong the service life of the lens, and reduce the costs; On the contrary, will
reduce the service life.
When laser working, inevitably optical element contact suspension. When the laser was cutting or engraving on
the part of the cutting dust generating material cutting, carving, marking, material surface could release a large
number of corrosive gas and dust, the gas and dust will cause harm to the lens. When pollutants fell on the
surface of the lens, will absorb energy from the laser beam, lead to the thermal lens effect. If the lens have not
form the thermal stress, the operator can be disassembled and cleaned. of course, shall be made in a certain way
to avoid damage to the lens and further pollution.
General Operation Principles
In the installation and cleaning process of lens, any sticky material, even nail print or oil droplets, will increase the
absorption rate of the lens and reduce service life.
Therefore, the following precautions are required:
Do not use suction device or inflatable equipment to avoid scratching the lens surface;
Hold the edge of the lens rather than the film when take lens;
The lens should be stored in a dry and clean place for testing and cleaning. A good console should have
several layers of cleaning tissue or lens tissue on the surface;
The operator should avoid talking over the lens, and keep food, beverages and other potential contaminants
away from the working environment.
The correct cleaning method
①
Against mild pollution (dust, fiber particles) for flexible clean
Before the following steps, use a balloon blowing off the dust on the lens surface, if still can not remove the
pollutant, please go to step
②
.
②
for mild pollution stains, fingerprints) for flexible clean
With acetone or isopropyl alcohol extract infiltrates an unused degreased cotton swabs about 30 seconds on
the mirror surface cleaning, cleaning swab with slight pressure do from the center of the circle to the outside
Note
Avoid using workshop air pipes, because they contain a lot of water
and oil. These pollutant can be harmful in lens surface absorption
layer.