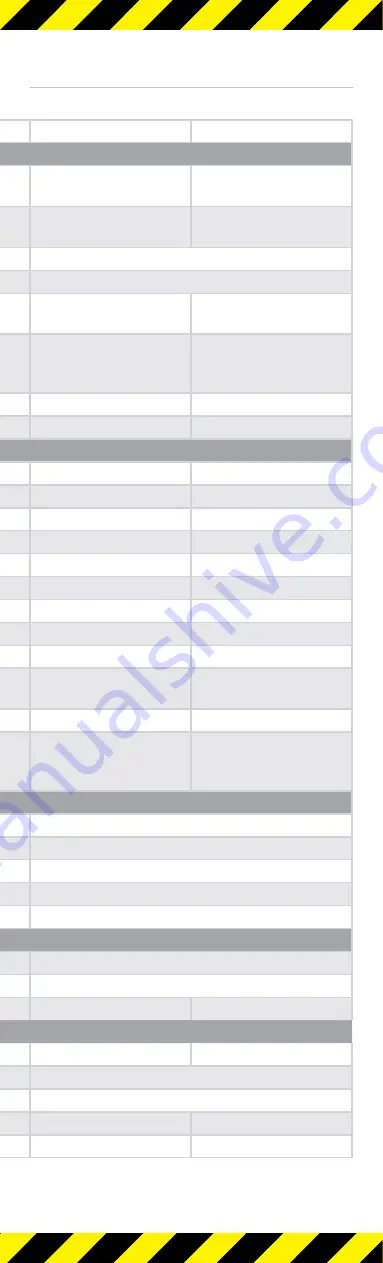
11
youngmangroup.com
Measurments:
Metric
Imperial
Rated load, manual forces and weight:
Safe working load
150kg
(inc on platform extension)
331lbs
(inc on platform extension)
equivalent to
(1 person (80kg) plus 70kg
tools & materials)
(1 person (176lbs) plus
154lbs tools & materials)
Maximum allowable manual force
200N
Maximum allowable chassis inclination
1.5
°
Maximum allowable wind speed
12.5m/s
(with platform closed)
28mph
(with platform closed)
Maximum load per wheel
420kg (based on drive
wheels – swivel castor
rating is 500kg)
926lbs (based on drive
wheels – swivel castor
rating is 1102lbs)
Machine weight
495kg
1091lbs
Maximum point loading
14.83kg/cm
²
211psi
Dimensions:
Maximum platform height
3.14m
10’4”
Minimum platform height
0.63m
2’1”
Maximum safe working height
5.14m
16’10”
Platform delay on descent height
1.86m
4’7”
Platform width
0.7m
2’4”
Platform length
1.25m-1.65m
4’1”-5’5”
Platform guardrail height
1.1m
3’7”
Toeboard height
0.15m
6”
Overall width
0.76m
2’6”
Stowed height
1.74m (0.89m with
guardrails removed)
5’9” ( 2’11” with guardrails
removed)
Stowed length (with step deployed)
1.39m
4’7”
Ground clearance
Platform lowered
0.045-0.09m
Platform raised 0.01m
Platform lowered 2”- 4”
Platform raised 0.4”
Electrical:
Voltage
24V DC
Power pack motor
1.2kW DC
Drive wheel motors
24V/2800rpm/0.5kW
Batteries (deep cycle/sealed gel)
2 x 12V/100Ah
Battery charger
100-120V/200-240V (automatic switching)
Hydraulics:
Maximum hydraulic pressure
255 bar
Working pressure
150 bar
Hydraulic fluid reservoir
1.5 litres
0.33 gallons
Performance:
Maximum number of lifts and descents on one charge:
350 (150kg load)
211 psi
Ascent time
19 seconds (150kg load)
Descent time
21 seconds (150kg load)
Maximum driving speed (platform lowered)
65m/minute
2.42mph
Maximum driving speed (platform raised)
13.5m/minute
0.5mph
2.1 technIcAl DAtA
Summary of Contents for BoSS X3X-SP
Page 45: ...43 youngmangroup com Notes...
Page 46: ...44 BoSS X3X SP Instructions for Use Notes...
Page 47: ...45 youngmangroup com Notes...