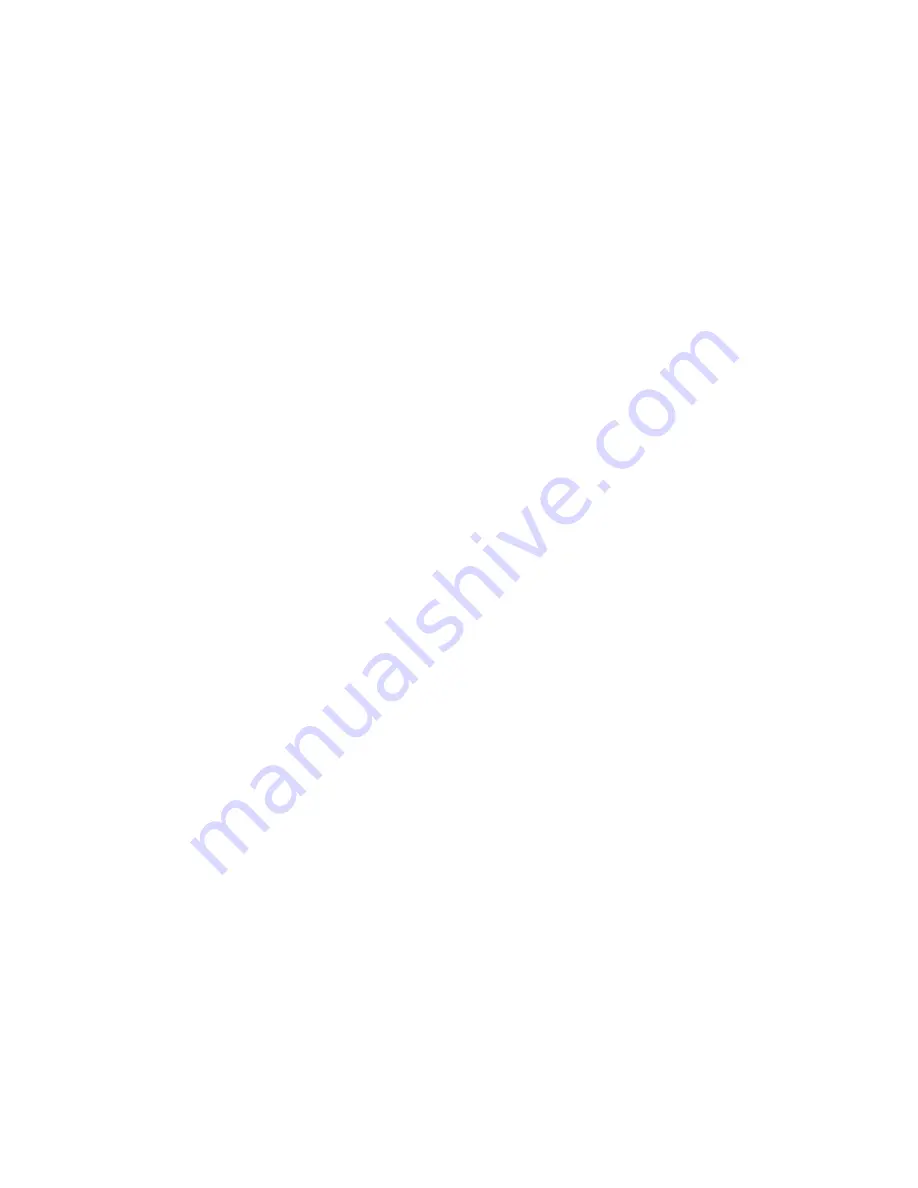
JOHNSON CONTROLS
124
FORM 161.01-OM1
ISSUE DATE: 6/8/2018
SECTION 5 - MAINTENANCE
CONDUCT PRESSURE TEST
If a pressure test indicates all joints are not leaking,
proceed to test with appropriate refrigerant as follows:
1. With no pressure in the system, charge refrigerant
vapor into the chiller until pressure is at least 30
psig (206 kPa) so pressure is above the saturation
temperature for water to freeze.
2. Add refrigerant until the saturation pressure for
the prevailing ambient temperature of the chiller
is achieved, leak checking repaired joints with a
refrigerant leak detector as pressure is increased.
3. Test around each joint and factory weld carefully
and thoroughly.
4. To check for tube or tube joint leaks:
a. Isolate and drain the condenser and evapora-
tor waterboxes
b. Purge the waterboxes and tubes with dry ni-
trogen through the vents or drains until the
detector does not indicate
c. Close the vents and drains and wait an hour
d. Open a vent or drain and insert the leak de-
tector. If a leak is detected, the heads must
be removed and the source of the leak de-
termined as outlined in the
REFRIGERANT CHARGING
To avoid the possibility of freezing liquid within the
evaporator tubes when charging an evacuated system,
only refrigerant vapor from the top of the drum or cyl-
inder must be admitted to the system until the system
pressure is raised above the point corresponding to the
freezing point of the evaporator liquid.
While charging, every precaution must be taken to pre-
vent moisture laden air from entering the system. Make
up a suitable charging connection from new copper
tubing to fit between the system charging valve and the
fitting on the charging drum. This connection should
be as short as possible but long enough to permit suf-
ficient flexibility for changing drums. The charging
connection should be purged each time a full container
of refrigerant is connected and changing containers
should be done as quickly as possible to minimize the
loss of refrigerant.
Refrigerant may be furnished in cylinders containing
either 100 lbs or 1900 lbs. (45 kg or 862 kg) of refrig-
erant.
CHECKING THE REFRIGERANT CHARGE
The refrigerant charge is specified for each chiller
model in
. Charge the correct
amount of refrigerant.
Charge the refrigerant in accordance with the method
shown in this section. The weight of the refrigerant
charged should be recorded after initial charging.
During operation, the refrigerant charge level is cor-
rect when the condenser level is above the subcooler,
and the measured Evaporator Approach and Discharge
Refrigerant Gas Superheat are at the design values
for the condition. Design values would be provided
upon request from the chillers sales engineer from the
chiller rating program. These depend on tube selection,
chilled fluid type, operating head, and operating condi-
tion. The equations (below) define these parameters.
Condenser level is detected by the liquid level sensor
and controlled to the programmed setpoint by the chill-
er control logic.
Equations
• Evaporator Approach = (LELT) - (SET)
• Discharge Superheat = (CDGT) - (SCT)
Definitions:
• SET = Saturated Evaporator Temperature
• LELT = Leaving Evaporator Liquid Temperature
• CDGT = Compressor Discharge Gas Temperature
• SCT = Saturated Condensing Temperature
The parameters can be viewed on the control center.
The chiller must be at design operating conditions
and full load operation before the correct refrigerant
charge level can be properly determined when oper-
ating. When proper condenser level is set, evaporator
approach can be trended at constant operating points to
monitor potential loss of charge.
Liquid refrigerant will be visible in the evaporator
sight glass, but the refrigerant charge amount cannot be
properly determined by viewing the liquid refrigerant
level in the evaporator sight glass. The level changes
due to suction conditions and load. If exact conditions
are repeated, level should repeat in the glass from a
known baseline.
Summary of Contents for YZ MODEL A
Page 10: ...JOHNSON CONTROLS 10 FORM 161 01 OM1 ISSUE DATE 6 8 2018 THIS PAGE INTENTIONALLY LEFT BLANK...
Page 142: ...JOHNSON CONTROLS 142 FORM 161 01 OM1 ISSUE DATE 6 8 2018 Appendix Material Safety Data Sheets...
Page 143: ...JOHNSON CONTROLS 143 Appendix Material Safety Data Sheets FORM 161 01 OM1 ISSUE DATE 6 8 2018...
Page 144: ...JOHNSON CONTROLS 144 FORM 161 01 OM1 ISSUE DATE 6 8 2018 Appendix Material Safety Data Sheets...
Page 145: ...JOHNSON CONTROLS 145 Appendix Material Safety Data Sheets FORM 161 01 OM1 ISSUE DATE 6 8 2018...
Page 146: ...JOHNSON CONTROLS 146 FORM 161 01 OM1 ISSUE DATE 6 8 2018 Appendix Material Safety Data Sheets...
Page 147: ...JOHNSON CONTROLS 147 Appendix Material Safety Data Sheets FORM 161 01 OM1 ISSUE DATE 6 8 2018...
Page 148: ...JOHNSON CONTROLS 148 FORM 161 01 OM1 ISSUE DATE 6 8 2018 Appendix Material Safety Data Sheets...
Page 149: ...JOHNSON CONTROLS 149 Appendix Material Safety Data Sheets FORM 161 01 OM1 ISSUE DATE 6 8 2018...
Page 150: ...JOHNSON CONTROLS 150 FORM 161 01 OM1 ISSUE DATE 6 8 2018 Appendix Material Safety Data Sheets...
Page 151: ...JOHNSON CONTROLS 151 Appendix Material Safety Data Sheets FORM 161 01 OM1 ISSUE DATE 6 8 2018...
Page 152: ...JOHNSON CONTROLS 152 FORM 161 01 OM1 ISSUE DATE 6 8 2018 Appendix Material Safety Data Sheets...
Page 153: ...JOHNSON CONTROLS 153 Appendix Material Safety Data Sheets FORM 161 01 OM1 ISSUE DATE 6 8 2018...
Page 154: ...JOHNSON CONTROLS 154 FORM 161 01 OM1 ISSUE DATE 6 8 2018 Appendix Material Safety Data Sheets...