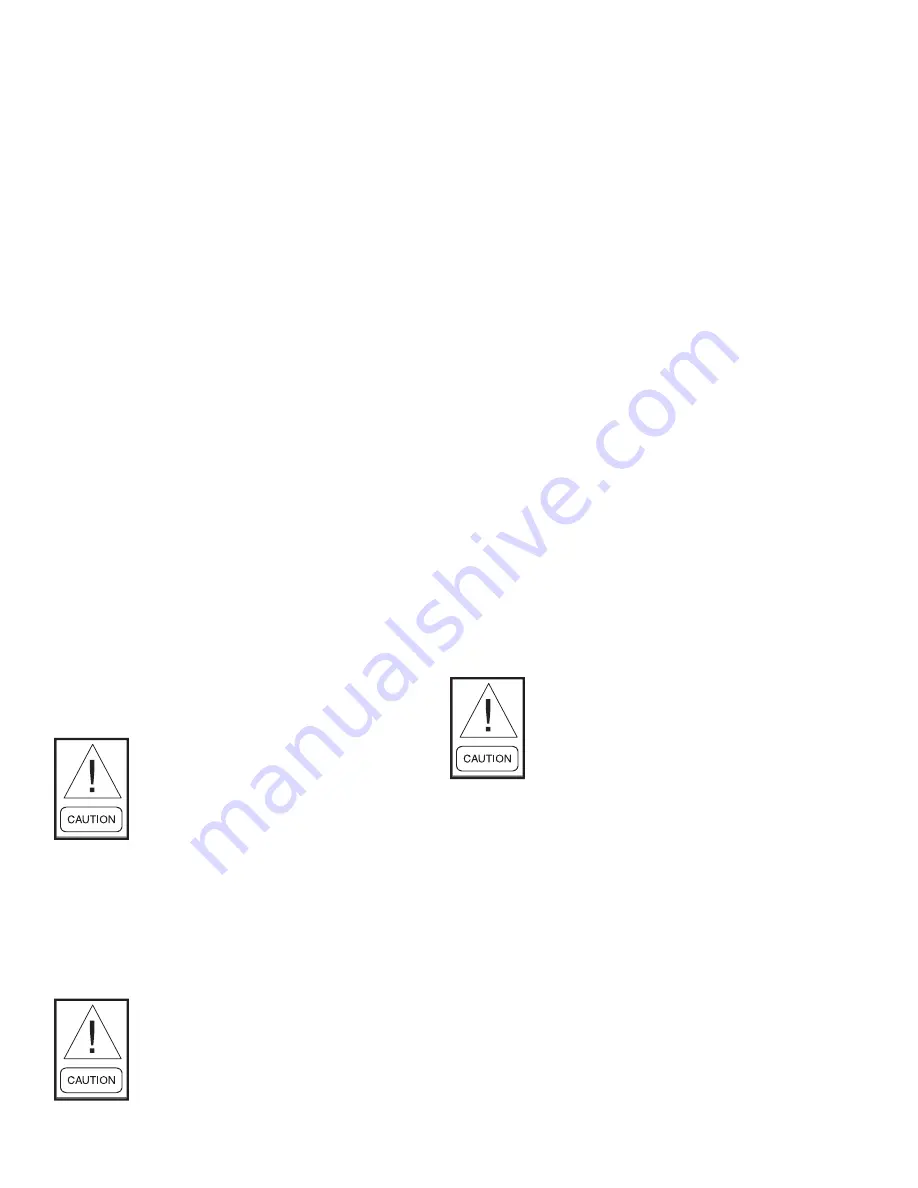
FORM 201.23-CL1 (309)
6
JOHNSON CONTROLS
Sight glasses will vary in type depending upon
the manufacturer of the separator. One type will
have balls that float in the sight glasses to indicate
level. Another type will have a bulls' eye glass. The
bulls' eye glass will tend to appear to lose the lines
in the bulls' eye when the level is above the glass.
Oil level should not be above the top sight glass.
In the rare situation where oil levels are high, drain
oil to lower the level to the bottom of the top sight
glass.
Oil levels in the oil separators above the top sight
glass in either oil separator should be avoided and
may cause excessive oil carryover in the system.
High oil concentration in the system may cause
nuisance trips resulting from incorrect readings
on the level sensor and temperature sensors.
Temperature sensor errors may result in poor
refrigerant control and liquid overfeed to the com-
pressor.
In the unlikely event it is necessary to add oil, con-
nect a YORK oil pump to the charging valve on the
oil separator, but do not tighten the flare nut on the
delivery tubing. With the bottom (suction end) of
the pump submerged in oil to avoid entrance of air,
operate the pump until oil drips from the flare nut
joint, allowing the air to be expelled, and tighten the
flare nut. Open the Compressor oil charging valve
and pump in oil until it reaches the proper level as
described above.
When oil levels are high, adding oil
may not visibly increase the level in the
separators during operation. This may
be an indication the level is already too
high and the oil is being pumped out
into the system where it will cause heat
transfer and control problems.
6. Ensure water pumps are on. Check and adjust
water pump flow rate and pressure drop across the
cooler.
Excessive flow may cause catastrophic
damage to the evaporator.
7. Check the control panel to ensure it is free of
foreign material (wires, metal chips, tools,
documents, etc.).
8. Visually inspect wiring (power and control). Wiring
MUST meet N.E.C. and local codes
.
9. Check tightness of the incoming power wiring
inside the power panel and inside the motor ter-
minal boxes.
10. Check for proper size fuses in control circuits.
11. Verify that field wiring matches the 3-phase power
requirements of the chiller.
12. Be certain all water temperature sensors are inserted
completely in their respective wells and are coated
with heat conductive compound.
13. Ensure the suction line temperature sensors are
strapped onto the suction lines at 4 or 8 O’clock
positions.
14. Assure the glycol level in the VSD cooling system
is 9-15 inches (23-28 cm) from the top of the fill
tube. This check should be performed prior to run-
ning the pump.
15. Check to assure the remote start/stop for Sys #1
on Terminals 2 to 15 and Sys #2 on Terminals 2 to
16 are closed on the User Terminal Block 1TB to
allow the systems to run. If remote cycling devices
are not utilized, place a wire jumper between these
terminals.
Never run the glycol pump without
coolant! Running the glycol pump
without coolant may damage the pump
seals.
Always fill the system with approved
YORK coolant to avoid damage to the
pump seals and the chiller.
16. Ensure that the CLK jumper JP2 on the Chiller
Control Board is in the ON position.
17. Assure a flow switch is connected between
Terminals 2 and 13 on the User Terminal Block
1TB in the panel. Throttle back flow to assure
the flow switch opens with a loss of flow. It is
recommended that auxiliary pump contacts be
placed in series with the flow switch for additional
protection, if the pump is turned off during chiller
operation. Whenever the pump contacts are used,
the coil of the pump starter should be suppressed
with an RC suppressor (031-00808-000).