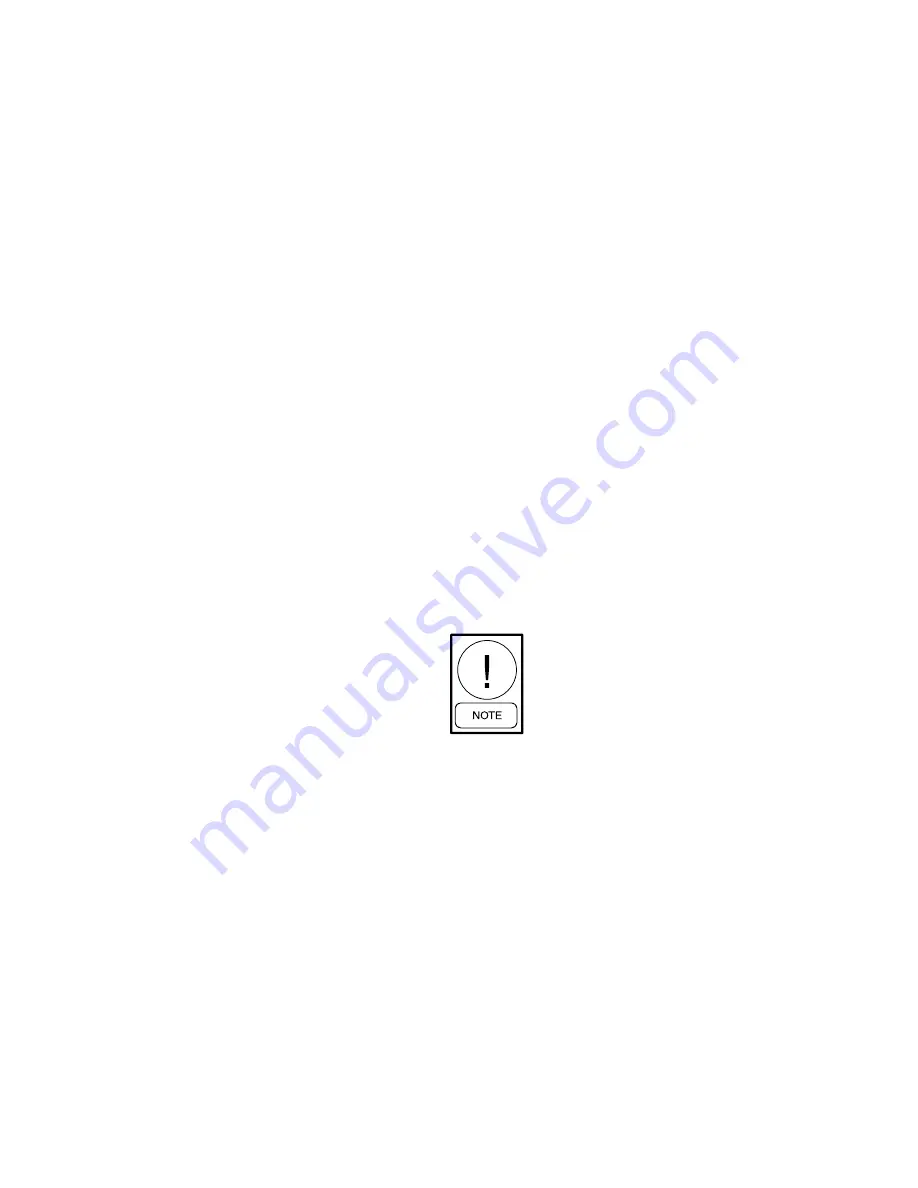
JOHNSON CONTROLS
36
FORM 150.66-NM3
ISSUE DATE: 09/25/2020
SECTION 4 - INSTALLATION
Field Wiring
–
Power wiring must be provided
through a fused disconnect switch to the unit terminals
(or optional molded disconnect switch) in accordance
with N.E.C. or local code requirements. Minimum cir-
cuit ampacity and maximum dual element fuse size are
given in
.
A 120-1-60, 15 amp source must be supplied for the
control panel through a fused disconnect when a con-
trol panel transformer (optional) is not provided
. See
).
Refer to unit wiring diagrams for field and power wir
-
ing connections, chilled water pump starter contacts,
alarm contacts, compressor run status contacts, PWM
input, and load limit input. See
for a detailed description of operation
concerning aforementioned contacts and inputs.
Evaporator Pump Start Contacts
Terminal block TB1 – terminals 23 to 24, are nor mally-
open contacts that can be used to switch field supplied
power to provide a start signal to the evapo rator pump
contactor. The contacts will be closed when any of the
following conditions occur:
1. Low Leaving Chilled Liquid Fault
2. Any compressor is running
3. Daily schedule is not programmed OFF and the
Unit Switch is ON
The pump will not run if the micro panel has been pow-
ered up for less than 30 seconds, or if the pump has run
in the last 30 seconds, to prevent pump motor over-
heating. See
and refer to the unit wiring dia gram.
System Run Contacts
Contacts are available to monitor system status. Nor-
mally-open auxiliary contacts from each com pressor
contactor are wired in parallel with TB1 – terminals 25
to 26 for system 1, and TB1 – termi nals 27 to 28 for
system 2 (YCAL0041 - YCAL0071). See
and
refer to the unit wiring dia gram.
Alarm Status Contacts
Normally-open contacts are available for each re-
frigerant system. These normally-open contacts close
when the system is functioning normally. The respec-
tive contacts will open when the unit is shut down on a
unit fault, or locked out on a system fault. Field connec-
tions are at TB1 terminals 29 to 30 (system 1), and ter-
minals 31 to 32 (system 2 YCAL0041 - YCAL0071).
Remote Start/Stop Contacts
To remotely start and stop the chiller, dry contacts can
be wired in series with the flow switch and CTB1 -
termi nals 13 to 14. See
ing dia gram.
Remote Emergency Cutoff
Immediate shutdown of the chiller can be accomplished
by opening a field-installed dry contact to break the
elec trical circuit between terminals 5 to L on terminal
block
TB1
. The unit is shipped with a factory jumper
installed between terminals 5 to L, which must be re-
moved if emergency shutdown contacts are installed.
See
and refer to the unit wiring dia gram.
PWM Input
The PWM input allows reset of the chilled liquid set-
point by supplying a “timed” contact closure. Field
wiring should be connected to CTB1 – terminals 13 to
20. A detailed explanation is provided in the Unit Con-
trol section. See
Control / Power Panel Components on
and refer to the unit wiring diagram.
Load Limit Input
Load limiting is a feature that prevents the unit from
loading beyond a desired value. The unit can be “load
limited” either 33%, 40%, 50%, 66% or 80%, depend-
ing on the number of compressors on unit. The field
connections are wired to CTB1 – terminals 13 to 21,
and work in conjunction with the PWM inputs. A de-
tailed explanation is provided in the Unit Control sec-
Control / Power Panel Components on page
and refer to the unit wiring diagram.
When using the Load Limit feature,
the PWM feature will not function
– SIMULTANEOUS OPERATION
OF LOAD LIMITING AND TEM
PERATURE RESET (PWM INPUT)
CANNOT BE DONE.
Flow Switch Input
The flow switch is field wired to CTB1 terminals 13 -
Control / Power Panel Components on page
and refer to the unit wiring diagram.
COMPRESSOR HEATERS
Compressor heaters are standard. SM90 to SM160
compressors utilize 50 W heaters; SM185 compressors
utilize 75 W heaters. If power is OFF more than two
hours, the crankcase heaters must be energized for 18
to 24 hours before restarting a compressor. This will
ensure that liquid slugging and oil dilution does not
damage the compressors on start.
Summary of Contents for YCAL Series
Page 4: ...JOHNSON CONTROLS 4 FORM 150 66 NM3 ISSUE DATE 09 25 2020 THIS PAGE INTENTIONALLY LEFT BLANK...
Page 16: ...JOHNSON CONTROLS 16 FORM 150 66 NM3 ISSUE DATE 09 25 2020 THIS PAGE INTENTIONALLY LEFT BLANK...
Page 130: ...JOHNSON CONTROLS 130 FORM 150 66 NM3 ISSUE DATE 09 25 2020 THIS PAGE INTENTIONALLY LEFT BLANK...
Page 144: ...JOHNSON CONTROLS 144 FORM 150 66 NM3 ISSUE DATE 09 25 2020 THIS PAGE INTENTIONALLY LEFT BLANK...
Page 173: ...FORM 150 66 NM3 ISSUE DATE 09 25 2020 173 JOHNSON CONTROLS 10 NOTES...