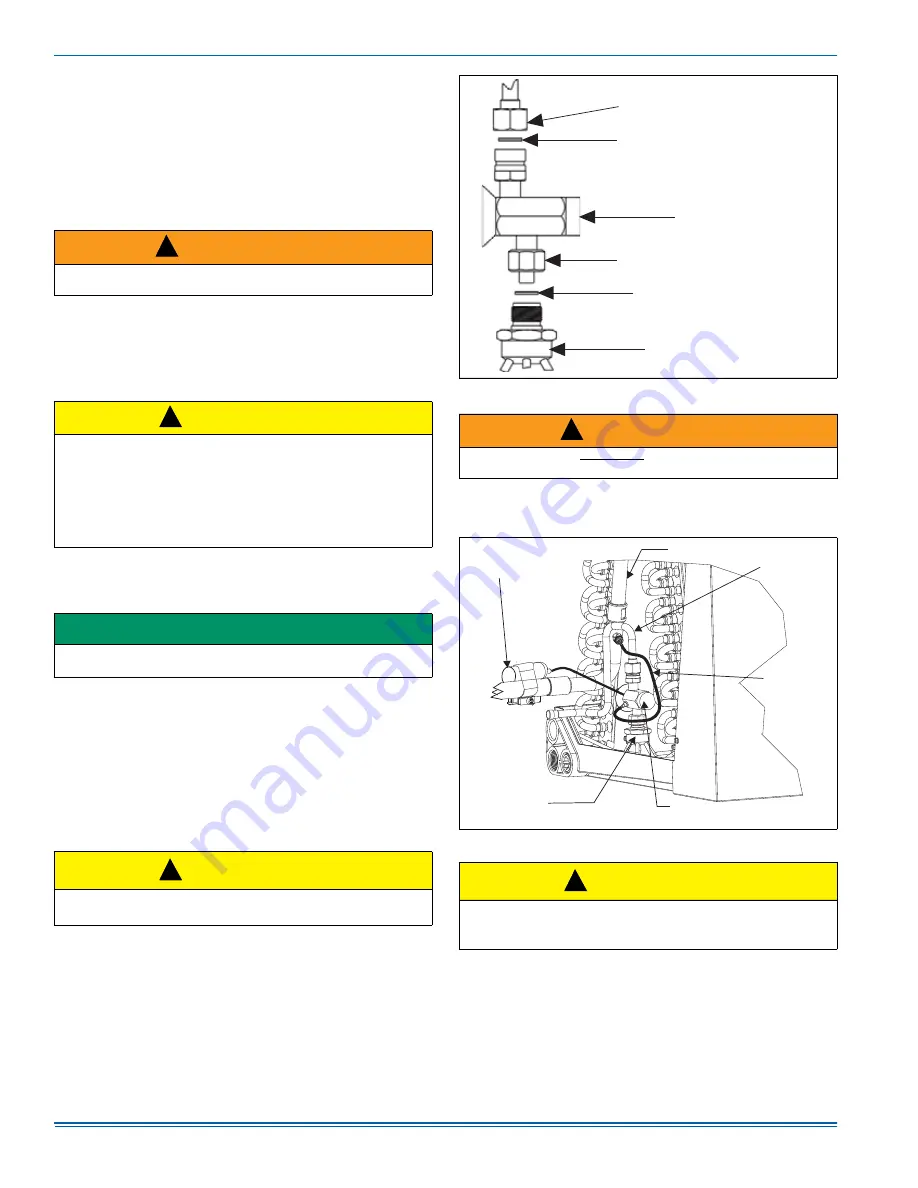
5604542-UIM-B-0419
6
Johnson Controls Ducted Systems
12. Release the refrigerant charge into the system. Open the liquid line
valve first, then the vapor line valve by removing the plunger cap
and turning the valve counter-clockwise using hex head wrenches.
Valves are fully open when the valve stem is touching the cham-
fered retaining wall at the top of the valve. If the service valve is a
ball type valve, use an adjustable end wrench to turn the valve stem
one quarter turn counter-clockwise to open it. DO NOT overturn or
the valve stem may break or become damaged. See PRECAU-
TIONS DURING BRAZING SERVICE VALVE.
13. Replace service valve cap finger tight, then tighten an additional 1/
12 turn (1/2 hex flat). Cap must be replaced to prevent leaks.
14. See “System Charge” section for checking and recording system
charge. See Section VI.
SECTION IV: INDOOR EXPANSION DEVICE
THERMOSTATIC EXPANSION VALVE
(
TXV)
INSTALLATION
The following are the basic steps for installation. For detailed instruc-
tions, refer to the Installation Instructions accompanying the TXV kit.
Install TXV kit as follows:
1.
Relieve the holding charge by depressing Schrader core on the
suction manifold stub out.
2.
After holding charge is completely discharged, loosen and remove
the Schrader core.
3.
Place a backup wrench on distributor, loosen and remove brass
distributor nut. Retain brass nut for use on liquid line. Keep Teflon
washer in place and discard clear disk.
4.
Install the thermal expansion valve to the distributor assembly with
supplied fittings. Ensure Teflon washer is seated in distributor.
Hand tighten and turn an additional 1/4 turn to seal. Do not over
tighten fittings. See Figure 6.
5.
Slide the nut removed in step 3 over the supplied liquid line. Place
supplied Teflon washer from TXV kit in place on TXV, and install liq-
uid line to the top of the thermal expansion valve. Adjust assembly
so liquid line aligns with hole in access panel. Hand tighten the liq-
uid line, and apply an additional 1/4 turn to seal.
6.
Install the TXV equalizer line onto the vapor line by hand tightening
the 1/4” SAE coupling nut to the equalizer fitting, and apply an
additional 1/3 turn to seal. See Figure 7.
7.
Pass the TXV temperature sensing bulb through the suction line
split grommet in the access panel.
WARNING
Never attempt to repair any brazed connections while the system is
under pressure. Personal injury could result.
CAUTION
Outdoor unit model numbers ending with an “H” have a factory
installed hard start kit which is required when a TXV is installed on the
indoor unit. Outdoor unit model numbers with no “H” ending do not
require a hard start kit unless a TXV is being installed on the indoor
unit or unless local regulations dictate it. The Tabular Data Sheet
which comes with the unit specifies whether or not a hard start kit is
required. When a TXV Kit is needed, it should be ordered from
Source 1.
IMPORTANT
Refer to the Technical Guide for the unit to determine the proper TXV
kit to be used on this product.
CAUTION
Do not over-torque. Do not use slip joint pliers. This will distort the
aluminum distributor and the brass fitting (potentially causing leaks).
!
!
!
FIGURE 6:
TXV Installation
WARNING
Schrader valve core
MUST NOT
be installed with TXV installation.
Poor system performance or system failure could result.
FIGURE 7:
TXV Bulb and Equalizer Line Installations
CAUTION
In all cases, mount the TXV bulb after vapor line is brazed and has
had sufficient time to cool. Failure to use suction line grommet may
result in premature TXV failure.
T
X
V
/
D
I
STR
IB
UTOR
COUP
LING
LI
QU
I
D
LIN
E
/
T
X
V
COUP
LING
TE
FL
O
N W
AS
H
ER
T
X
V
TE
FL
O
N W
AS
H
ER
D
I
STR
IB
UTOR
A
0281-001
!
T
X
V
B
U
LB
(Wrap with
insulation.)
VAPOR
LIN
E
LI
QU
I
D
LIN
E
TV
X
EQUA
LIZ
ER
LIN
E
T
H
ER
M
A
L
E
X
PA
N
S
I
O
N
VA
L
VE
(
T
X
V
)
D
I
STR
IB
UTOR
B
OD
Y
A
0279-002
!