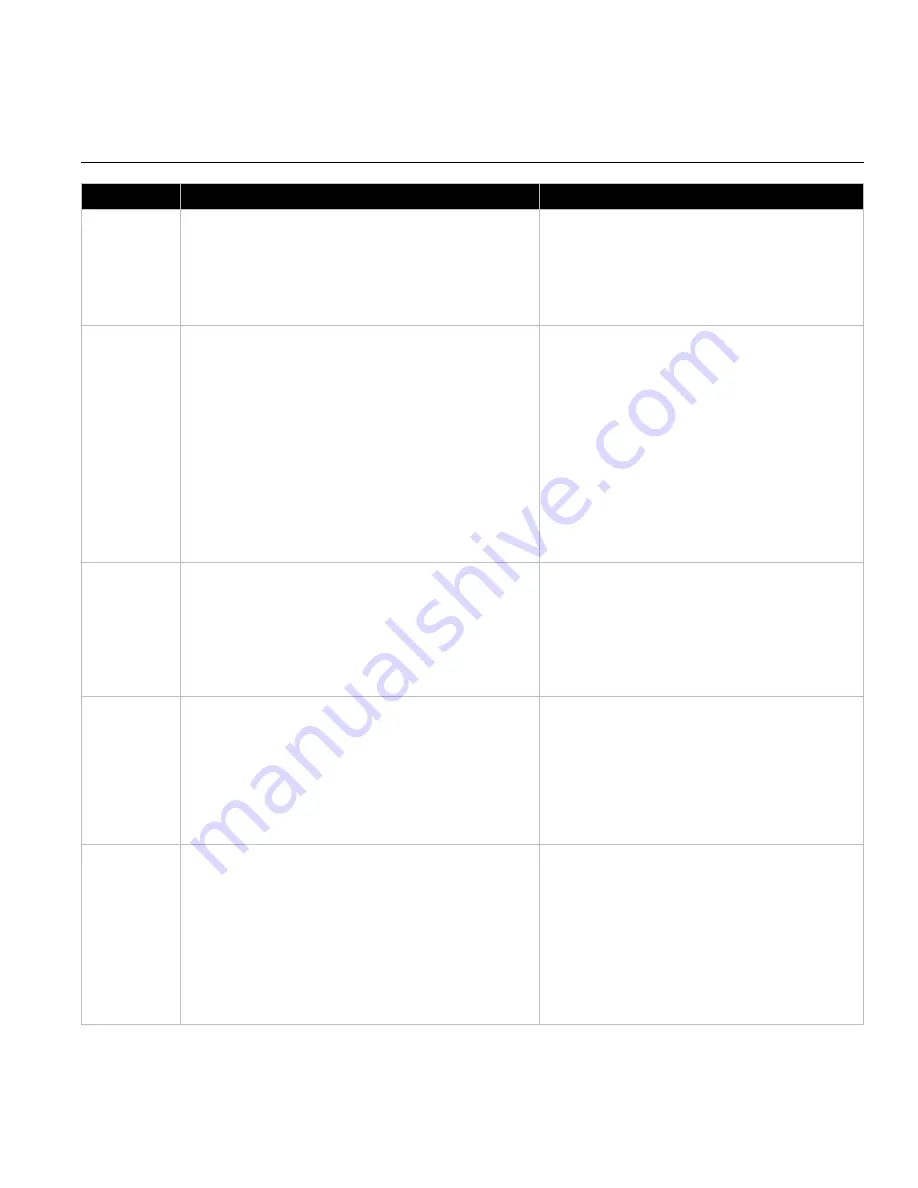
JOHNSON CONTROLS
11
TROUBLESHOOTING CHECKLIST
Symptom
Possible Cause(s)
Corrective Action
Capacity or
Pressure
Below Rating
1.
Total resistance of system higher than anticipated.
2.
Speed too low.
3.
Dampers or variable inlet varies improperly adjusted.
4.
Poor fan inlet or outlet conditions.
5.
Air leaks in system.
6.
Damaged impeller or incorrect direction of rotation.
1.
System problems.
2.
Adjust drive.
3.
Adjust.
4.
Elbows at or too close to fan.
5.
Seal joints / correct damper settings.
6.
Correct.
Vibration
and Noise
1.
Misalignment of impeller, bearings, couplings.
2.
Unstable foundation.
3.
Foreign material in fan causing unbalance.
4.
Worn bearings.
5.
Damaged impeller or motor.
6.
Broken or loose bolts or set screws, bent shaft, or worn
coupling.
7.
Impeller or driver unbalanced.
8.
60/120 Hz cycle magnetic hum due to electrical input.
9.
Fan delivering more than rated capacity.
10.
Loose dampers or VIVS.
11.
Speed too high or fan rotating in wrong direction.
12.
Vibration transmitted to fan from some other source.
1.
Loosen, align, tighten.
2.
Inferior design, start over.
3.
Remove.
4.
Replace bearings and shaft.
5.
Check and repair.
6.
Replace.
7.
Balance.
8.
Check for high or unbalanced voltage.
9.
Reduce speed.
10.
Adjust and tighten.
11.
Correct.
12.
Isolate.
Overheated
Bearings
1.
Too much grease in ball bearings.
2.
Poor alignment.
3.
Damaged impeller or drive.
4.
Bent shaft.
5.
Abnormal end thrust.
6.
Dirt in bearings.
7.
Excessive belt tension.
1.
Allow run time to purge (24 hours)
2.
Correct.
3.
Inspect, correct, or replace.
4.
Replace.
5.
Loosen set screws and adjust.
6.
Replace bearing; use filtered grease.
7.
Adjust.
Overloaded
Motor (Pulls Too
Many Amps)
1.
Speed too high.
2.
Discharge over capacity due to existing system resistance
being lower than original rating.
3.
Specific gravity or density of gas above design value.
4.
Wrong direction of rotation or poor alignment.
5.
Impeller wedging or binding on inlet ball.
6.
Bearings improperly lubricated.
7.
Motor improperly wired.
1.
Reduce speed or change HP.
2.
Adjust system resistance.
3.
Recalculate and correct.
4.
Correct.
5.
Loosen and adjust.
6.
See page
7.
Verify and correct.
Motor
Problems
1.
Check for low or high voltage from power source.
2.
High temperature; drawing too much current or dirt in
windings.
3.
Vibration and noise.
4.
Armature rubs against stator.
5.
Too much or not enough lubrication in bearings.
6.
Commutator brushes on d-c motor worn or not seated
under proper tension.
7.
Vibration and noise; loose hold down bolts.
8.
Low insulation resistance due to moisture.
1.
Correct voltage.
2.
Repair motor.
3.
Correct armature imbalance.
4.
Replace worn bearings.
5.
Correct lubrication.
6.
Repair motor.
7.
Tighten hold down bolts.
8.
Check resistance with a megohm meter (“Meggar”)
or similar instrument employing a 500 vold d-c
potential. Resistance should read at least 1 megohm.
Note: Care should be taken to follow all local electrical, safety and building codes. Provisions of the National Electric Code (NEC), as wells as the Occupational Safety and
Health Act (OSHA) should be followed. See additional notes on next page.