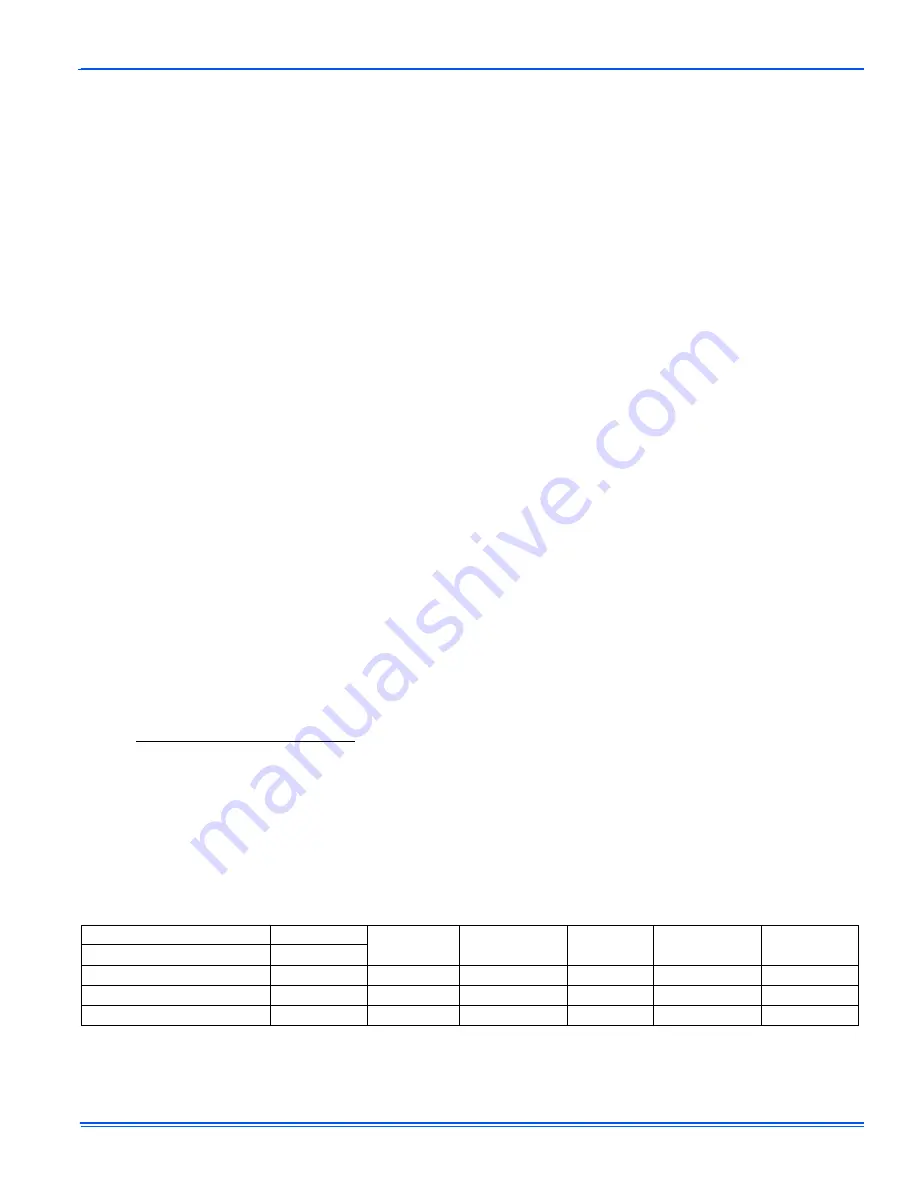
035-19643-001 Rev. B (0204)
Unitary Products Group
7
COOLING AIRFLOW
The cooling airflow is preset at the factory to provide approximately 90
percent of the maximum CFM and must be field adjusted to match the
HVAC system at installation. Refer to the outdoor unit installation
instruction for the recommended airflow for the cooling system.
Delay Taps Selection on the CFM / Timer Board
Pin Position A:
is the factory setting and is used for test purposes. The
blower will operate at 100% of the programmed cooling air flow for 60
seconds, with a 15 second coast to stop.
Pin Position B:
is for a two-stage condenser. This results in a 45 sec-
ond off delay at 82% of the programmed cooling airflow with a 15-sec-
ond coast to stop
Pin Position C:
is for a system with a TXV or solenoid valve. This
results in a 45 second off delay at 75% of the programmed cooling air-
flow with a 15-second coast to stop.
Pin Position D:
Is for a system without a TXV or solenoid valve. This
results in a 60 second off delay at 82% of the programmed cooling air-
flow with a 15-second coast to stop.
Cool and ADJ Taps Selection on the CFM / Timer Board
Pin Position A, B, C, and D:
The pin settings are dependent on the
model furnace and the CFM that is desired for your application. Table
16 in the installation manual has two columns under each model fur-
nace. These columns are the high / low speed CFM options for each
model. On the right side of the table there are two columns labeled
“COOL TAP” and “ADJ TAP”. Find the model furnace you have, scroll
down the high / low columns until you come to the desired CFM, then
go to the last two columns in that row to find the recommended “COOL
TAP” and “ADJ TAP” settings. Once you have found the settings, go to
the CFM / Timer Board. Under “TAP SELECTION” you will see a col-
umn labeled “COOL” and one labeled “ADJ”. Place the PINS on the
proper COOL setting and the proper ADJ setting that you found in the
table. Refer to Figure 7 for the location COOL, HEAT, DELAY and ADJ
TAP SELECTIONS and the pin positions on the CFM / Timer Board.
DIRECT DRIVE BLOWER MOTOR
A failed variable speed motor should always be replaced with a variable
speed motor suitable for the furnace model being serviced. However, if
one is not available, a direct-drive multi speed blower motor can be
used as a
TEMPORARY REPLACEMENT MOTOR
in the interim.
Removal of the Variable Speed Blower Motor Assembly:
The procedure for removing the variable speed blower assembly:
1.
Disconnect the electrical supply to the furnace and remove the
access doors.
2.
Remove blower assembly mounting screws and slide the blower
assembly out of the slots in the deck. If the two shipping screws
were not previously removed, also remove and discard these two
screws located on each front corner of the blower assembly.
3.
Loosen the blower wheel set screw that secures the blower wheel
to the blower motor shaft.
4.
Remove the motor mount bolts.
5.
Slide the variable speed motor out of the blower housing.
Reassembly of the Variable Speed Blower Motor Assembly:
1.
Slide the new variable speed motor in to the blower housing. Make
sure you line up the flat side on the motor shaft with the setscrew
on the hub in the center of the blower wheel.
2.
Install the motor mount bolts in to the fan housing.
3.
Center the indoor fan wheel in the fan housing and tighten the
blower wheel set screw on the flat side the blower motor shaft.
4.
Reinstall blower assembly mounting screws and slide the blower
assembly back in the slots in the deck. Do not reinstall the two
shipping screws were removed.
5.
Install the access doors.
6.
Restore power to the furnace and verify operation.
INSTALLATION OF PSC MOTOR:
The motor speed tap wires are connected to the 1/4" quick connect ter-
minal on the Integrated Control using the black jumper wire that is
secured to the wire harness inside the burner compartment and is
marked “PSC Motor”. Follow the instructions below to properly install
the PSC motor.
1.
Install the PSC direct drive motor into motor mount.
2.
Slide motor in motor mount insuring there is no interference
between moving and stationary parts. Position wire leads down-
ward. Tighten motor mount band screw to 30 in. lbs.
3.
Center the blower wheel in the blower housing and align the shaft
flat with the blower wheel set screw. Tighten setscrew to 30 in. lbs.
4.
Replace blower assembly and fasten with 5 screws
5.
Strap motor capacitor to electric panel. Refer to Table 2 for proper
capacitor selection.
6.
Fasten electric panel to blower housing.
7.
Remove red wire from circuit input terminal. Plug jumper wire
(attach to motor power harness) on 120-volt line terminal on igni-
tion control and jumper to circuit Input. Connect brown door switch
wire to jumper.
8.
Connect white main harness lead to Line neutral.
9.
Connect motor leads to cool, heat lo and heat high per electrical
wire diagram table in the Installation manual.
10. Connect brown capacitor leads from motor to capacitor and cover
terminals with boot supplied.
11.
The motor ground (green) wire is secured to the right front of the
blower mounting plate with a screw.
12. Restore power to the furnace and verify operation.
TABLE 2:
Replacement PSC Motor / Capacitor Information
High Fire Inputs
Airflow
Cabinet Size
Motor
Part Number
Motor
Horsepower
Capacitor
Part Number
Capacitor
Rating
BTU/H (kW)
CFM (m³)
80,000 (23.4)
1,200 (33.98)
B
024-23271-000
1/2
024-20045-000
7.5 f
100,000 (29.3)
2,000 (56.63)
C
024-23238-001
1.0
024-20446-000
15.0 f
120,000 (35.1)
2,000 (56.63)
D
024-23238-001
1.0
024-20446-000
15.0 f