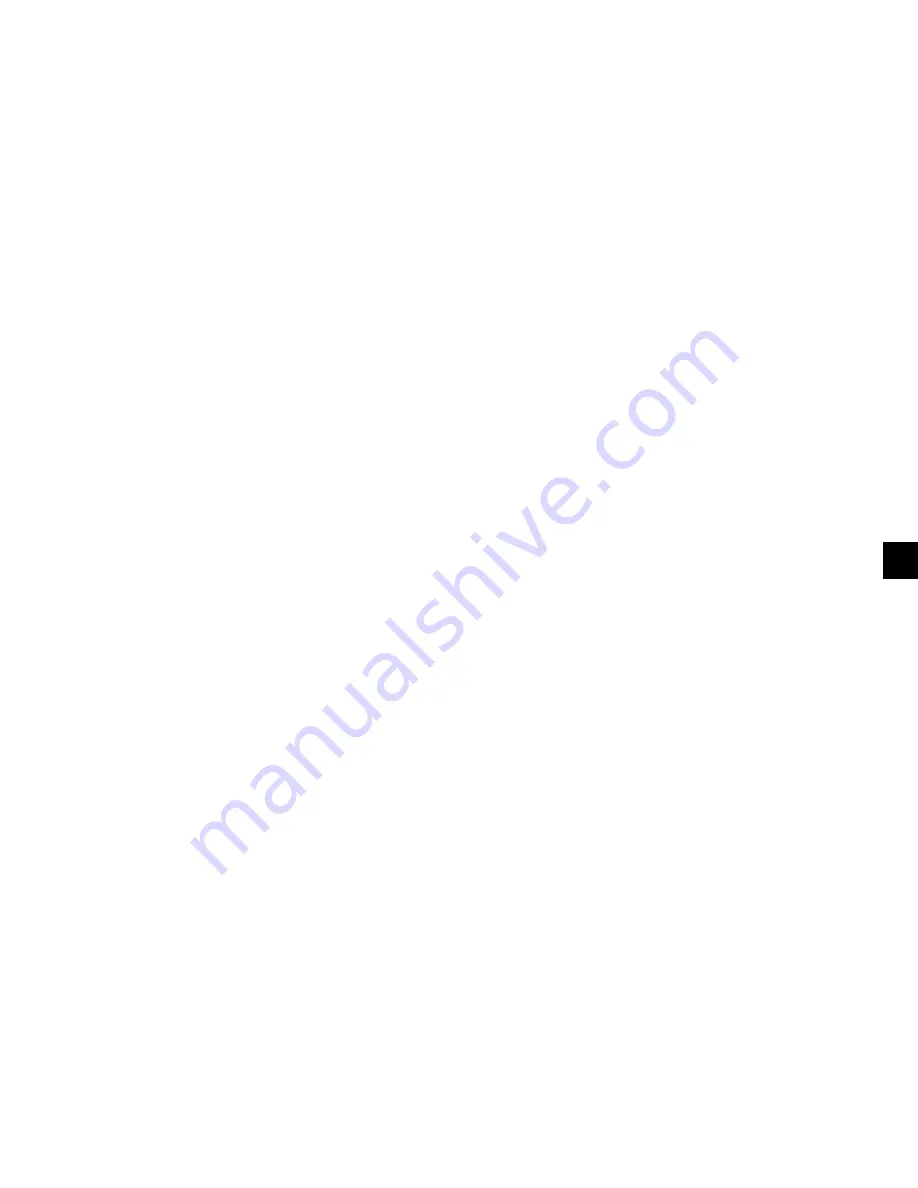
15
YORK INTERNATIONAL
FORM 201.18-NM4
tection of the compressor. Oil pressure safety is moni-
tored as the difference between suction and the pres-
sure of the oil entering the rotor case.
Maximum working pressure of the oil separator is 31
bar (450 PSIG). A relief valve is installed in the oil
separator piping. This will soon be incorporated into
the oil separator. Oil level should be above the mid-
point of the “lower” oil sight glass when the compres-
sor is running. Oil level should not be above the top of
the “upper” sight glass. Oil temperature control is pro-
vided through liquid injection activated by the micro-
processor, utilizing a discharge temperature sensor, and
a solenoid valve.
Oil Cooling
Oil cooling is provided by routing oil from the oil sepa-
rator through several of the top rows of the condenser
coils and back to the compressor.
Capacity Control
The compressors will start at the minimum load posi-
tion and provide a capacity control range from 10% -
100% of the full unit load using a continuous function
slide valve. The microprocessor modulates the current
signal to a 3-way pressure regulating capacity control
valve which controls command compressor capacity,
independent of system pressures, and balances the com-
pressor capacity with the cooling load. Loading is ac-
complished by varying pressure through the pressure
regulating capacity control valve to move the slide valve
against the spring pressure to promote stable smooth
loading.
Automatic spring return of the slide valve to the mini-
mum load position will ensure compressor starting at
minimum motor load.
Power and Control Panel
All controls and motor starting equipment are factory
wired and function tested. The panel enclosures are de-
signed to IP55 and are manufactured from powder
painted galvanized steel.
The Power and Control Panel are divided into power
sections for each compressor and associated fans, a con-
trol section and an electrical options section. The power
and control sections have separate hinged, latched, and
gasket sealed doors equipped with wind struts.
Each power compartment contains:
Compressor and fan starting contactors, fan motor ex-
ternal overloads, control circuit serving compressor ca-
pacity control, compressor and fan contactor coils and
compressor motor overloads.
The current transformers for the compressor motor over-
loads sense each phase, as an input to the microproces-
sor. This protects the compressor motors from damage
due to: low current input, high input current, unbal-
anced current, single phasing, phase reversal, and com-
pressor locked rotor.
The control section contains:
ON/OFF switch, microcomputer keypad and display,
microprocessor board, I/O expansion board, relay
boards and power supply board.
The options sections contain:
A control circuit transformer complete with service
switch providing 115/1/Ø power to the unit control
system.
Electrical options as described in “Accessories and
Options.”
Microprocessor Controls
The microprocessor has the following functions and
displays:
• A liquid crystal 40 character display with text pro-
vided on two lines and light emitting diode back-
lighting outdoor viewing.
• A color coded, 35 button, sealed keypad with sec-
tions for Display, Entry, Setpoints, Clock, Print, Pro-
gram and Unit ON/OFF.
The standard controls shall include: brine chilling, ther-
mal storage, automatic pump down, run signal contacts,
demand load limit from external building automation
system input, remote reset liquid temperature reset in-
put, unit alarm contacts, chilled liquid pump control,
automatic reset after power failure, automatic system
optimization to match operating conditions.
The software is stored in non-volatile memory
(EPROM) to eliminate chiller failure due to AC power
failure. The Programmed Setpoint is stored in lithium
battery backed memory.
Motor Current Protection
The microprocessor motor protection provides high cur-
rent protection to assure that the motor is not damaged
due to voltage, excess refrigerant, or other problems
that could cause excessive motor current. This is ac-
complished by sending 3-phase current signals propor-
2
Summary of Contents for Millennium YCAS Series
Page 49: ...49 YORK INTERNATIONAL FORM 201 18 NM4 7 This page intentionally left blank ...
Page 65: ...65 YORK INTERNATIONAL FORM 201 18 NM4 LD04179 7 ...
Page 79: ...79 YORK INTERNATIONAL FORM 201 18 NM4 This page intentionally left blank 7 ...
Page 83: ...83 YORK INTERNATIONAL FORM 201 18 NM4 This page intentionally left blank 7 ...
Page 87: ...87 YORK INTERNATIONAL FORM 201 18 NM4 LD04268 7 ...