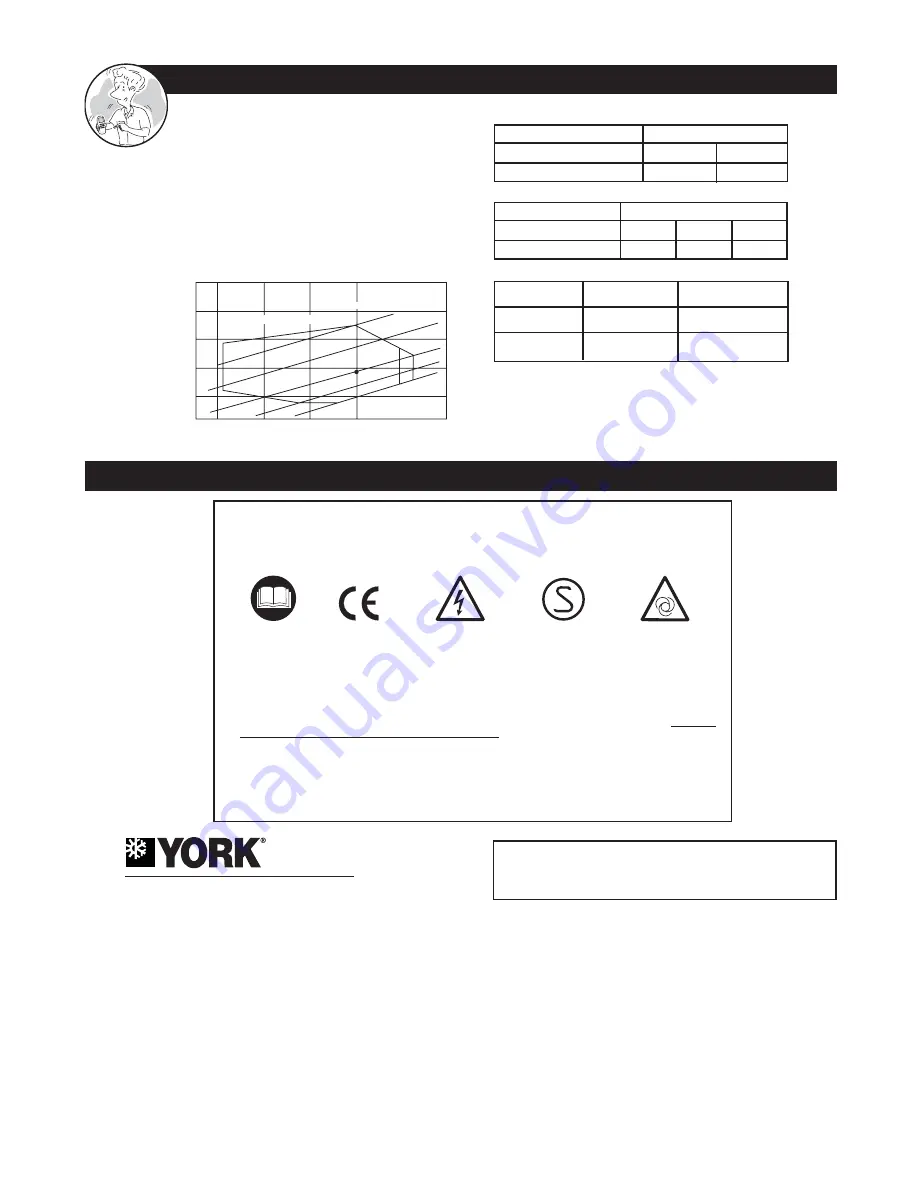
TECHNICAL APPENDIX
Unit Capacity
Total cooling capacity can be determined by using
correction factors C1, C2 and C3.
Given cooling capacity = Cooling capacity at
standard rating conditions x C1 x C2 x C3.
C1 = Capacity correction factor for temperature
C2 = Capacity correction for piping length
C3 = Capacity correction for indoor unit fan speed
Capacity correction factor for temperature
20
10
15
20
25
30
35
25
30
35
40
45
Air intake dry bulb temperature, outdoor unit (CDB)
Inlet air wet b
ulb temperatur
e
, indoor unit (CWB)
R.C.
120%
110%
100%
90%
85%
Capacity correction factor C1
Operating temperature range
DECLARATION OF CONFORMITY
Capacity correction factor for piping length (C2)
Piping length (m)
Correction factor C2
Indoor unit
10
0.98
5
1.00
Cooling mode
Heating mode
Maximum
Minimum
+ 19
º
C
(– 5 with low ambient kit)
– 8
º
C
+ 46
º
C
+ 28
º
C
(heat pump mode)
Fan speed
Correction factor C3
Indoor unit
High
1
Medium
0.90
Low
0.75
R.C.
= Standard rating conditions :
Indoor 27
°
C DB / 19.5
°
C WB
Outdoor 35
°
C DB / 24
°
C WB
Capacity correction factor for indoor fan speed (C3)
Operating temperature limits
DE - COMMISSIONING DISMANTLING & DISPOSAL
This product contains refrigerant under pressure, rotating parts, and electrical connections which may be a
danger and cause injury!
All work must only be carried out by competent persons using suitable protective clothing and safety precautions.
Read the Manual
Risk of electric shock
Unit is remotely
controlled and may
start without warning
1.
Isolate all sources of electrical supply to the unit including any control system supplies switched by the unit. Ensure
that all points of electrical and gas isolation are secured in the OFF position. The supply cables and gas pipework may
then be disconnected and removed. For points of connection refer to unit installation instructions.
2
. Remove all refrigerant from each system of the unit into a suitable container using a refrigerant reclaim or recovery unit.
This refrigerant may then be reused, if appropriate, or returned to the manufacturer for disposal.
Under No
circumstances should refrigerant be vented to atmosphere.
Where appropriate, drain the refrigerant oil from each
system into a suitable container and dispose of according to local laws and regulations governing disposal of oily
wastes.
3.
Packaged unit can generally be removed in one piece after disconnection as above. Any fixing down bolts should be
removed and then unit lifted from position using the points provided and equipment of adequate lifting capacity.
Reference MUST be made to the unit installation instructions for unit weight and correct methods of lifting. Note that
any residual or spilt refrigerant oil should be mopped up and disposed of as described above.
4.
After removal from position the unit parts may be disposed of according to local laws and regulations.
YORK
®
International Corporation
035T83169-001