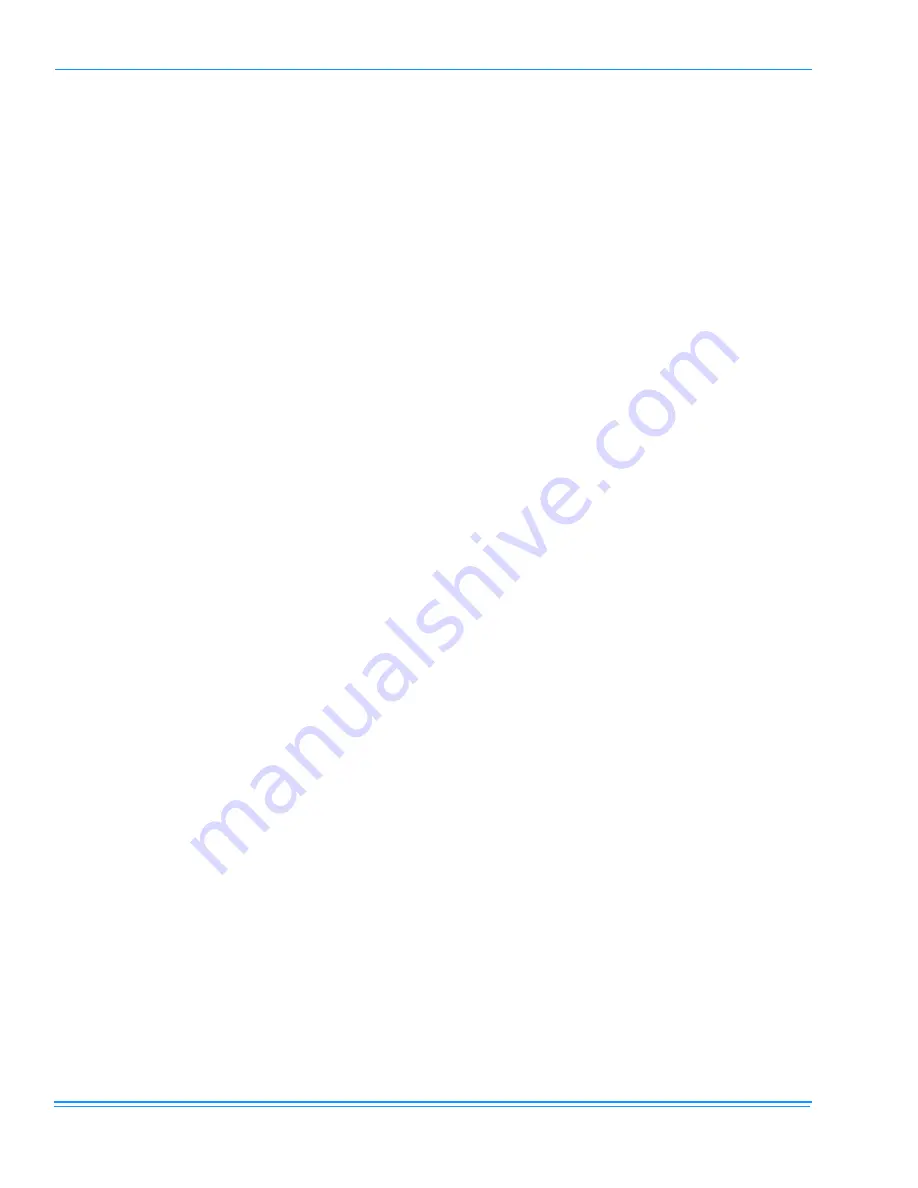
292424-XIM-A-0307
12
Unitary Products Group
6.
Is the control circuit transformer set for the proper volt-
age?
7.
Have the fuses, disconnect switch and power wire been
sized properly?
8.
Are all compressor hold-down nuts properly secured?
9.
Are any refrigerant lines touching each other or any
sheet metal surface? Rubbing due to vibration could
cause a refrigerant leak.
10. Are there any visible signs of a refrigerant leak, such as
oil residue?
11. Is any electrical wire laying against a hot refrigerant line?
INITIAL START-UP
1.
Supply power to the unit through the disconnect switch
at least 8 hours prior to starting the compressor.
2.
Move the system switch on the thermostat to the AUTO
or COOL position.
3.
Reduce the setting of the room thermostat to energize
the compressor.
4.
Check the operation of the evaporator unit per the manu-
facturer's recommendations.
5.
With an ammeter, check the compressor amps against
the unit data plate.
6.
Check for refrigerant leaks.
7.
Check for any abnormal noises and/or vibrations, and
make the necessary adjustments to correct (e.g. fan
blade(s) touching shroud, refrigerant lines hitting on
sheet metal, etc.)
8.
After the unit has been operating for several minutes,
shut off the main power supply at the disconnect switch
and inspect all factory wiring connections and bolted sur-
faces for tightness.
OPERATION
NOTE:
The timing intervals described in the following pro-
cedures are nominal. Some variations will naturally
occur due to differences in individual components,
or due to variations in ambient temperature or line/
control voltage. Refer to the wiring labels inside of
the unit control access panel for additional informa-
tion.
SEQUENCE OF OPERATION
OVERVIEW
These series of condensing units, come factory equipped
with Simplicity™ controls to moni tor all unit functionality and
safety controls.
SAFETY CONTROLS
The Simplicity™ control board incorporates features to moni -
tor safety circuits as well as minimize compressor wear and
damage. An anti-short cycle delay (ASCD) is utilized to pre-
vent operation of a compressor too soon after its previous
run. Additionally, a minimum run time is imposed anytime a
compressor is energized to allow proper oil return to the com-
pressor. The ASCD is initiated on unit start-up and on any
compressor reset or lockout.
The Simplicity™ control board monitors the following inputs
for each cooling system:
•
A high-pressure switch is factory installed to protect
against excessive discharge pressure due to a
blocked condenser coil or a condenser fan motor
failure. During cooling operation, if a high-pressure
limit switch opens, the Simplicity™ control board will
de-energize the associated compressors and initiate
the 5-minute ASCD. If the call for cool is still present
at the end of the ASCD, the control board will re-
energize the halted compressor.
•
If a high-pressure switch opens three times within
two hours of operation, the Simplicity™ control
board will lockout the associated system compres-
sors and will flash an error code (see Table 9 ).
•
A low-pressure switch to protect the unit against
excessively low suction pressure is standard on all
condensing units.
If the low-pressure switch opens during normal operation, the
Simplicity™ control board will de-energize the compressor,
initiate the ASCD, and shut down the condenser fans.
On startup, if the low-pressure switch opens, the Simplicity™
control board will monitor the low-pressure switch to make
sure it closes within one minute. If it fails to close, the unit will
shut down the associated compressor and begin an ASCD. If
the call for cool is still present at the end of the anti-short
cycle time delay, the control board will re-energize the halted
compressor.
If a low-pressure switch opens three times within one hour
of operation, the Simplicity™ control b oard will lock-out the
associated compressor and flash an error code (see Table
9 ).
An ambient air switch will lock out mechanical cooling at 45
°
F
(7°C). In order to operate the unit in ambient temperatures
below 45
°
F (7°C), the optional low ambient kit must be field
installed which will allow the unit to operate during conditions
down to 0
°
F (18°C).
PUMP OUT OPTION
The pump out option is field installed on 15 and 20 ton sys-
tems. The pump out circuit is activated each time the first and