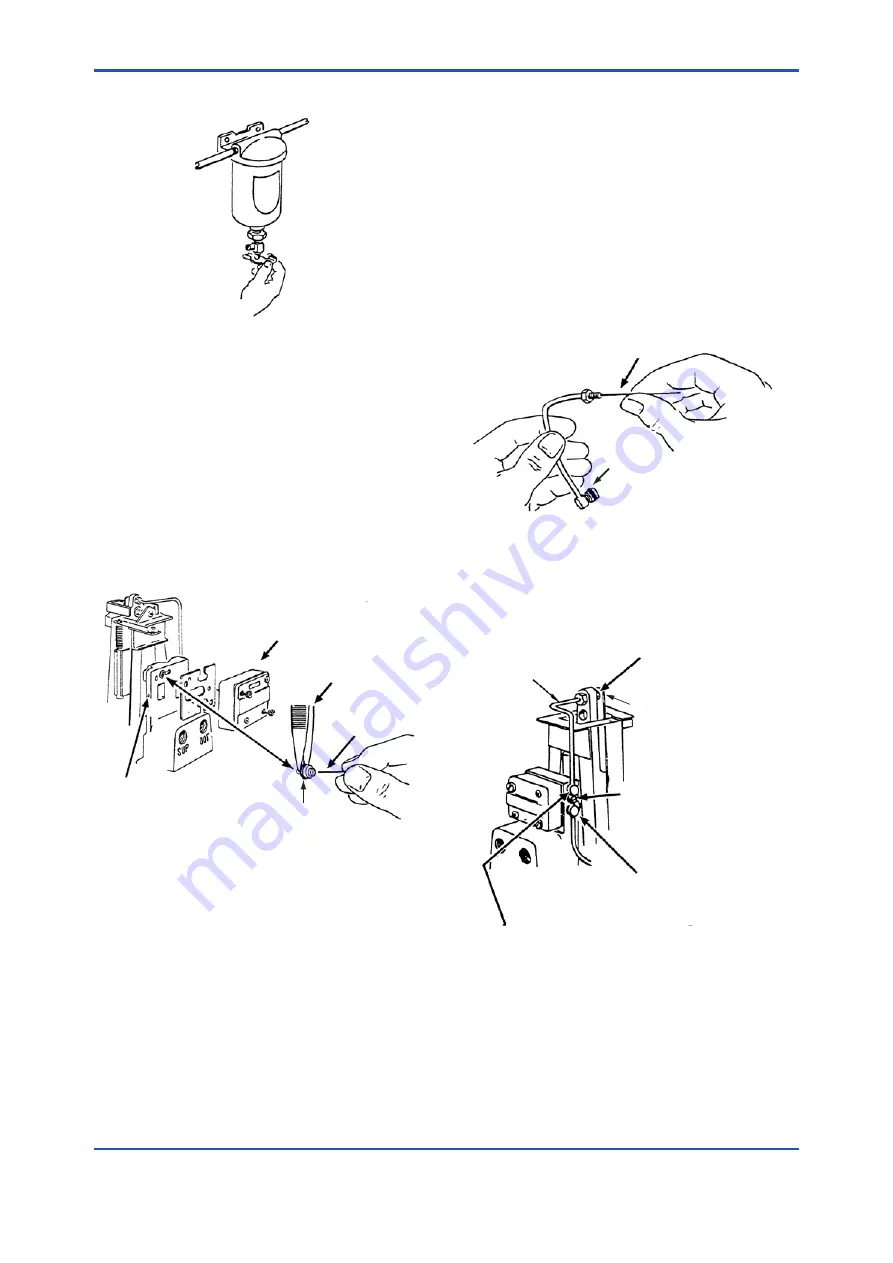
<5. Maintenance>
5-4
IM 02C01B04-01EN
5.2 Supply Air Filter
F0512.ai
Blow filter out at least once a day.
Figure 5.4
Air Filter
5.3 To Clean Restrictor
A plugged restrictor will cause low output pressure.
1. Remove pneumatic amplifier (Refer to section
5.8)
2. Lift out restrictor with tweezers.
3. Clean with a 0.18 mm dia. wire
4. Apply thin film of Vaseline, or similar lubricant to
O-ring.
F0513.ai
Before August. 1975, restrictor was
screwed into side of casting.
Amplifier
Tweezers
Wire
O-ring
Figure 5.5
Cleaning of Restrictor
5.4 To Clean Nozzle Assembly
An accumulation of dirt at the flapper nozzle may
cause a zero shift.
1. Unscrew nozzle nut. Do not let soldered nut on
opposite side of casting turn.
2. Ease nozzle out of casting.
3. Loosen clamp screw and rotate S-clamp.
Withdraw nozzle O-ring connection with twisting
motion. Do not bend tubing.
4. Clean nozzle with 0.73 mm dia. wire,
compressed air, or suitable solvent. Wipe top of
flapper clean.
F0514.ai
Wire
O-ring
5. Before replacing, apply a thin film of Vaseline
or similar lubricant to O-ring. Replace nozzle
assembly in reverse order. Check reference
adjustment (Refer to section 4.1).
F0515.ai
Nozzle O-ring
connection
Feedback O-ring
connection
Nozzle
assembly
Nozzle nut
Nozzle
Clamp screw
Figure 5.6
Cleaning of Nozzle Assembly