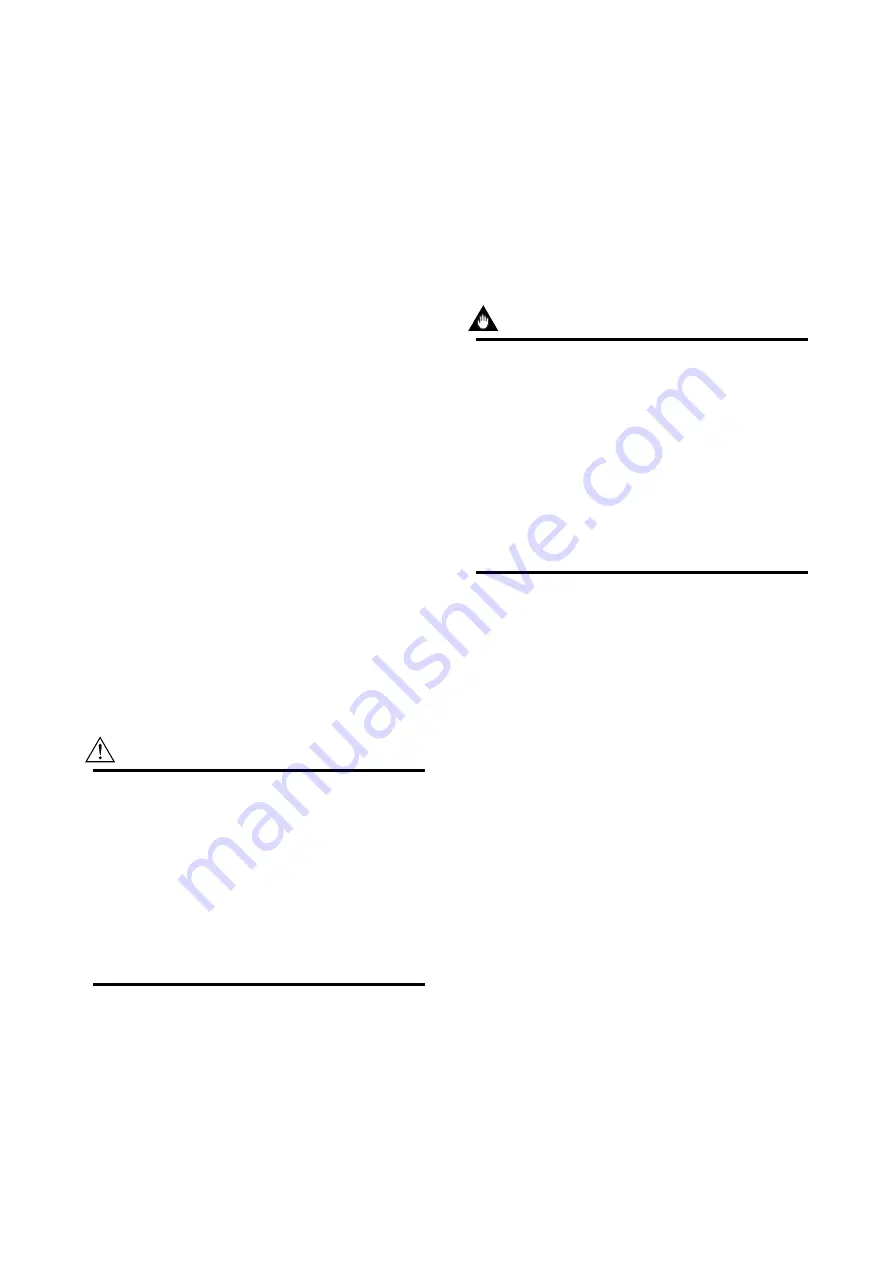
IM 01C25F01-01E
2-2
2. HANDLING CAUTIONS
2.4 Selecting the Installation
Location
The transmitter is designed to withstand severe
environmental conditions. However, to ensure that it
will provide years of stable and accurate performance,
take the following precautions when selecting the
installation location.
(a) Ambient Temperature
Avoid locations subject to wide temperature
variations or a significant temperature gradient. If
the location is exposed to radiant heat from plant
equipment, provide adequate thermal insulation
and/or ventilation.
(b) Ambient Atmosphere
Do not install the transmitter in a corrosive atmo-
sphere. If this cannot be avoided, there must be
adequate ventilation as well as measures to prevent
the leaking of rain water and the presence of
standing water in the conduits.
(c) Shock and Vibration
Although the transmitter is designed to be relatively
resistant to shock and vibration, an installation site
should be selected where this is kept to a minimum.
(d) Installation of Explosion-protected Transmitters
An explosion-protected transmitters is certified for
installation in a hazardous area containing specific
gas types. See subsection 2.9 “Installation of an
Explosion-Protected Transmitters.”
2.5 Pressure Connection
WARNING
• Never loosen the process connection when an
instrument is installed in a process. The device
is under pressure, and a loss of seal can result
in a sudden and uncontrolled release of pro-
cess fluid.
• When draining toxic process fluids that have
condensed inside the pressure detector, take
appropriate steps to prevent the contact of such
fluids with the skin or eyes and the inhalation of
vapors from these fluids.
The following precautions must be observed in order to
safely operate the transmitter under pressure.
(a) Make sure that the process connection is tightened
firmly.
(b) Make sure that there are no leaks in the impulse
piping.
(c) Never apply a pressure higher than the specified
maximum working pressure.
2.6 Waterproofing of Cable
Conduit Connections
Apply a non-hardening sealant to the threads to
waterproof the transmitter cable conduit connections.
(See figure 6.8, 6.9 and 6.10.)
2.7 Restrictions on Use of Radio
Transceivers
IMPORTANT
Although the transmitter has been designed to
resist high frequency electrical noise, if a radio
transceiver is used near the transmitter or its
external wiring, the transmitter may be affected
by high frequency noise pickup. To test this,
start out from a distance of several meters and
slowly approach the transmitter with the trans-
ceiver while observing the measurement loop for
noise effects. Thereafter use the transceiver
outside the range where the noise effects were
first observed.
2.8 Insulation Resistance and
Dielectric Strength Test
Since the transmitter has undergone insulation resis-
tance and dielectric strength tests at the factory before
shipment, normally these tests are not required. If the
need arises to conduct these tests, heed the following:
(a) Do not perform such tests more frequently than is
absolutely necessary. Even test voltages that do not
cause visible damage to the insulation may degrade
the insulation and reduce safety margins.
(b) Never apply a voltage exceeding 500 V DC (100 V
DC with an internal lightning protector) for the
insulation resistance test, nor a voltage exceeding
500 V AC (100 V AC with an internal lightning
protector) for the dielectric strength test.
(c) Before conducting these tests, disconnect all signal
lines from the transmitter terminals. The procedure
for conducting these tests is as follows:
• Insulation Resistance Test
1) Short-circuit the + and – SUPPLY terminals in the
terminal box.
2) Turn OFF the insulation tester. Then connect the
insulation tester plus (+) lead wire to the shorted
SUPPLY terminals and the minus (–) leadwire to
the grounding terminal.