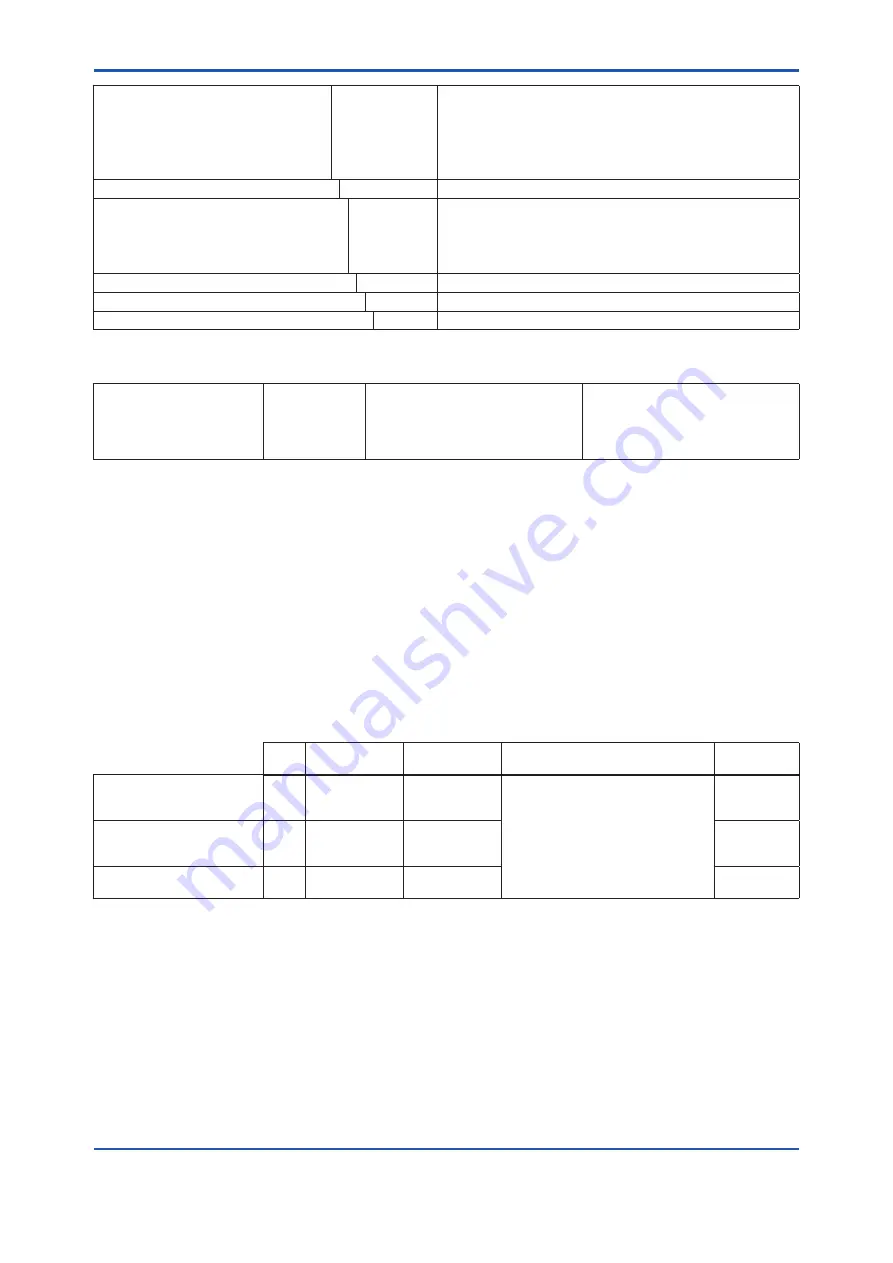
<7. General Specifications>
7-27
IM 01C25W01-01EN
Flange pressure rating
1 ...........................
class150
A ........
10K
H ........
PN10/16
2 ...........................
class300
B ........
20K
K ........
PN25/40
4 ...........................
class600
C ........
30K
L ........
PN64
5 ...........................
class900 *
8
D ........
40K
6 ...........................
class1500 *
8
E ........
63K
Flange type
S .........................
for general use
Flange material
A ......................
JIS S25C
B ......................
304 SST*
4
C ......................
316 SST*
4
S ......................
316L SST*
4
*
15
Extended outside diameter
-0 ..................
None
Extended length
0 .................
None
--------
N ..............
Always N
Table 2g. Diaphragm material and Sealing face material
Wetted parts material
*
1
[Diaphragm material]
[Sealing face material]
SS ........................
[S] 316L SST
[S] 316L SST
HH .......................
[H] Hastelloy C-276*
7
#
[H] Hastelloy C-276*
7
#
TT ........................
[T] Tantalum
[T] Tantalum
*1:
Users must consider the characteristics of selected wetted parts material and the influence of process fluids. The use of
inappropriate materials can result in the leakage of corrosive process fluids and cause injury to personnel and/or damage
to plant facilities. It is also possible that the diaphragm itself can be damaged and that material from the broken diaphragm
and the fill fluid can contaminate the user’s process fluids.
Be very careful with highly corrosive process fluids such as hydrochloric acid, sulfuric acid, hydrogen sulfide, sodium
hypochlorite, and high temperature steam (150°C [302°F] or above). Contact Yokogawa for detailed information of the
wetted parts material.
*2:
Refer to section 12 for limitation of capillary length.
*3:
Not applicable to different size between Process connection size and Flange size.
*4:
Forged version of the material may be used.
*5:
Applicable for Diaphragm material code S and H.
Inside of isolating diaphragms (fill fluid side) are gold plated, effective for hydrogen permeation.
*6:
Not applicable for seal fill fluid code 2.
*7:
Hastelloy C-276 or N10276.
*8:
Not applicable for process connection size code 2.
The ‘#’marks indicate the construction materials conform to NACE material recommendations per MR0175 (2003).
Please refer to latest standards for details.
Table 2h. Process temperature and Ambient temperature
Code
Process
temperature
*
9
Ambient
temperature
*
11
Working pressure
Specific
gravity
*
13
Silicone oil*
10
(high temp. and high
vacuum use)
1
−10 to 250°C
(14 to 482°F)
−10 to 60°C*
12
(14 to 140°F)
0.013 kPa abs
(0.0019 psi abs)
to flange rating pressure
1.07
Silicone oil
(high temp. and high
vacuum use)
2
10 to 315°C
(50 to 599°F)
10 to 60°C*
12
(50 to 140°F)
1.09
Silicone oil
(high vacuum use)
4
−10 to 100°C
(14 to 212°F)
−10 to 60°C*
12
(14 to 140°F)
1.07
Note: The differential pressure transmitter should be installed at least 600 mm below the high pressure (HP) process connection.
However, this value (600 mm) may be affected by ambient temperature, operating pressure, fill fluid or material of the
wetted diaphragm.
Contact YOKOGAWA when the transmitter can not be installed at least 600 mm below the HP process connection.
*9:
See figure 1a, 1b ‘Working Pressure and Process Temperature.’
*10: In case of diaphragm material code T (Tantalum), process temperature limit is up to 200°C (392°F).
*11: This ambient temperature is the transmitter ambient temperature.
*12: In case of process connection size code 2, ambient temperature limit is up to 50°C (122°F).
*13: Approximate values at a temperature of 25°C (77°F)
*14: Not applicable for process connection size code 2.
*15: Not applicable for flange standards code D.