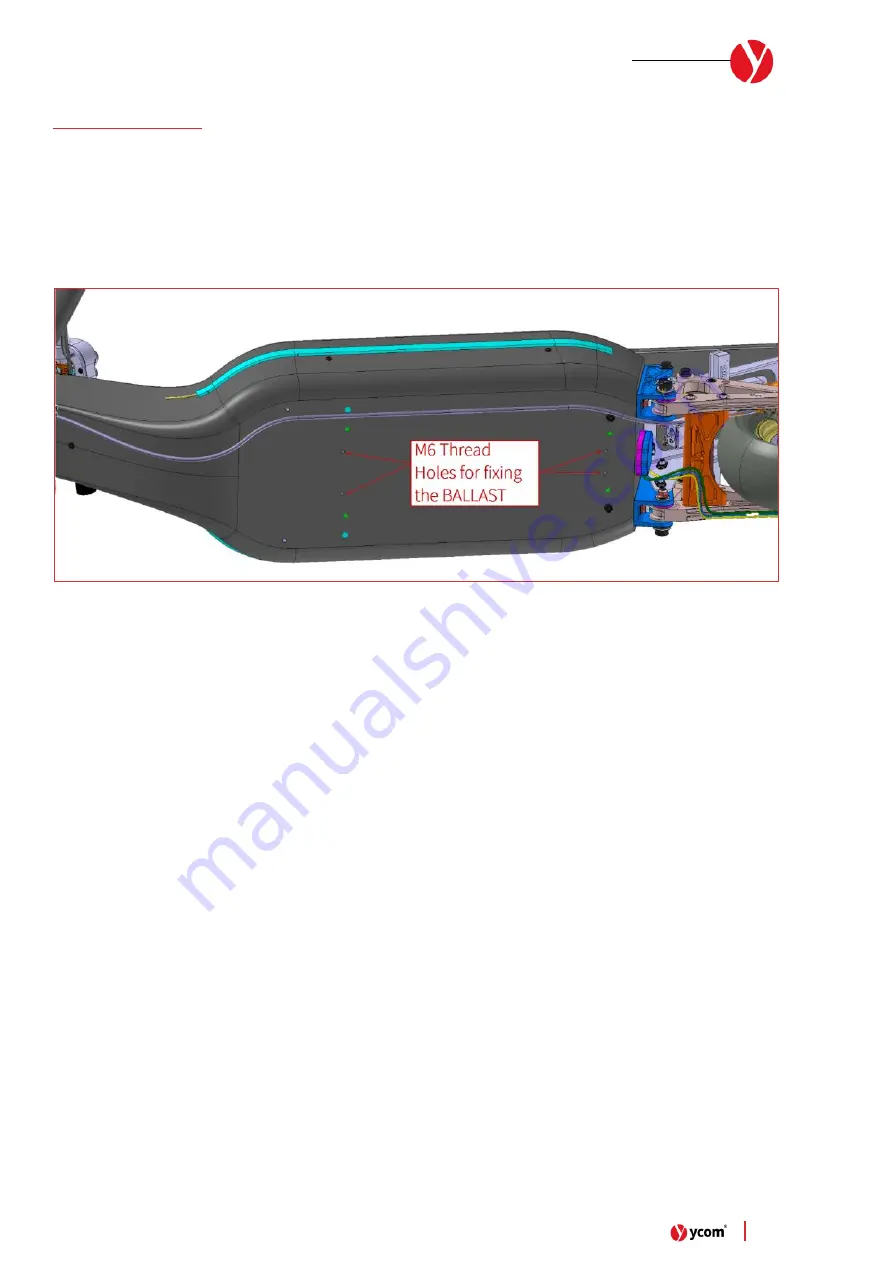
15
|
eSC S1-X
–
User manual
The weight of the vehicle in running condition is 41.5kg.
In case the BOP (Balance of Performance) request is to add weight on the vehicle, there is the possibility to add some
ballast under the chassis on the keel area.
The ballast must be fixed with 4 M6 bolts and its maximum allowed size is 100x405x11 mm.
Image 5
- Space under the chassis for ballast fixing
8.
Weight and Ballast
Summary of Contents for eSC S1-X
Page 1: ...1 eSC S1 X User manual eSC S1 X User Manual TEAMS v2 03 05 2022...
Page 4: ...4 eSC S1 X User manual Image 1 Full Vehicle main views 1 eSC S1 X Vehicle Views...
Page 12: ...12 eSC S1 X User manual Image 2 Standard Setup for Front Fork assembly...
Page 13: ...13 eSC S1 X User manual Image 3 Standard Setup for Rear Fork assembly...
Page 14: ...14 eSC S1 X User manual Image 4 Standard Steering Damper Setup...
Page 18: ...18 eSC S1 X User manual Image 6 Sequence for adjust the steering bearing preload 2 3 4 5 6...
Page 40: ...40 eSC S1 X User manual Image 22 Datalogger main screen...