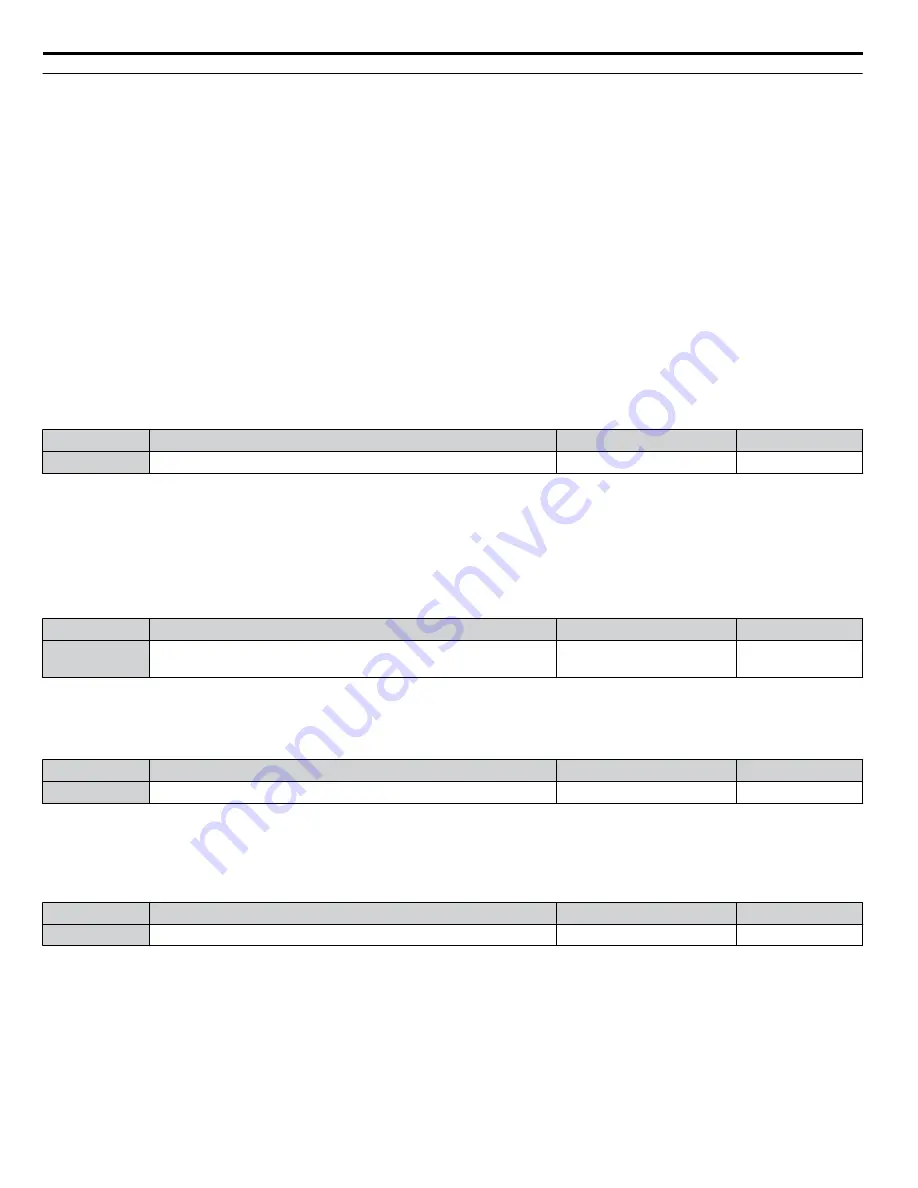
u
n3: High Slip Braking (HSB) and Overexcitation Braking
n
High Slip Braking (V/f)
HSB works in V/f Control only and decreases the stopping time compared to normal deceleration without using dynamic
braking options. HSB reduces the output frequency in large steps to stop the motor and produce a high slip, which dissipates
the regenerative energy created from decelerating the load in the motor windings. Due to the increased temperature of the
motor windings, do not use HSB to frequently stop the motor. The duty cycle should be around 5% or lower.
Notes on Using High Slip Braking
• The set deceleration time is ignored during HSB. Use Overexcitation Deceleration 1 (L3-04 = 4) to stop the motor within a
specified time.
• Braking time varies based on the load inertia and motor characteristics.
• Enabling HSB and KEB Ride-Thru simultaneously will trigger an oPE03 error.
• HSB must be triggered by a digital input set to H1-
oo
= 68. After the HSB command is given, the drive will not restart
until the motor is completely stopped and the Run command is cycled.
• Use parameters n3-01 through n3-04 to adjust HSB.
n
n3-01: High Slip Braking Deceleration Frequency Width
Sets the step width for frequency reduction during HSB. Increase n3-01 if DC bus overvoltage (ov) occurs during HSB.
No.
Name
Setting Range
Default
n3-01
High Slip Braking Deceleration Frequency Width
1 to 20%
5%
n
n3-02: High Slip Braking Current Limit
Sets the maximum current to be output during an HSB stop as a percentage of motor rated current (E2-01). Reducing the
current limit increases the deceleration time. This value must not exceed the current rating of the drive.
• Lower this setting if overvoltage occurs during HSB.
• Lower this setting if motor current is too high during HSB. High current can damage the motor due to overheat.
• The default setting is 120%.
No.
Name
Setting Range
Default
n3-02
High Slip Braking Current Limit
0 to 200%
Determined by
L8-38
n
n3-03: High Slip Braking Dwell Time at Stop
When the motor reaches a relatively low speed at the end of HSB, the output frequency is kept at the minimum output frequency
set to E1-09 for the time set to n3-03. Increase this time if the inertia is very high and the motor coasts after HSB is complete.
No.
Name
Setting Range
Default
n3-03
High Slip Braking Dwell Time at Stop
0.0 to 10.0 s
1.0 s
n
n3-04: High Slip Braking Overload Time
Sets the time required for an HSB overload fault (oL7) to occur when the drive output frequency does not change during an
HSB stop due to excessive load inertia or the load rotating the motor. To protect the motor from overheat, the drive trips with
an oL7 fault if these conditions last longer than the time set in n3-04.
No.
Name
Setting Range
Default
n3-04
High Slip Braking Overload Time
30 to 1200 s
40 s
n
Overexcitation Deceleration (Induction Motors)
Increases the flux during deceleration and allows shorter deceleration time settings. Enabled by setting L3-04 to 4 or 5.
to L3-04: Stall Prevention Selection during Deceleration on page 106
.
Notes on Overexcitation Deceleration
• Frequently applying Overexcitation Deceleration raises the motor temperature because regenerative energy is mainly
dissipated as heat in the motor. In cases where frequent application is required, make sure the motor temperature does not
exceed the maximum allowable value of Overexcitation Deceleration.
• During Overexcitation Deceleration 2, Hunting Prevention in V/f Control is disabled.
1.9 n: Special Adjustments
124
YASKAWA SIEP YAIZ1U 03B YASKAWA AC Drive – Z1000 Programming Manual
Summary of Contents for Z1000 CIMR-ZU*A Series
Page 339: ......