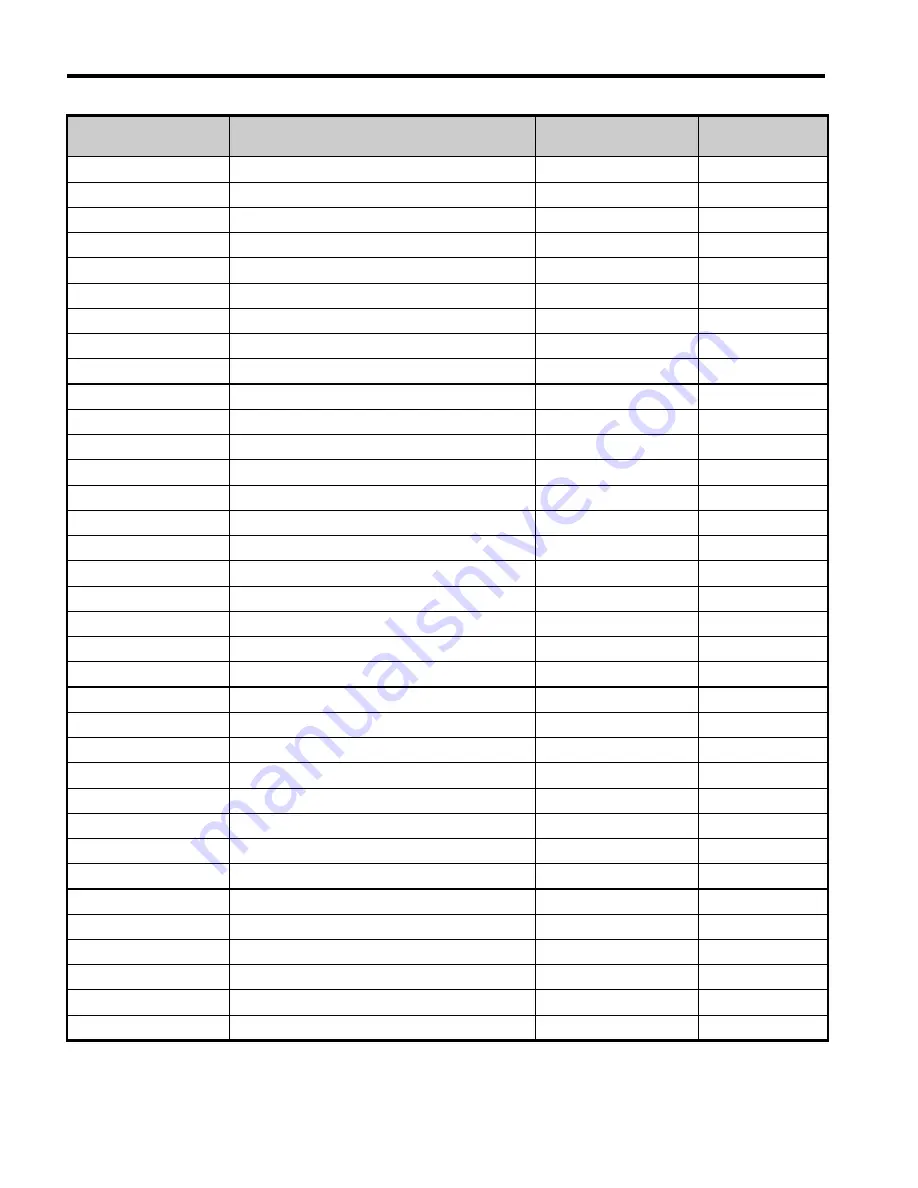
9 Fault Diagnosis and Possible Solutions
EN 28
YASKAWA Europe
YEU TOEP C710606 87A - V1000 Option Powerlink - Installation Manual
2310
Motor overload
oL1
0x0B
2221
Drive overload
oL2
0x0C
2311
Overtorque detection 1
oL3
0x0D
2312
Overtorque detection 2
oL4
0x0E
5420
Braking transistor fault
rr
0x0F
4410
Internal braking resistor overheat
rH
0x10
5441
External fault 3
EF3
0x11
5442
External fault 4
EF4
0x12
5443
External fault 5
EF5
0x13
5444
External fault 6
EF6
0x14
FF17
Cooling FAN fault
FAn
0x17
7180
Motor over speed (control mode using PG)
oS
0x18
8321
Speed deviation (control mode using PG)
dEv
0x19
7305
PG fault (control mode using PG)
PGo
0x1A
3130
Input phase loss
PF
0x1B
3300
Output phase loss
LF
0x1C
FF01
Motor overheat alarm
oH3
0x1D
5300
Digital operator disconnected
oPr
0x1E
5530
EEPROM error
Err
0x1F
FF08
MEMOBUS/Modbus Error
CE
0x21
FF07
BUS error
bUS
0x22
FF06
Control fault
CF
0x25
5481
Fault input from option card
EF0
0x27
FF02
PID feedback lost
FbL
0x28
FF03
Undertorque detected 1
UL3
0x29
FF04
Undertorque detected 2
UL4
0x2A
FF05
High slip braking OL
oL7
0x2B
FF31
Intermediary voltage fault
VCF
0x31
FF36
Output current imbalance
LF2
0x36
FF3B
Too many speed search restarts
SEr
0x3B
FF41
PID feedback loss
FbH
0x41
FF0D
External fault at input terminal S1
EF1
0x42
FF0E
External fault at input terminal S2
EF2
0x43
FF44
Mechanical weakening detection 1
oL5
0x44
FF45
Mechanical weakening detection 2
UL5
0x45
Error Code (Hex)
Meaning
Drive Display
INVR:0x0080
Enum Value