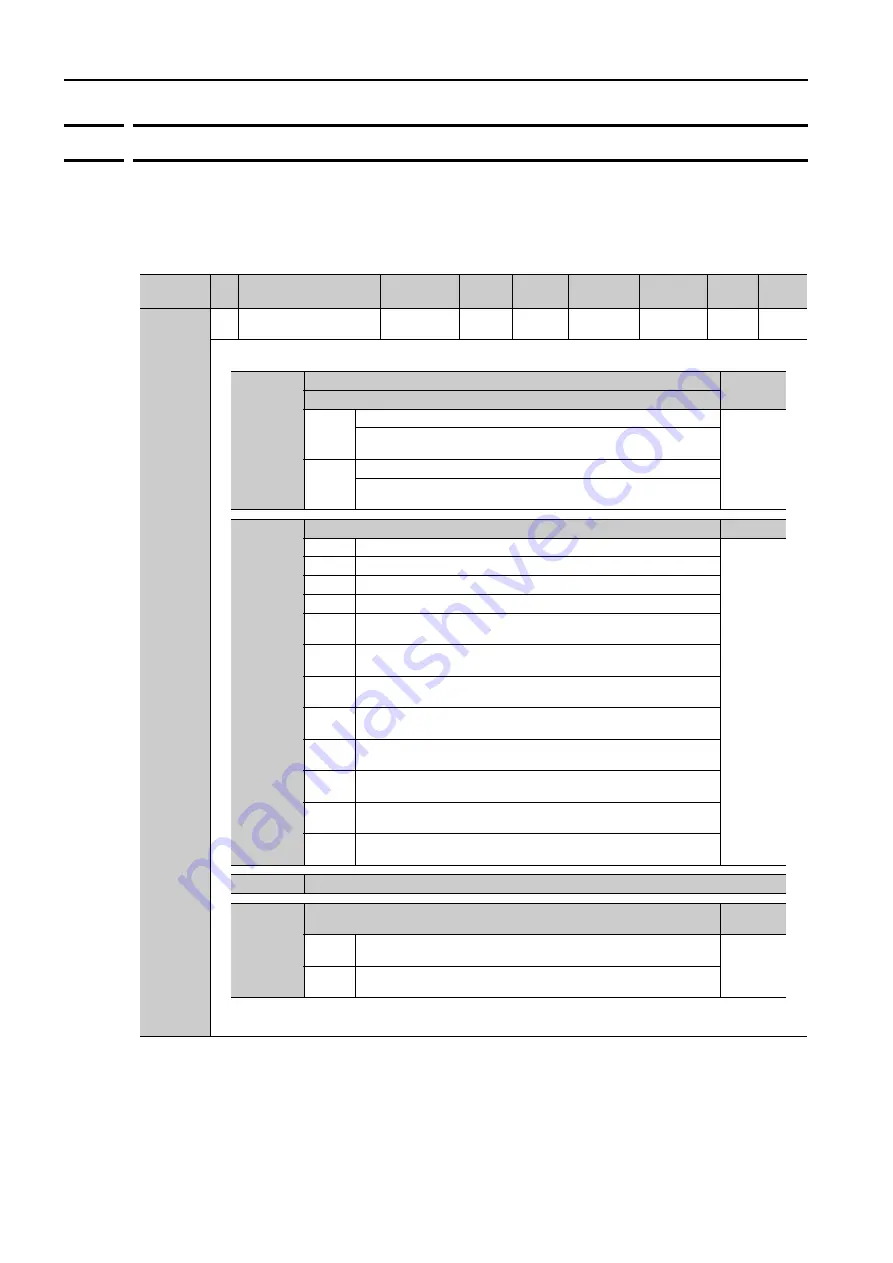
9.2 List of Parameters
9.2.2 List of Parameters
9-4
9.2.2
List of Parameters
The following table lists the parameters.
Note: Do not change the following parameters from their default settings.
•
Reserved parameters
•
Parameters not given in this manual
•
Parameters that are not valid for the Servomotor that you are using, as given in the parameter table
Parameter
No.
Siz
e
Name
Setting
Range
Setting
Unit
Default
Setting
Applicable
Motors
When
Enabled
Classi-
fication
Refer-
ence
Pn000
2
Basic Function Selec-
tions 0
0000h to
10B1h
–
0010h
All
After
restart
Setup
–
Continued on next page.
n.
X
Rotation Direction Selection
Reference
Movement Direction Selection
0
Use CCW as the forward direction.
*1
Use the direction in which the linear encoder counts up as the for-
ward direction.
1
Use CW as the forward direction. (Reverse Rotation Mode)
Use the direction in which the linear encoder counts down as the
forward direction. (Reverse Movement Mode)
n.
X
Control Method Selection
Reference
0
Speed control with analog references
*1
1
Position control with pulse train references
2
Torque control with analog references
3
Internal set speed control with contact commands
4
Switching between internal set speed control with contact refer-
ences and speed control with analog references
5
Switching between internal set speed control with contact refer-
ences and position control with pulse train references
6
Switching between internal set speed control with contact refer-
ences and torque control with analog references
7
Switching between position control with pulse train references and
speed control with analog references
8
Switching between position control with pulse train references and
torque control with analog references
9
Switching between torque control with analog references and
speed control with analog references
A
Switching between speed control with analog references and
speed control with zero clamping
B
Switching between position control with pulse train references and
position control with reference pulse inhibition
n.
X
Reserved parameter (Do not change.)
n.X
Rotary/Linear Servomotor Startup Selection When Encoder Is Not Con-
nected
Reference
0
When an encoder is not connected, start as SERVOPACK for
Rotary Servomotor.
*1
1
When an encoder is not connected, start as SERVOPACK for
Linear Servomotor.