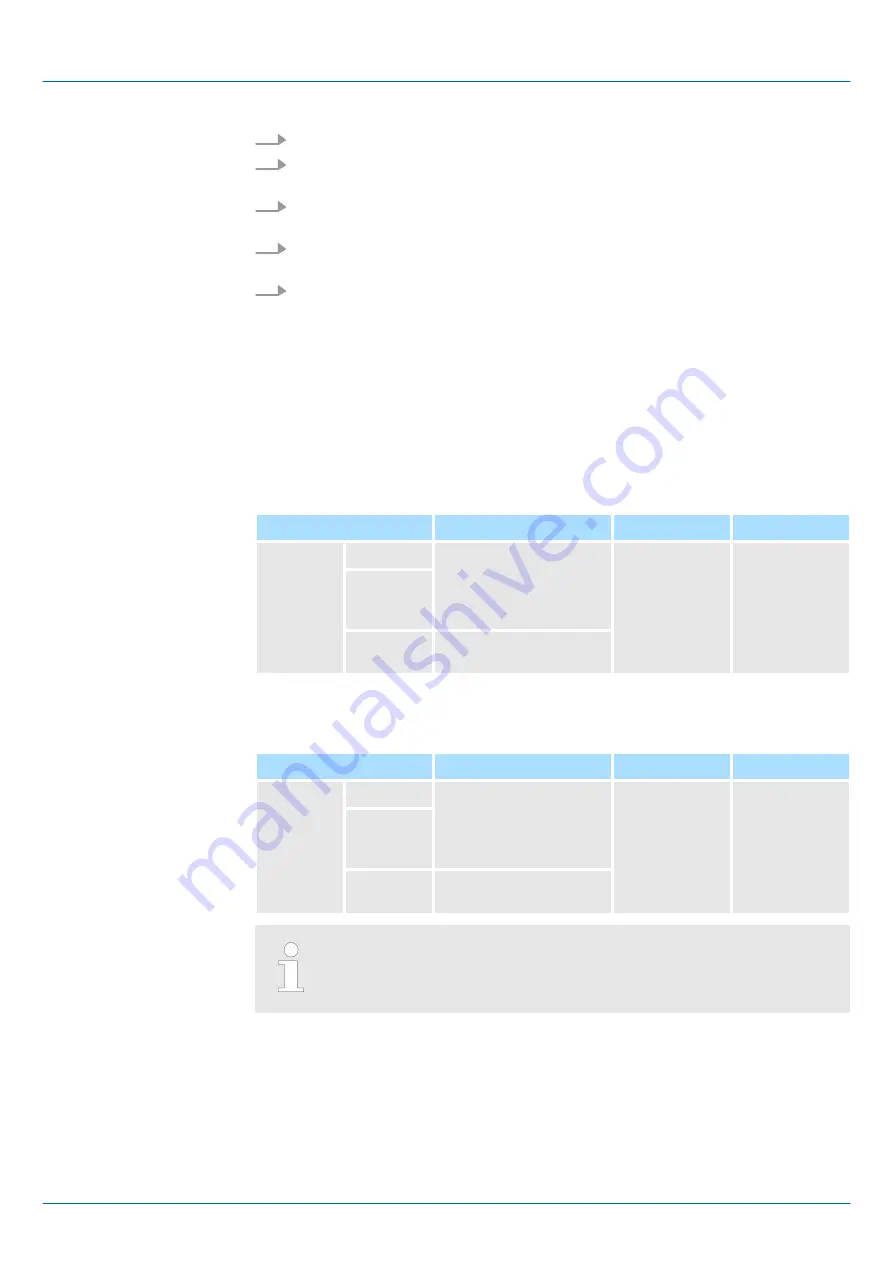
1.
Set Pn475 to n.
1 (Enable gravity compensation).
2.
To enable changes to the settings, turn the power supply to the SERVOPACK OFF
and ON again.
3.
Use S or an analog monitor to find the torque reference value when the
motor is stopped with the servo ON.
4.
Set the torque reference value found in step 3 in Pn476 (Gravity Compensation
Torque).
5.
Turn the servo ON and OFF a few times and fine-tune Pn476 so that the moving
part of the machine does not fall.
9.13.5
Current Control Mode Selection
Current control mode selection reduces high-frequency noise while the Servomotor is
being stopped.
The setting depends on the capacity of the SERVOPACK.
SERVOPACK Models SGD7S-R70A, -R90A, -1R6A, -2R8A, -3R8A, -5R5A, and -7R6A
Parameter
Function
When Enabled Classification
Pn009
n.
0
Use current control
mode 1.
After restart
Tuning
n.
1
(default
setting)
n.
2
Use current control
mode 2 (low noise).
SERVOPACK Models SGD7S-120A, -180A, -200A, -330A, -470A, -550A, -590A, and
-780A
Parameter
Function
When Enabled Classification
Pn009
n.
0
Use current control
mode 1.
After restart
Tuning
n.
1
(default
setting)
n.
2
Use current control
mode 2 (low noise).
If current control mode 2 is selected, the load ratio may increase while
the Servomotor is being stopped.
Sigma-7 Series SERVOPACKs
Tuning
Additional Adjustment Functions > Current Control Mode Selection
| | PROFINET Communications - SIEP YEUOC7P 02A Revision 0 | en |
398