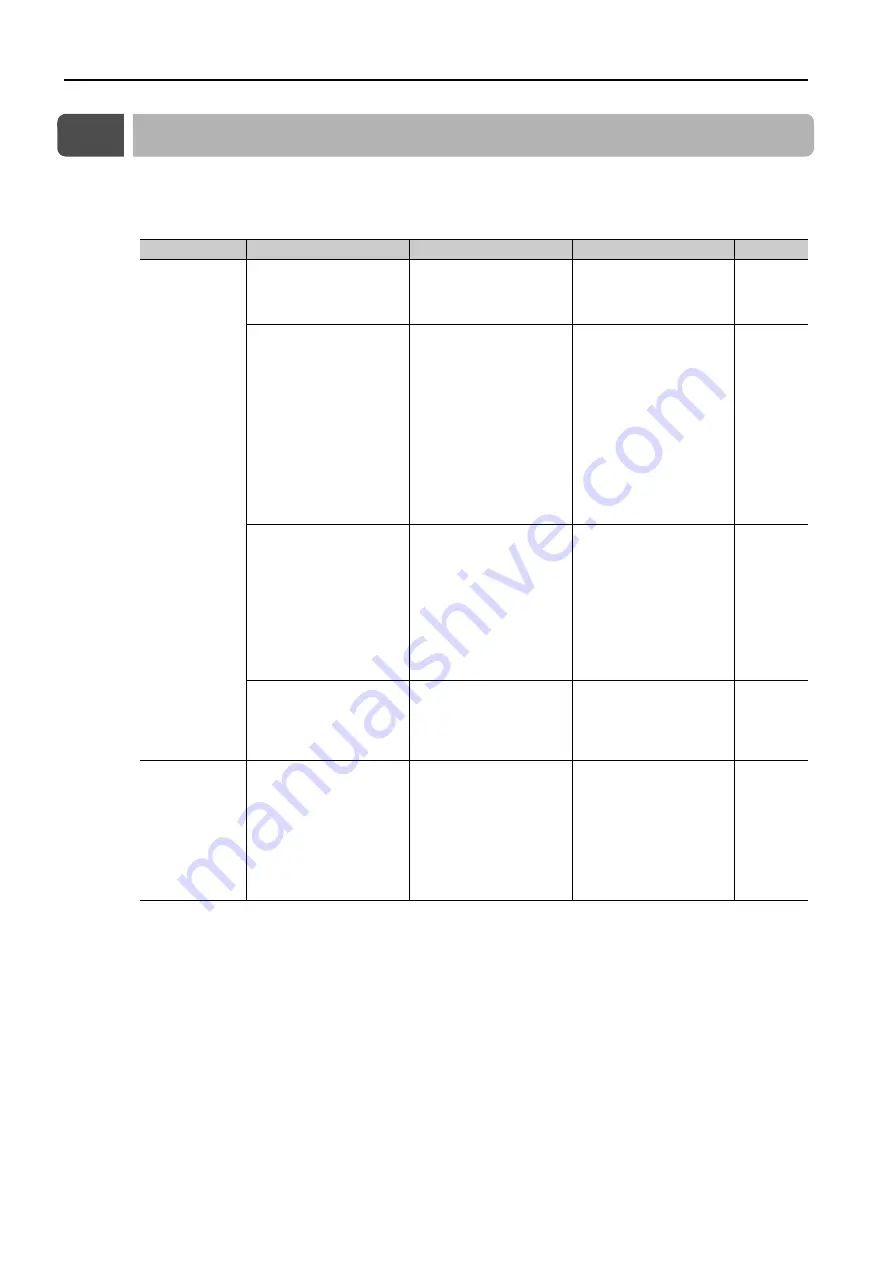
6.2 Troubleshooting Based on the Operation and Conditions of the Servomotor
6-6
6.2
Troubleshooting Based on the Operation and Conditions of the Servomotor
This section provides troubleshooting for problems related to the dynamic brake hardware
option specifications based on the operation and conditions of the Servomotor, including
causes and corrections.
Problem
Possible Cause
Confirmation
Correction
Reference
Dynamic Brake
Does Not
Operate
The setting of Pn001 =
n.
X (Servo OFF or
Alarm Group 1 Stopping
Method) is not suitable.
Check the setting of
Pn001 = n.
X.
Set Pn001 = n.
X
correctly.
–
Dynamic brake resistor is
disconnected.
Check the moment of
inertia, motor speed, and
dynamic brake frequency
of use. The dynamic
brake resistor may be
disconnected if there
was excessive moment
of inertia, excessive
motor speed, excessive
use of the dynamic
brake, or if a suitable
external dynamic brake
has not been selected.
Turn OFF the power sup-
ply to the servo system.
Replace the SERVO-
PACK. To prevent dis-
connection, reduce the
load.
–
The dynamic brake drive
circuit failure.
–
Turn OFF the power sup-
ply to the servo system.
A part in the dynamic
brake circuit has failed.
Replace the SERVO-
PACK. Take measures to
reduce the load in order
to prevent damage to the
dynamic brake drive cir-
cuit.
–
The external dynamic
brake resistor is not con-
nected properly.
Check the connection
status.
Turn OFF the power sup-
ply to the servo system.
Connect the selected
dynamic brake resistor
correctly.
–
An External
Dynamic Brake
Resistor
Cannot Be
Connected
A SERVOPACK to which
an external dynamic
brake resistor cannot be
connected (SGD7S-
R70A to -2R8A or
SGD7W-1R6A to -2R8A)
is in use.
Check the SERVOPACK
model.
Turn OFF the power sup-
ply to the servo system.
Select another SERVO-
PACK.
(Use a SERVOPACK that
accepts an externally
connected dynamic
brake resistor or a stan-
dard SERVOPACK.)
–