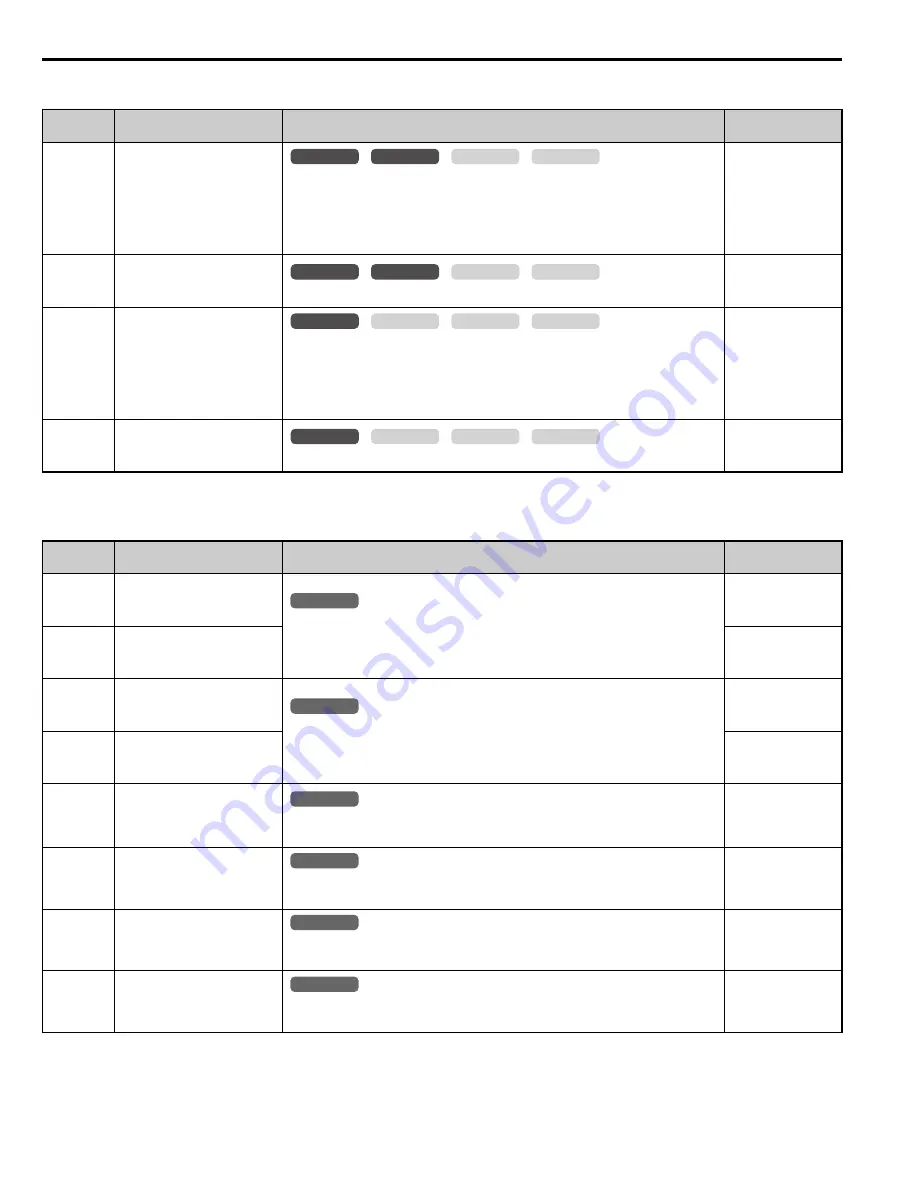
B Parameter Table
190
YASKAWA
TOEPYAIL1E01A YASKAWA AC Drive L1000E Quick Start Guide
L3: Stall Prevention
L4: Speed Detection
No.
(Addr.)
Name
Description
Setting
L3-01
(48FH)
<16> The setting value is dependent on the setting for the carrier frequency reduction (L8-38).
Stall Prevention Selection
during Acceleration
0: Disabled.
1: General purpose. Acceleration is paused as long as the current is above the
L3-02 setting.
2: Intelligent. Accelerate in the shortest possible time without exceeding the L3-
02 level.
Default: 1
Min: 0
Max: 2
L3-02
(490H)
Stall Prevention Level during
Acceleration
Used when L3-01 = 1 or 2. 100% is equal to the drive rated current.
Default:
Min: 0%
Max: 150%
L3-05
(493H)
Stall Prevention Selection
during Run
0: Disabled. Drive runs at a set frequency. A heavy load may cause speed loss.
1: Decel time 1. Uses the deceleration ramp set to C1-02 while Stall Prevention
is performed.
2: Decel time 2. Uses the deceleration ramp set to C1-04 while Stall Prevention
is performed.
Default: 1
Min: 0
Max: 2
L3-06
(494H)
Stall Prevention Level during
Run
Enabled when L3-05 is set to 1 or 2. 100% is equal to the drive rated current.
Default:
Min: 30%
Max: 150%
No.
(Addr.)
Name
Description
Setting
L4-01
(499H)
Speed Agreement Detection
Level
L4-01 sets the speed detection level for digital output functions H2-
= 3, 4,
5.
L4-02 sets the hysteresis or allowable margin for speed detection.
Default: 0.0%
Min: 0.0%
Max: 100.0%
L4-02
(49AH)
Speed Agreement Detection
Width
Default: 4.0%
Min: 0.0%
Max: 40.0%
L4-03
(49BH)
Speed Agreement Detection
Level (+/-)
L4-03 sets the speed detection level for digital output functions H2-
= 13,
14, 15, 16.
L4-04 sets the hysteresis or allowable margin for speed detection.
Default: 0.0%
Min: –100.0%
Max: 100.0%
L4-04
(49CH)
Speed Agreement Detection
Width (+/-)
Default: 4.0%
Min: 0.0%
Max: 40.0%
L4-05
(49DH)
Speed Reference Loss
Detection Selection
0: Stop. Drive stops when the speed reference is lost.
1: Run. Drive runs at a reduced speed when the speed reference is lost.
Default: 0
Min: 0
Max: 1
L4-06
(4C2H)
Speed Reference at
Reference Loss
Sets the percentage of the speed reference that the drive should run with when
the speed reference is lost.
Default: 80%
Min: 0.0%
Max: 100.0%
L4-07
(470H)
Speed Agree Detection Selection
0: No detection during baseblock
1: Detection always enabled
Default: 0
Min: 0
Max: 1
L4-13
(4F6H)
Door Zone Level
Sets the door zone speed level. The "door zone" multi-function digital output is
closed when the speed falls below this level.
Default: 0.0%
Min: 0.0%
Max: 100.0%
common
_
CLV
CLV/PM
V/f
OLV
common
_
CLV
CLV/PM
V/f
OLV
common
_
CLV
CLV/PM
V/f
OLV
common
_
CLV
CLV/PM
V/f
OLV
All Modes
common
_
All Modes
common
_
All Modes
common
_
All Modes
common
_
All Modes
common
_
All Modes
common
_