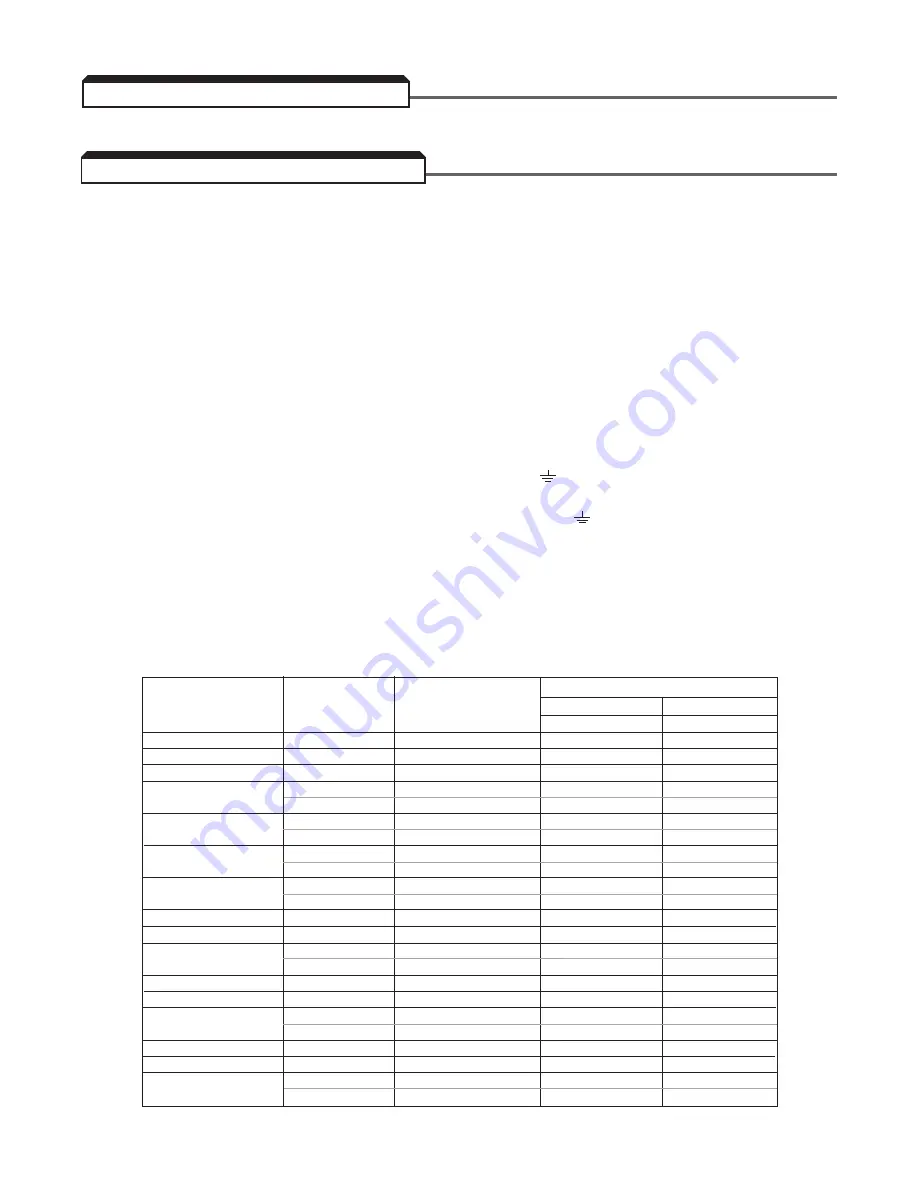
All basic interconnections (using the Digital Operator) are shown in Figures 1-3 and 1-4.
1 . 4 . 1 M a i n C i r c u i t I n p u t / O u t p u t
Complete wire interconnections according to Table 1-2, Figure 1-3 and Figure 1-4. Be sure to
observe the following:
• Use 600V vinyl-sheathed wire or equivalent. Wire size and type should be determined by local
electrical codes.
• Avoid routing power wiring near equipment sensitive to electrical noise.
• Avoid running input and output wiring in the same conduit.
• NEVER connect AC main power to output terminals T1(U), T2(V), and T3(W).
• NEVER allow wire leads to contact metal surfaces. Short-circuit may result.
• NEVER connect power factor correction capacitors to the drive output. Consult
Yaskawa when connecting noise filters to the drive output.
• WIRE SIZING MUST BE SUITABLE FOR CLASS I CIRCUITS.
• When connecting motor to drive’s output terminals, include a separate ground wire. Attach ground
wire solidly to motor frame and to drive’s ground terminal.
• When using armored or shielded cable for connection between drive and motor, solidly connect
armor or shield to motor frame, and to drive’s ground terminal.
• Motor lead length should NOT EXCEED 164 feet (50 meters), and motor wiring should be run in
a separate conduit from other power wiring. If lead length must exceed this distance, reduce
carrier frequency (see paragraph 5.8) and consult factory for proper installation procedures.
• Use UL listed closed loop connectors or CSA certified ring connectors sized for the selected wire
gauge. Install connectors using the correct crimp tool recommended by the connector
manufacturer.
1-2
1.4 ELECTRICAL INSTALLATION
WIRE SIZE
TERMINAL
CLOSED-LOOP
CLAMPING TORQUE
AWG
mm
2
SCREW
CONNECTOR
STEEL
COPPER
lb-in
N-m
lb-in
N-m
20
0.5
M3.5
1.25 - 3.5
7.8
0.9
7.0
0.8
18
0.75
M4
1.25 - 4
13.0
1.5
10.4
1.2
16
1.25
M4
1.25 - 4
13.0
1.5
10.4
1.2
M4
2 - 4
13.0
1.5
10.4
1.2
14
2
M5
2 - 5
26.1
20.9
3.1
2.4
M4
3.5 - 4
13.0
1.5
10.4
1.2
12
3.5
M5
3.5 - 5
26.1
20.9
3.1
2.4
M4
5.5 - 4
13.0
1.5
10.4
1.2
10
5.5
M5
5.5 - 5
26.1
20.9
3.1
2.4
M5
8 - 5
26.1
20.9
3.1
2.4
8
8
M6
8 - 6
40.9
34.8
4.8
4.1
6
14
M6
14 - 6
40.9
34.8
4.8
4.1
4
22
M8
22 - 8
100.0
82.6
11.7
10.7
M8
38 - 8
100.0
82.6
11.7
10.7
2
38
M10
38 - 10
182.6
156.5
21.4
18.4
1/0
60
M10
60 - 10
182.6
156.5
21.4
18.4
3/0
80
M10
80 - 10
182.6
156.5
21.4
18.4
M10
100 - 10
182.6
156.5
21.4
18.4
4/0
100
M12
100 - 12
313.0
191.3
36.7
23.1
MCM300
150
M12
150 - 12
313.0
191.3
36.7
23.1
MCM400
200
M12
200 - 12
313.0
191.3
36.7
23.1
M12
325 - 12
313.0
191.3
36.7
23.1
MCM650
325
M16
325 - 16
313.0
191.3
36.7
23.1
Summary of Contents for GPD515C
Page 1: ...GPD 515 G5 Drive Technical Manual Models GPD515C and CIMR G5M Document Number TM 4515...
Page 17: ...1 16...
Page 20: ...1 19...