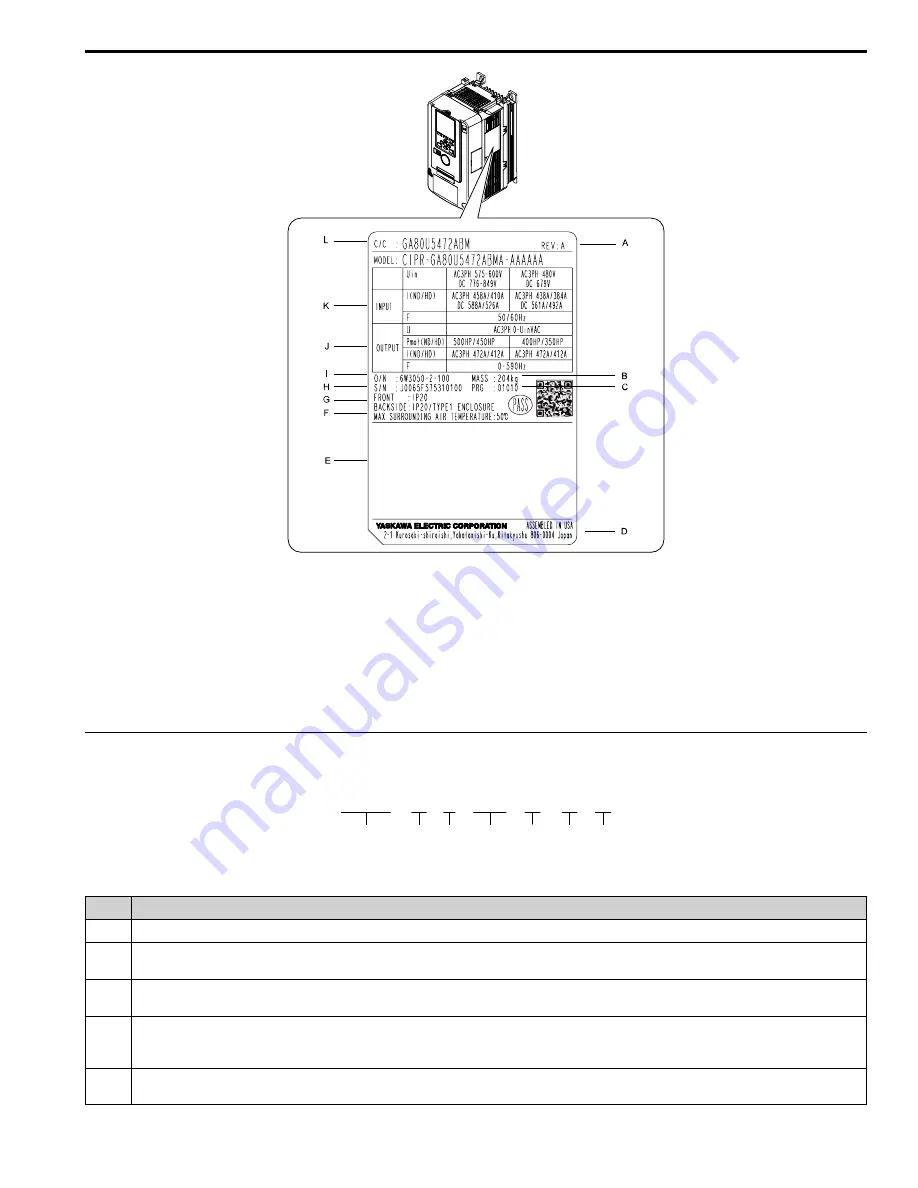
YASKAWA
TOEPC7106170VA GA800 600 V Drive Installation & Primary Operation
9
A - Product Revision
B - Weight
C - Drive software version
D - The address of the head office of Yaskawa
Electric Corporation
E - Standards compliance
F - Surrounding air temperature
G - Enclosure protection design
H - Serial number
I - Lot number
J - Output specifications
K - Input specifications
L - Catalog code
Figure 4.1 Nameplate Example
◆
How to Read the Catalog Code
Use the information in
and
to read the drive catalog codes.
Figure 4.2 Drive Catalog Code
Table 4.1 Catalog Code Details
No.
Description
1
GA800 Series
2
Region code
•
U: Americas
3
Input power supply voltage
•
5: Three-Phase AC 600 V
4
Rated output current
Note:
Refer to the rated output current list for more information.
5
EMC noise filter
A: No built-in EMC filter
GA80 U 5 382 A B M
1
2
3
4
5
6
7