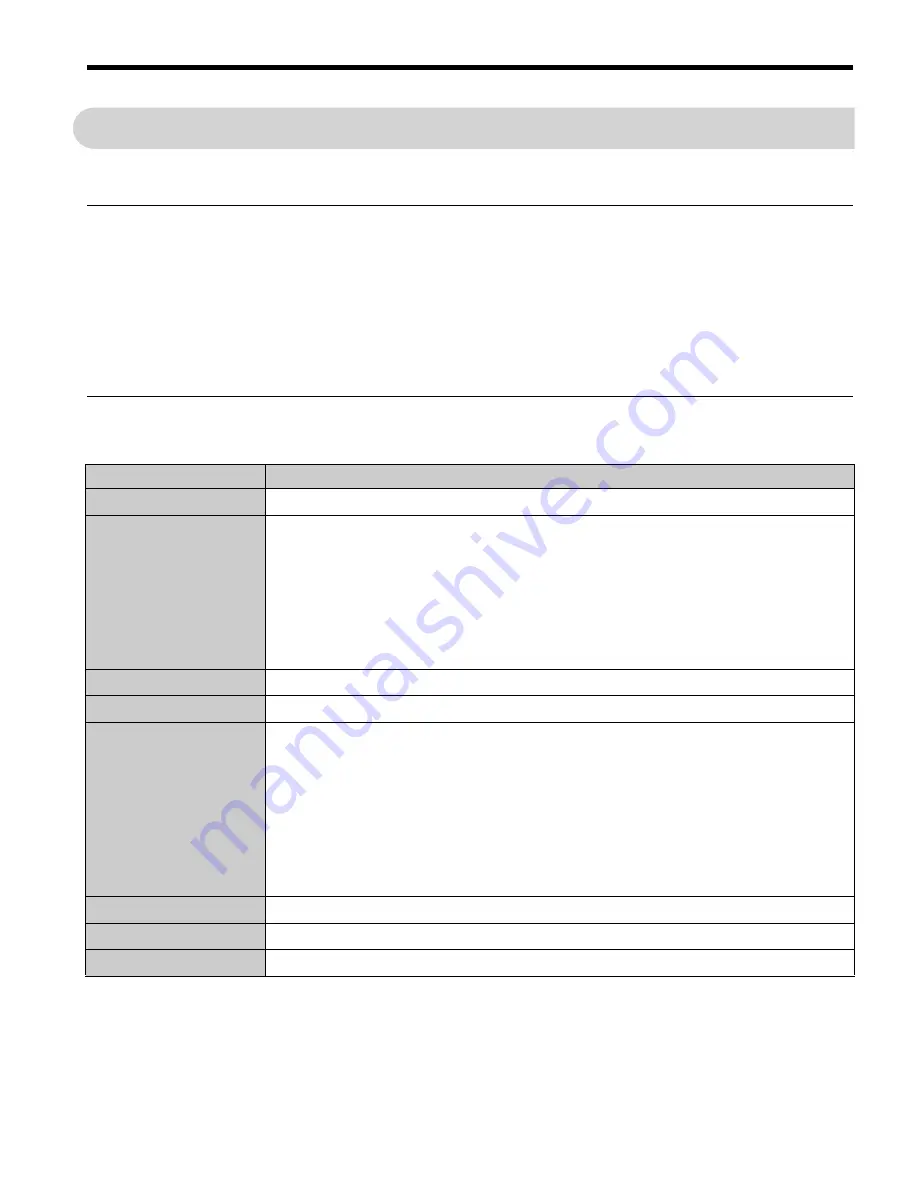
ENGLISH
2 Mechanical Installation
YASKAWA Europe
TOEP C710606 15C YASKAWA AC Drive - V1000 Quick Start Guide
EN 7
2
Mechanical Installation
Upon Receipt
Please perform the following tasks after receiving the drive:
• Inspect the drive for damage. If the drive appears damaged upon receipt, contact your sup-
plier.
• Verify receipt of the correct model by checking the information on the nameplate. If you
have received the wrong model contact your supplier.
Installation Environment
For optimum performance life of the drive, install the drive in an environment that meets the
conditions listed below.
Environment
Conditions
Installation Area
Indoors
Ambient Temperature
-10
°
C to +40
°
C (NEMA Type 1)
-10
°
C to +50
°
C (Open-Chassis Type)
When using an enclosure panel, install a cooling fan or air conditioner in the
area to ensure that the air temperature inside the enclosure does not exceed the
specified levels.
Do not allow ice to develop on the drive.
Humidity
95% RH or less and free of condensation
Storage Temperature
-20
°
C to +60
°
C
Surrounding Area
Install the drive in an area free from:
• oil mist and dust
• metal shavings, oil, water or other foreign materials
• radioactive materials
• combustible materials (e.g., wood)
• harmful gases and liquids
• excessive vibration
• chlorides
• direct sunlight
Altitude
1000 m or less
Vibration
10 - 20 Hz at 9.8 m/s
2
, 20 - 55 Hz at 5.9 m/s
2
Orientation
Install the drive vertically to maintain maximum cooling effects.